Introduction
Plastic injection molding is the backbone of modern manufacturing, enabling mass production of precise, durable components. Yet, B2B clients face three critical challenges: cost optimization, material selection, and high-volume efficiency. This guide dives deep into these priorities, backed by industry data, real-world case studies, and comparisons of top thermoplastics like ABS, polypropylene (PP), and polycarbonate (PC).
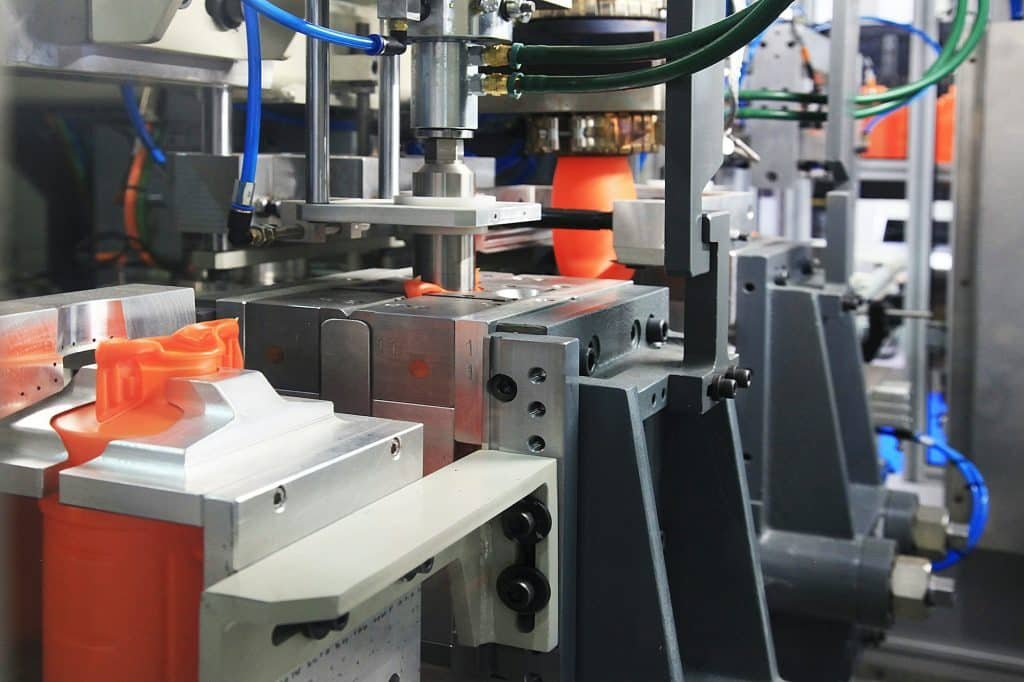
Plastic Injection Molding Cost Optimization Strategies
1.1 Reducing Cycle Times Without Sacrificing Quality
Cycle time directly impacts costs. For example, reducing a 30-second cycle by 10% saves $18,000 annually per machine. Techniques include:
- Mold temperature control: Maintain ±2°C variation to prevent defects.
- Automated ejection systems: Cut downtime by 15%.

1.2 Material Waste Minimization
The average plant wastes 4-8% of raw materials. Solutions:
- Regrind integration: Blend 20-30% regrind with virgin resin.
- AI-driven predictive analytics: Reduce overfills by 12%.
Case Study: Automotive supplier TechMold Inc. slashed costs by 22% using IoT-enabled real-time monitoring and regrind optimization.
Thermoplastic Material Selection Guide for B2B Buyers
2.1 Key Properties Comparison: ABS vs. PP vs. PC
Property | ABS | Polypropylene (PP) | Polycarbonate (PC) |
Cost (USD/kg) | 2.1–2.5 | 1.3–1.8 | 3.0–3.5 |
Heat Resistance | 85°C | 100°C | 135°C |
Impact Strength | High | Moderate | Very High |
Best For | Automotive interiors | Food packaging | Medical devices |
2.2 When to Choose Engineering Plastics
For high-stress applications (e.g., aerospace), consider:
- PEEK: 90–120/kg, withstands 250°C.
- Ultem (PEI): 40% lighter than steel, FDA-compliant.
Scaling High-Volume Injection Molding Processes
3.1 Multi-Cavity Mold Design
A 64-cavity mold produces 8x more parts/hour than an 8-cavity system but requires:
- Balanced runner systems: ±1% weight variation tolerance.
- Conformal cooling channels: Reduce cooling time by 30%.

3.2 Lean Manufacturing Integration
- SMED (Single-Minute Exchange of Die): Cut mold changeover to <10 minutes.
- TPM (Total Productive Maintenance): Boost OEE (Overall Equipment Effectiveness) to 85%+.
FAQs: Addressing Plastic Injection Molding Pain Points
1. How much does a plastic injection mold cost?
Molds range from 3,000(simple) to 100,000+ (multi-cavity, high-precision).
2. Can recycled plastics be used in injection molding?
Yes, but limit regrind to 30% for structural parts to maintain strength.
3. What’s the minimum order quantity (MOQ) for custom parts?
Typically, 1,000–10,000 units, depending on mold complexity.
4. How to prevent warping in thin-walled parts?
Use materials with low shrinkage (e.g., PP: 1.5–2.5%) and optimize gate design.
5. Which industries benefit most from high-volume molding?
Automotive, consumer electronics, and medical device manufacturing.
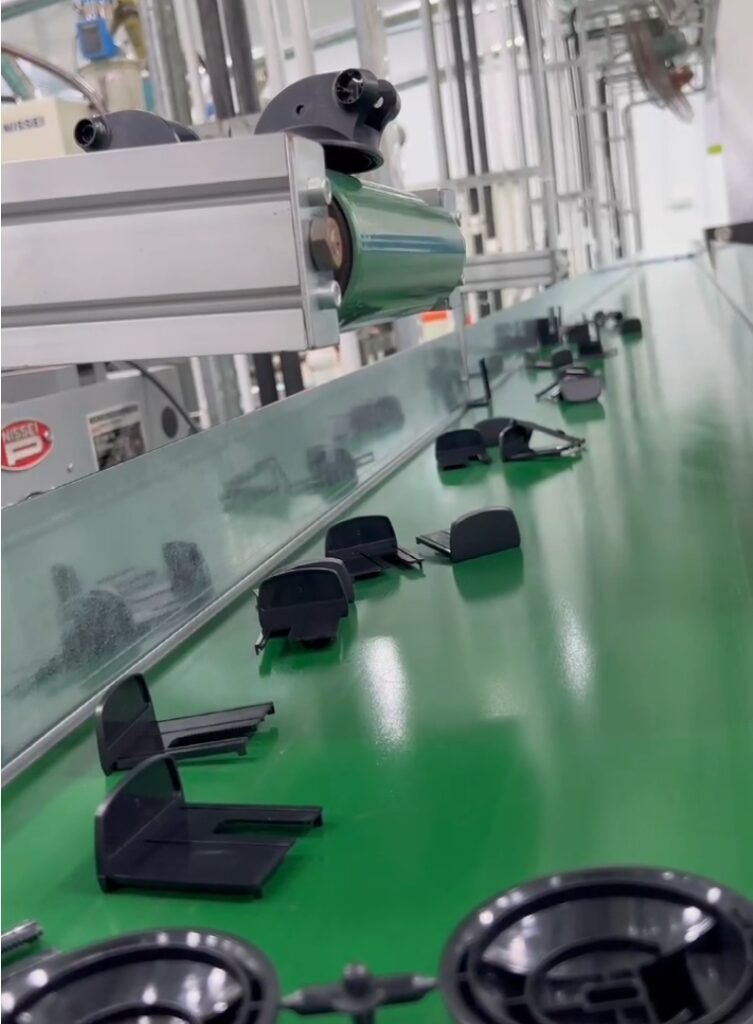
Conclusion
Optimizing plastic injection molding hinges on balancing cost, material science, and scalable processes. By leveraging advanced cooling technologies, data-driven material selection, and lean methodologies, manufacturers can achieve 20–30% cost savings while meeting stringent quality standards.
Ready to Optimize Your Molding Process?
Contact us for a free audit of your production line and material strategy.