Injection molding is a widely used manufacturing process for producing plastic parts with intricate shapes and fine details. While the primary focus in injection molding is on creating the part’s overall structure, the surface quality of these parts is equally important. Surface treatment of injection molded parts is crucial in enhancing their appearance, functionality, and durability, meeting aesthetic and performance requirements in various industries.
Why Do Surface Treatments?
Surface treatments are essential for several reasons:
Aesthetic Enhancement: improve the visual appeal of parts by providing a smooth, glossy, or textured finish.
Functional Improvement: enhance properties like wear resistance, corrosion resistance, electrical conductivity, or friction reduction.
Adhesion Promotion: prepare surfaces for painting, coating, or bonding by improving adhesion properties.
Cleanliness and Hygiene: meet sanitary requirements, especially in the medical, food, and beverage industries.
Identification and Branding: allow for markings, logos, or other features integral to branding and product identification.
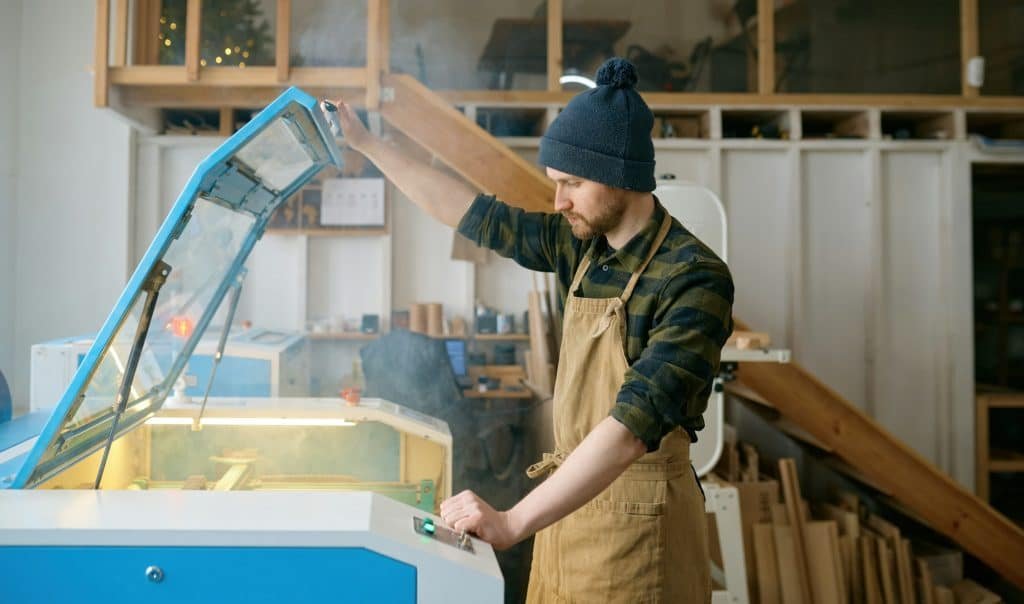
What are the Key Factors in Determining Surface Treatment?
Several factors influence the choice of surface treatment for injection molded parts:
Material Type: Different plastics respond differently to various treatments; hence, the material composition dictates suitable treatment methods.
End-Use Requirements: The part’s intended application, including environmental exposure and mechanical stress, determines its necessary surface properties.
Aesthetic Considerations: Desired visual characteristics such as color, texture, and gloss level influence the selection of surface treatment processes.
Cost and Production Efficiency: The cost-effectiveness and impact on production time are crucial in deciding which treatment to apply.
Regulatory Compliance: Adherence to industry standards and regulations, particularly in sectors like healthcare and automotive, guides the choice of surface treatments.

Surface Treatment Process Classification
Surface treatment processes for injection molded parts can be broadly classified into several categories:
Mechanical Treatments
- Polishing: Enhances surface smoothness and gloss.
- Blasting: Creates texture or roughness using abrasive materials.
Chemical Treatments
- Etching: Alters the surface by using chemicals to create textures or patterns.
- Priming: Prepares surfaces for subsequent coating or painting.
Thermal Treatments
- Flame Treatment: A controlled flame modifies surface properties, enhancing adhesion.
- Plasma Treatment: Employs plasma to clean and activate surfaces.
Coating Processes
- Painting: Applies colored coatings for aesthetic and protective purposes.
- Electroplating: Deposits a thin layer of metal to improve conductivity or corrosion resistance.
- Powder Coating: Provides a durable and decorative finish.
Specialized Treatments
- UV Coating: Uses ultraviolet light to cure coatings, providing a hard and glossy finish.
- Vacuum Metallization: Deposits a thin metallic layer for decorative or functional purposes.
In conclusion, surface treatment is vital to the injection molding process, significantly impacting the final product’s quality, performance, and marketability. Understanding the various factors and treatment options allows manufacturers to tailor the surfaces of their products to meet specific industry needs and customer expectations.