The Benefits of Plastic Injection Molding for Pet Product Manufacturing

The pet industry has seen a significant boom in recent years, with pet owners increasingly focusing on providing high-quality, functional, and aesthetically pleasing products for their furry companions. From durable pet toys to stylish pet accessories, plastic injection molding has emerged as a preferred manufacturing technique for creating a wide range of pet products. In this article, we explore the advantages of plastic injection molding for the pet product industry and how it helps meet the demands for high-quality, cost-effective, and customizable solutions.
What is Plastic Injection Molding?
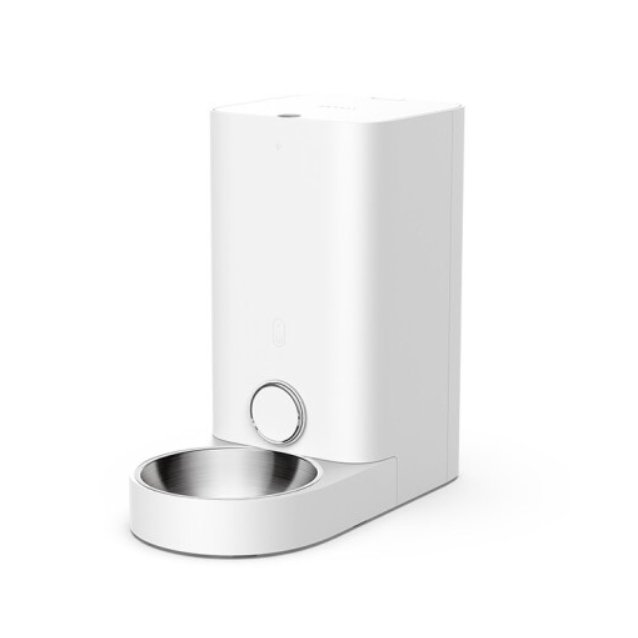
Plastic injection molding is a manufacturing process that involves injecting molten plastic material into a precisely designed mold cavity. The plastic then cools and hardens to form the desired shape, which can be ejected from the mold. This process is highly efficient and versatile, making it ideal for producing various products, including pet products.
Injection molding can accommodate various types of plastic materials, allowing manufacturers to select the best option based on the pet product’s specific requirements, such as durability, flexibility, or texture. This versatility, combined with its speed and precision, has made it the go-to choice for manufacturers of pet products across the globe.
Key Advantages of Plastic Injection Molding for Pet Products
1. Precision and Consistency
One of the key advantages of plastic injection molding is its ability to produce products with high precision and consistency. Once the mold is created, the process ensures that each pet product is manufactured to exact specifications, reducing the risk of defects and ensuring uniformity in large production runs. This is especially important in the pet industry, where products such as pet toys, accessories, and grooming tools need to be safe, functional, and reliable.
For instance, a pet toy that is made with tight tolerances can ensure that small parts do not break off and become choking hazards for pets. Consistent quality across all products is essential for maintaining customer satisfaction and trust.
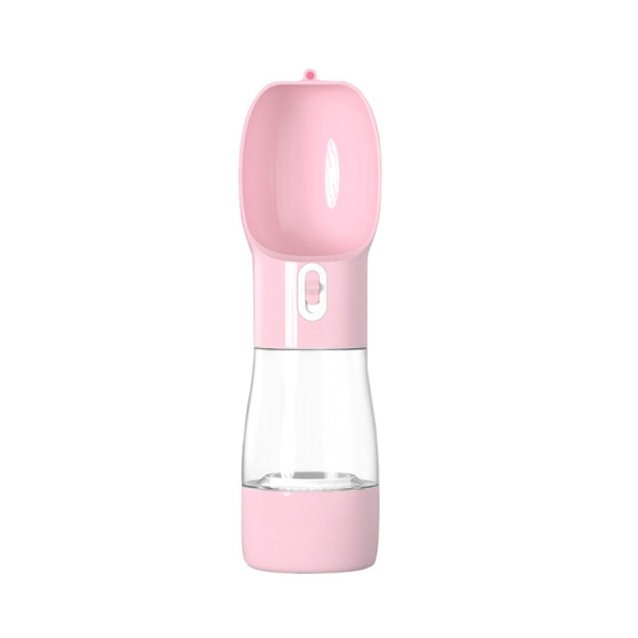
2. Customization and Design Flexibility
Plastic injection molding allows for a high degree of customization in design, making it possible to create pet products with unique shapes, colors, and textures. Whether you’re manufacturing ergonomic pet bowls, personalized dog collars, or interactive toys, injection molding offers the flexibility to design products that cater to both functionality and aesthetics.
Additionally, manufacturers can use multiple plastic materials or even incorporate inserts, such as logos, textures, or even electronic components, to enhance the product’s appeal and performance. Customization options are particularly valuable in the pet product industry, where unique, tailored items are in demand.
3. High-Volume Production with Cost Efficiency
In the pet product market, the demand for mass production of items such as pet beds, feeders, and toys is constantly growing. Plastic injection molding is particularly suited for high-volume production due to its speed and efficiency. Once the mold is designed and tested, the process can quickly produce thousands or even millions of identical products, significantly reducing the cost per unit.
The efficiency of plastic injection molding also helps minimize material waste, contributing to lower production costs and making it an economically viable option for pet product manufacturers. This cost-effectiveness is crucial for businesses looking to stay competitive in a fast-growing market.
4. Durability and Strength
The pet industry often requires products that are durable enough to withstand the wear and tear of daily use. Whether it’s a chew toy, a feeding bowl, or a pet carrier, the materials used in manufacturing must be able to endure repeated stress, exposure to moisture, and general handling. Plastic injection molding offers the ability to create strong and durable pet products that can withstand the rigorous demands of everyday pet life.
By selecting the right materials, manufacturers can ensure that their products are impact-resistant, easy to clean, and capable of handling various environmental conditions. Some plastic materials, such as polycarbonate or ABS, are particularly known for their strength and durability, making them ideal choices for pet products.
5. Fast Turnaround Times
The speed of plastic injection molding is another significant advantage, especially when time-to-market is critical. The ability to produce large quantities of pet products in a short amount of time helps manufacturers meet the ever-increasing demands of the pet industry. Whether launching a new pet accessory line or replenishing inventory, injection molding allows for quick production cycles, reducing the overall lead time.
In addition, rapid prototyping is possible with injection molding. Manufacturers can quickly test product designs and make adjustments, allowing for faster iteration and development of new pet products.
6. Safe and Non-Toxic Materials
For pet products, safety is of paramount importance. Pet owners are highly concerned about the materials used in the products they buy for their pets, especially when it comes to toys, feeding accessories, and grooming tools. Plastic injection molding offers the flexibility to work with a variety of non-toxic, food-safe, and environmentally friendly plastics.
By selecting BPA-free, FDA-approved, or recyclable materials, manufacturers can ensure that their pet products are safe for pets and meet industry standards for health and safety. This consideration not only enhances the reputation of manufacturers but also provides peace of mind to pet owners.
7. Environmental Benefits
Sustainability is becoming an increasingly important consideration in manufacturing, and the pet product industry is no exception. Plastic injection molding can be an environmentally friendly manufacturing process in several ways. The use of recycled plastics, along with the process’s low waste production, helps reduce the overall environmental impact.
Additionally, plastic injection molding allows for precise control over material usage, ensuring that excess plastic is minimized, which is essential for manufacturers aiming to meet eco-conscious consumer demands.
Applications of Plastic Injection Molding in Pet Products
Plastic injection molding is used to create a wide variety of pet products, ranging from practical items to fun accessories. Some common applications include:
- Pet Toys: Durable, safe, and interactive toys for pets, including chew toys and fetch items.
- Pet Accessories: Customizable pet collars, leashes, harnesses, and tags.
- Pet Feeding Products: Bowls, automatic feeders, and water dispensers.
- Pet Grooming Tools: Brushes, combs, and nail clippers.
- Pet Carriers: Lightweight, durable carriers for pets.
- Pet Furniture: Beds, cushions, and furniture covers designed for pets.
As the pet product market continues to expand, the role of plastic injection molding in the manufacturing process will only grow, offering businesses the flexibility, cost-effectiveness, and speed they need to meet consumer demands.
About BFY Mold
At BFY Mold, we specialize in high-quality plastic injection molding and mold manufacturing for a wide range of industries, including the pet product sector. Our services include mass production, on-demand production, CNC machining, and mirror spark, all of which are carried out at our fully equipped factory. We are dedicated to providing customized solutions that meet our clients’ specific needs and ensure high-quality production standards.
If you’re looking for a reliable partner to manufacture your pet products with precision and efficiency, BFY Mold is your go-to solution. With our advanced technology and expertise, we can bring your pet product ideas to life quickly and affordably.