Introduction to Prototyping in Product Development
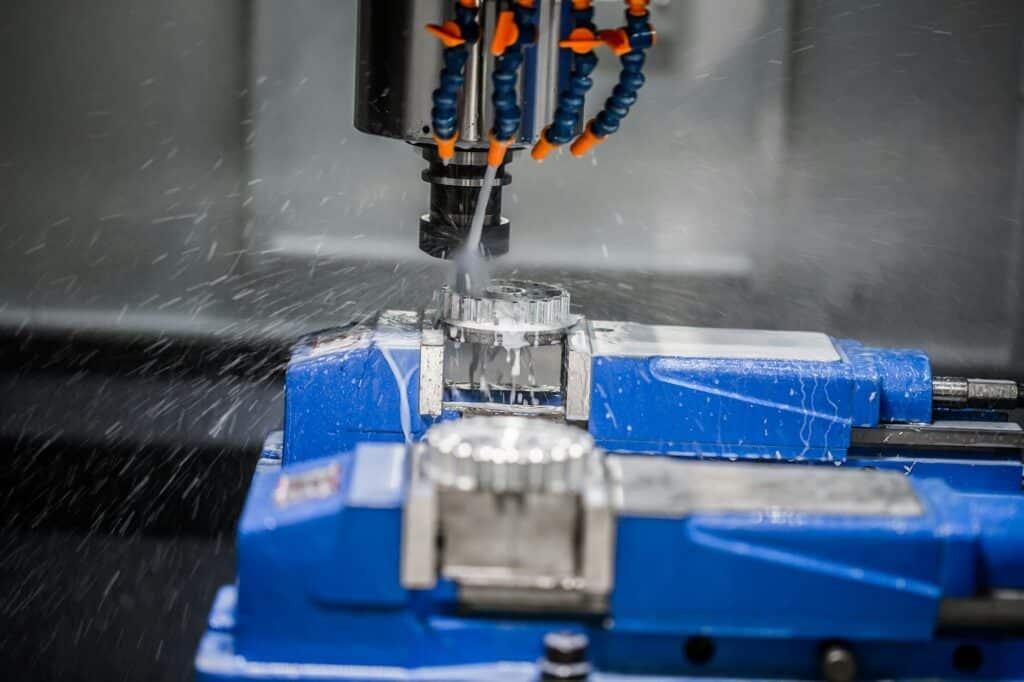
Prototyping with CNC machining and injection molding offers powerful solutions for modern product development, enabling designers and engineers to bring their concepts to life efficiently. By leveraging the precision of CNC machining alongside the speed and scalability of injection molding, manufacturers can create high-quality prototypes that accurately reflect the final product. This synergy not only accelerates the design process but also allows for rapid iterations and testing.
Prototyping stands as a cornerstone in the product development lifecycle, serving as an essential phase where ideas transform into tangible models. This intermediary step allows designers and engineers to visualize, test, and refine their concepts before committing to full-scale production. By creating prototypes, teams can identify design flaws early in the development process, ensuring that the final product meets the intended specifications and functionality.
The importance of prototyping cannot be overstated. It provides a practical framework for evaluating the usability and performance of a product. Through iterative testing and feedback, prototypes help in uncovering potential issues that might not be apparent in the initial design stages. This proactive approach minimizes costly revisions and redesigns later in the production cycle.
Moreover, prototyping fosters innovation by encouraging experimentation. Engineers and designers can explore different materials, manufacturing techniques, and design configurations to determine the most effective solutions. This hands-on engagement with the prototype offers invaluable insights that can lead to significant improvements in product functionality and user experience.
In addition to technical benefits, prototyping also plays a critical role in stakeholder communication. Physical models or even virtual simulations provide a concrete representation of the product, facilitating clearer discussions and more informed decision-making among team members, investors, and clients. This shared understanding helps align expectations and ensures that all parties are on the same page regarding the product’s development trajectory.
Ultimately, prototyping bridges the gap between conceptual design and market-ready products. By meticulously testing and refining prototypes, companies can enhance the quality and reliability of their products, thereby increasing their competitive edge in the market. This foundational phase not only mitigates risks but also paves the way for successful product launches, aligning with consumer needs and industry standards.
What is CNC Machining?
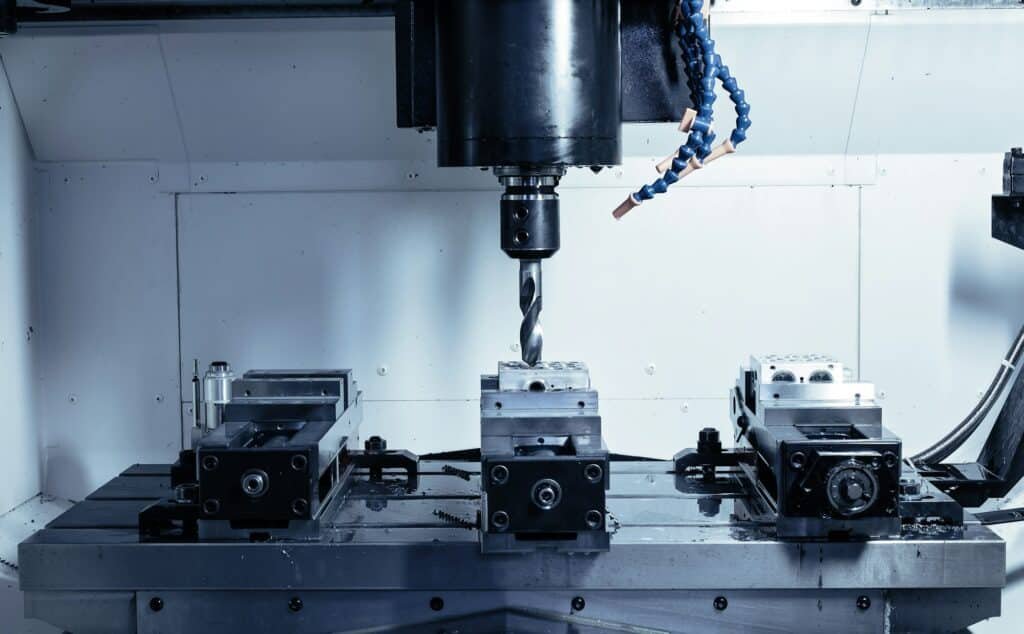
CNC (Computer Numerical Control) machining is a manufacturing process in which pre-programmed computer software dictates the movement of factory tools and machinery. This technology can be used to control a range of complex machinery, from grinders and lathes to mills and routers. With CNC machining, three-dimensional cutting tasks can be accomplished in a single set of prompts.
One of the primary advantages of CNC machining is its ability to produce highly precise and complex parts from a variety of materials, including metals, plastics, wood, and composites. The process begins with the creation of a digital design for the desired part. This design is then converted into a computer program that controls the movements of the machine, allowing it to cut, drill, and shape the material with exceptional accuracy.
CNC milling machines use rotary tools to cut away material, while CNC lathes rotate the workpiece against a cutting tool to shape it. CNC routers, on the other hand, are used for cutting and engraving materials like wood, plastic, and softer metals. Each type of machine has its specific capabilities and is chosen based on the requirements of the project.
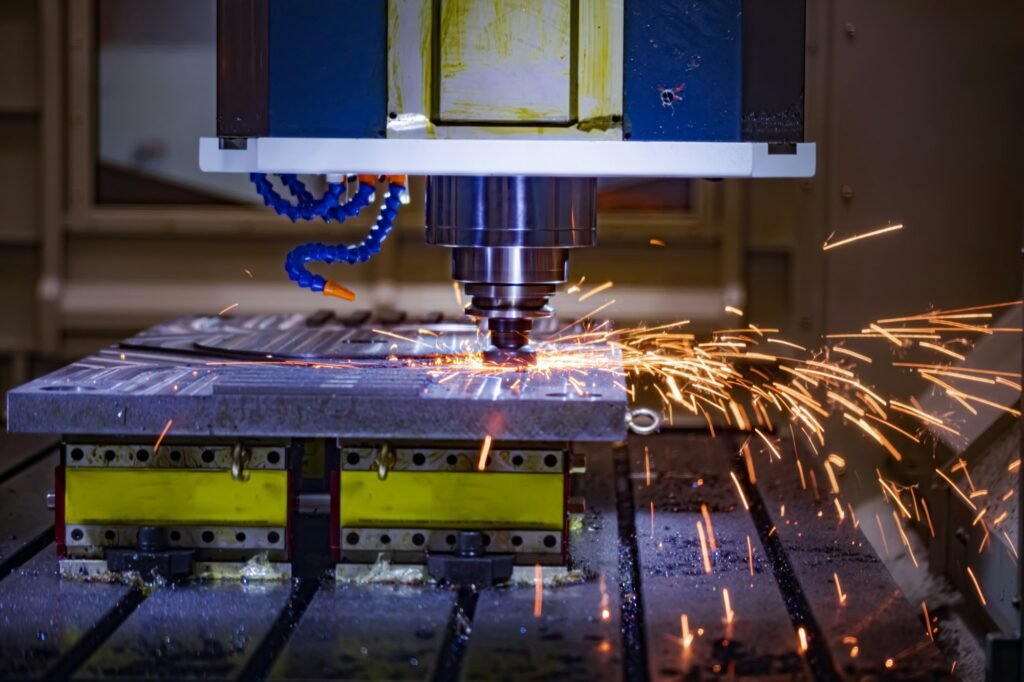
The benefits of CNC machining are manifold. Its unparalleled precision ensures that parts are produced to exact specifications, reducing errors and waste. The process is also highly efficient; once the design is programmed, the machine can operate continuously with minimal human intervention, speeding up production times. Furthermore, the versatility of CNC machines allows for the creation of complex geometries that would be difficult or impossible to achieve with manual machining techniques.
In the realm of product development, CNC machining stands out for its ability to rapidly produce prototypes and final parts that meet stringent quality standards. This makes it an indispensable tool in industries ranging from aerospace and automotive to consumer electronics and medical devices.
Understanding Injection Molding
Injection molding is a pivotal process in both prototyping and mass production, renowned for its efficiency and precision. At its core, injection molding involves the creation of molds, usually made from steel or aluminum, which are designed to form the desired shape of the product. Once the mold is prepared, materials, typically various types of plastics, are heated until they reach a molten state. This molten plastic is then injected into the mold cavity under high pressure. As the material cools and solidifies, it takes on the shape of the mold, resulting in the formation of the final product.
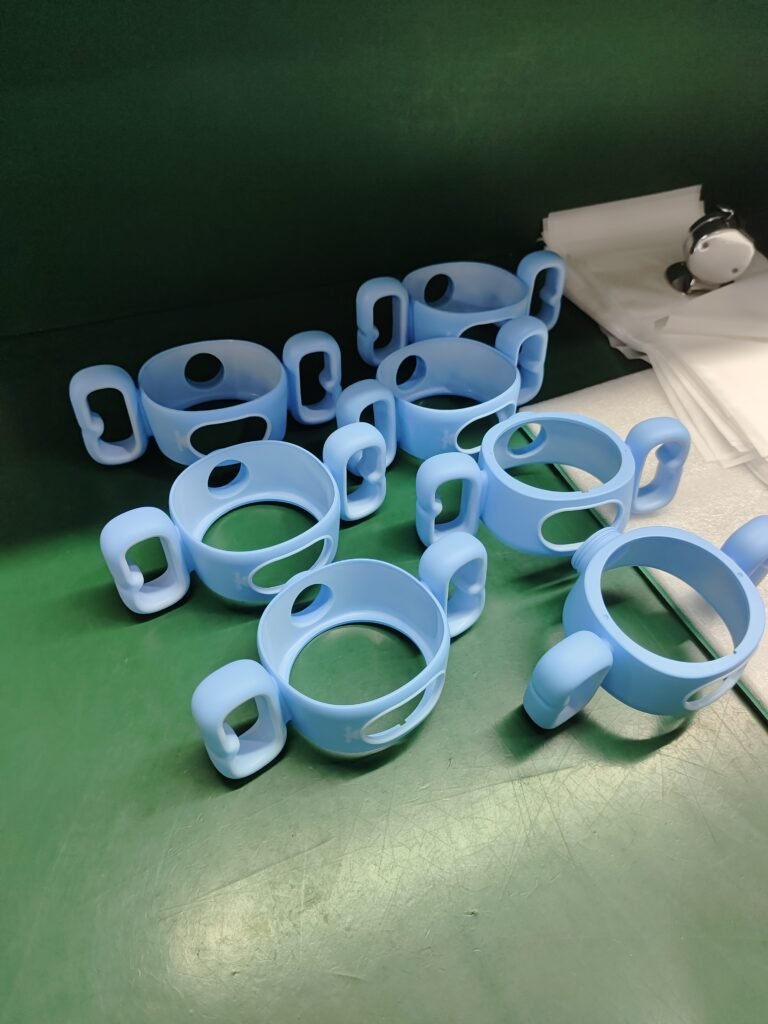
One of the most significant advantages of injection molding is its capacity for high production rates. This process can produce thousands of identical parts in a relatively short period, making it ideal for large-scale manufacturing. Additionally, injection molding offers remarkable repeatability. Once the mold is created, it can be used repeatedly to produce virtually identical parts, ensuring consistency and quality in mass production.
Another notable benefit of injection molding is its ability to produce complex shapes with tight tolerances. The precision of the molds allows for intricate designs and detailed features that might be challenging to achieve with other manufacturing methods. This capability is particularly advantageous in industries such as automotive, aerospace, and consumer electronics, where precision and complexity are paramount.
Moreover, injection molding is highly versatile in terms of material usage. While plastics are the most common materials, injection molding can also be used with metals, ceramics, and other composites, depending on the application. This versatility extends to the range of finishes and textures that can be achieved, adding further value to the process.
In essence, injection molding is an indispensable technique in modern manufacturing, offering efficiency, precision, and versatility. Its ability to produce large volumes of high-quality parts makes it a cornerstone in the field of product development.
The Role of CNC Machining in Prototyping
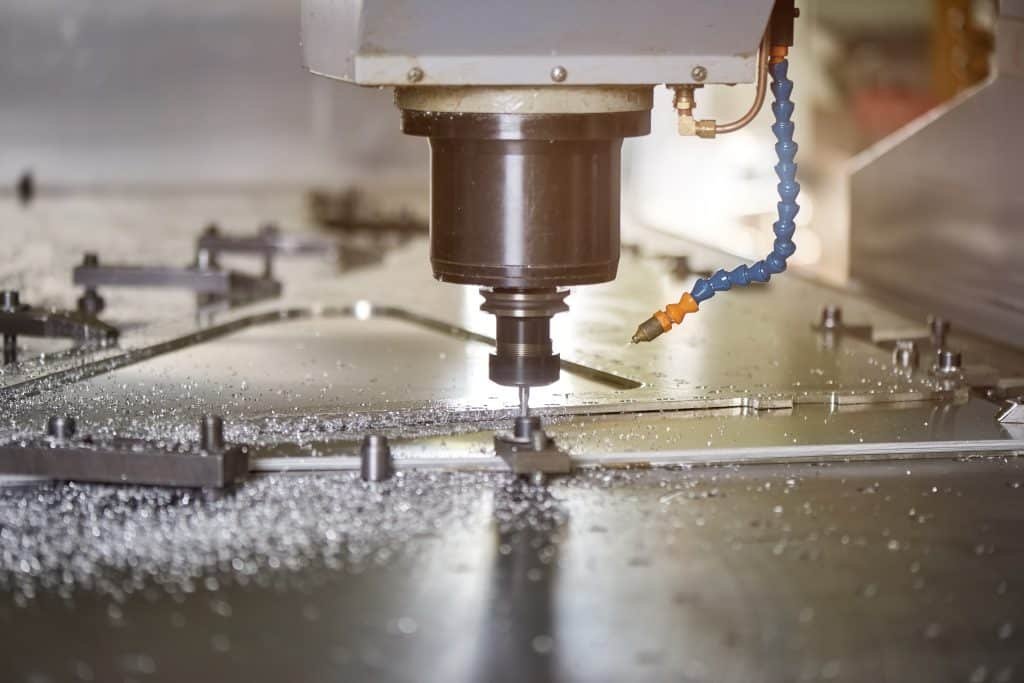
CNC machining has become an indispensable tool in the prototyping phase of product development, thanks to its precision and versatility. By leveraging computer numerical control (CNC) technology, manufacturers can quickly transform digital designs into accurate, physical prototypes. This capability significantly accelerates the iterative process, allowing designers to test and refine their concepts with unparalleled speed and precision.
One of the primary advantages of CNC machining in prototyping is its ability to produce highly detailed and accurate models. The precision of CNC machines ensures that the prototypes closely match the digital designs, minimizing discrepancies and reducing the need for manual adjustments. This high level of accuracy is crucial for identifying potential design flaws early in the development process, which in turn helps in refining the final product.
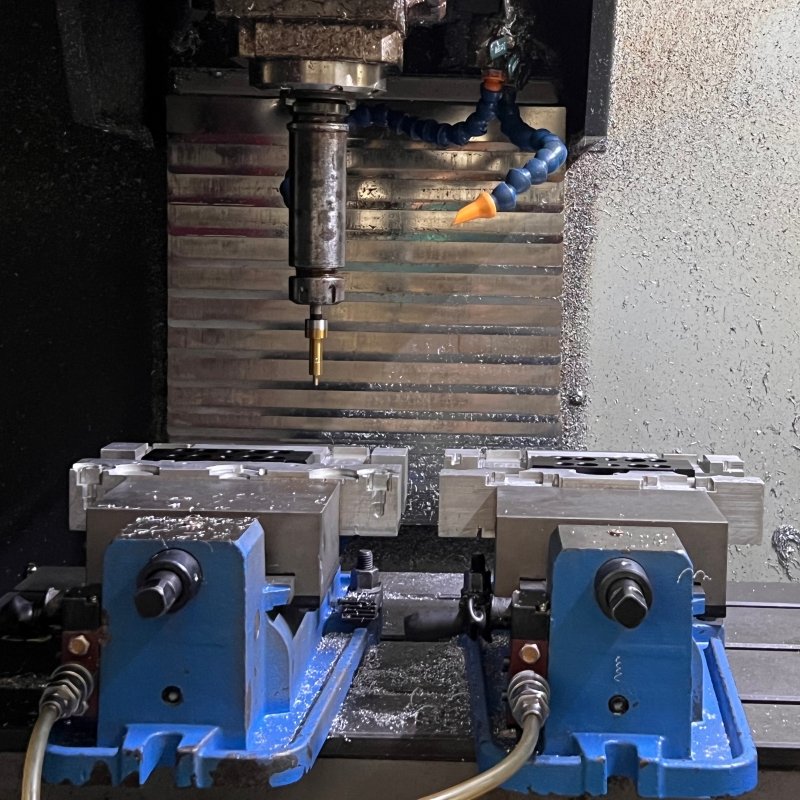
Moreover, CNC machining supports a broad spectrum of materials, ranging from metals and plastics to wood and composites. This versatility is essential for creating functional and durable prototypes that can withstand rigorous testing. For instance, metal prototypes can be subjected to stress tests to evaluate their structural integrity, while plastic prototypes can be used to assess the feasibility of complex geometries. The ability to work with diverse materials also enables designers to experiment with different options and select the most suitable one for the final product.
The rapid production capabilities of CNC machining are another significant benefit. Traditional methods of prototyping might take weeks or even months, whereas CNC machines can produce prototypes in a matter of hours or days. This swift turnaround time enables faster iteration cycles, facilitating quicker decision-making and reducing the overall time to market.
In conclusion, CNC machining plays a vital role in the prototyping phase of product development. Its precision, material versatility, and rapid production capabilities make it an invaluable asset for designers and engineers aiming to create functional and durable prototypes efficiently. As technology continues to advance, the role of CNC machining in prototyping is expected to become even more prominent, driving innovation and excellence in product development.
The Role of Injection Molding in Prototyping
Injection molding plays a crucial role in the prototyping phase, particularly for products destined for mass production using this method. By creating injection-molded prototypes, manufacturers gain significant insights that can streamline the transition to large-scale production. One of the primary advantages is the ability to test the production process early on. This involves assessing the efficiency of mold designs, identifying potential issues, and making necessary adjustments before full-scale manufacturing begins. Such proactive measures can mitigate costly errors and ensure a smoother production workflow.

Another critical benefit of using injection molding for prototypes is the evaluation of material performance. By producing prototypes with the same materials intended for the final product, manufacturers can accurately gauge how these materials behave under real-world conditions. This includes assessing durability, flexibility, and overall performance, which can inform decisions about material selection and potential modifications. This step is essential in ensuring that the final product meets the desired quality standards and performs reliably in its intended application.
Moreover, creating injection-molded prototypes allows for the refinement of mold designs. Prototyping enables engineers and designers to experiment with different mold configurations, identify design flaws, and make iterative improvements. This process ensures that the final molds used in mass production are optimized for efficiency and effectiveness. By refining mold designs during the prototyping phase, manufacturers can achieve higher precision in the final product, reducing waste and enhancing overall production quality.
In summary, the integration of injection molding in the prototyping process offers numerous advantages, including the ability to test production processes, evaluate material performance, and refine mold designs. These benefits not only enhance the overall quality of the final product but also contribute to a more cost-effective and efficient production cycle.
Comparing CNC Machining and Injection Molding for Prototyping
CNC machining and injection molding are two prominent methods employed in the prototyping phase of product development. Each technique offers distinct advantages and limitations, making them suitable for different scenarios based on specific project requirements.
CNC machining is renowned for its precision and versatility. This subtractive manufacturing process involves removing material from a solid block using computer-controlled cutting tools. One of the primary strengths of CNC machining is its ability to work with a wide range of materials, including metals, plastics, and composites. It excels in producing highly accurate and complex geometries, making it ideal for prototypes that require detailed features and tight tolerances. However, CNC machining can be more costly and time-consuming, particularly for low-volume production, due to the extensive setup and material waste involved.
On the other hand, injection molding is a process where molten material is injected into a mold cavity to form a part. This method is highly efficient for producing large quantities of parts with consistent quality. Injection molding is particularly advantageous when working with thermoplastics and elastomers, offering a broad selection of material options. Additionally, it is well-suited for creating complex shapes and intricate details. However, the initial cost of creating molds can be high, making it less economical for low-volume prototyping. The lead time for mold creation can also be a limiting factor when rapid prototyping is essential.
When deciding between CNC machining and injection molding, several factors should be considered. For prototypes that demand high precision, diverse material compatibility, and flexibility in design modifications, CNC machining is often the preferred choice. Conversely, injection molding is more suitable for projects requiring mass production, uniformity, and cost-efficiency for high volumes. The complexity of the design, material properties, and production timeline are critical determinants in selecting the appropriate prototyping method.
In essence, both CNC machining and injection molding have unique strengths that can be leveraged based on the specific needs of a project. Understanding their respective advantages and limitations is crucial in making an informed decision for effective prototyping.
Successful Prototyping Projects
Prototyping is a pivotal phase in product development, and the integration of CNC machining and injection molding has proven to be a game changer across various industries. These techniques not only streamline the prototyping process but also enhance precision, reduce costs, and accelerate time-to-market. Here, we delve into a few exemplary case studies that highlight the transformative power of these methodologies.
In the automotive sector, a leading car manufacturer faced significant challenges in developing a new engine component. Traditional prototyping methods were time-consuming and costly, impeding the project’s progress. By leveraging CNC machining, the team was able to create a highly accurate prototype swiftly. This precision machining allowed for rigorous testing and refinement, ultimately leading to a superior final product. Injection molding was later utilized to produce the component at scale, ensuring consistency and durability.
The medical device industry also illustrates the efficacy of CNC machining and injection molding in prototyping. A company aiming to develop an innovative surgical instrument encountered difficulties with existing prototyping techniques, which lacked the necessary precision and material properties. By adopting CNC machining, the team produced a detailed prototype that met stringent medical standards. The subsequent use of injection molding enabled the production of complex parts with high repeatability, crucial for medical applications.
Another noteworthy example comes from the consumer electronics sector. A startup developing a new wearable device needed a prototype that could undergo extensive user testing. Traditional methods fell short of achieving the required detail and functionality. CNC machining provided the solution, producing a prototype that closely mirrored the final product. Injection molding then facilitated the creation of multiple iterations, allowing for thorough testing and feedback incorporation. This iterative process was instrumental in refining the design and ensuring a successful product launch.
These case studies underscore the significant advantages of CNC machining and injection molding in prototyping. By overcoming traditional challenges and enhancing the development process, these techniques have enabled companies to bring innovative products to market efficiently and effectively.
Conclusion
In conclusion, the significance of prototyping in product development cannot be overstated. Prototyping serves as a critical phase that allows businesses to visualize, test, and refine their product concepts before moving into full-scale production. Throughout this blog post, we have explored the indispensable roles of CNC machining and injection molding in the prototyping process. CNC machining offers precision and flexibility, making it ideal for creating detailed and intricate prototypes. On the other hand, injection molding excels in producing high-fidelity prototypes that closely mimic the final product, ensuring reliable performance and functionality.
BFY Mold Manufacturing
Our company is dedicated to providing top-tier services in the realm of product development. We specialize in injection molding, mold manufacturing, mass production, and on-demand production. Additionally, we offer advanced CNC machining services and mirror spark technology, catering to a diverse range of prototyping and manufacturing needs. With our factory, we maintain stringent quality control and efficient production processes, ensuring that we deliver products that meet the highest standards of excellence.
Partnering with us means leveraging state-of-the-art technology and expert craftsmanship to bring your product ideas to life. Our commitment to quality and innovation ensures that every prototype we create not only meets but exceeds expectations. Whether you are in the initial stages of product development or ready to scale up to mass production, our comprehensive suite of services is designed to support your journey from concept to completion.