Introduction to Metal Machining
Metal machining is a manufacturing process that removes material from a workpiece to shape it into a desired form. Utilizing a variety of tools and techniques, metal machining is critical for industries ranging from aerospace to automotive, delivering precision components with high accuracy.
Modern machining processes combine traditional craftsmanship with advanced technologies like CNC (Computer Numerical Control) to meet rigorous quality standards.
In this article, we explore the different types of metal machining processes, their advantages, and applications, providing valuable insights into the world of precision manufacturing.
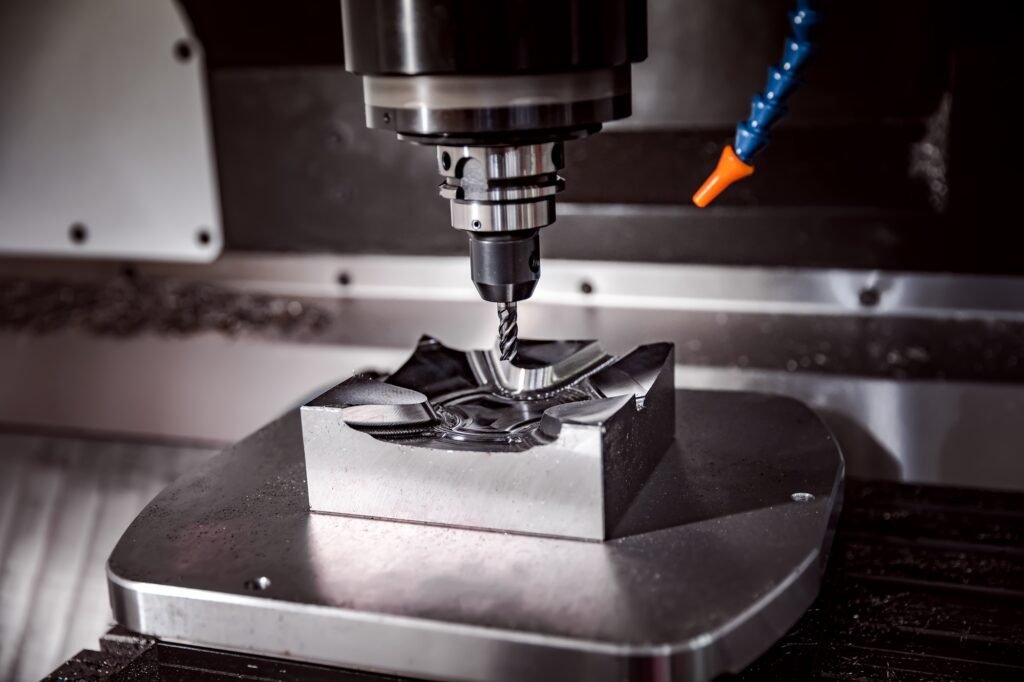
What Are Metal Machining Processes?
Metal machining encompasses several techniques to cut, shape, and refine metal parts. These processes are broadly categorized into traditional machining (e.g., turning and drilling) and non-traditional machining (e.g., laser cutting and electrical discharge machining). Each technique serves specific purposes and industries, ensuring versatility and adaptability in manufacturing.
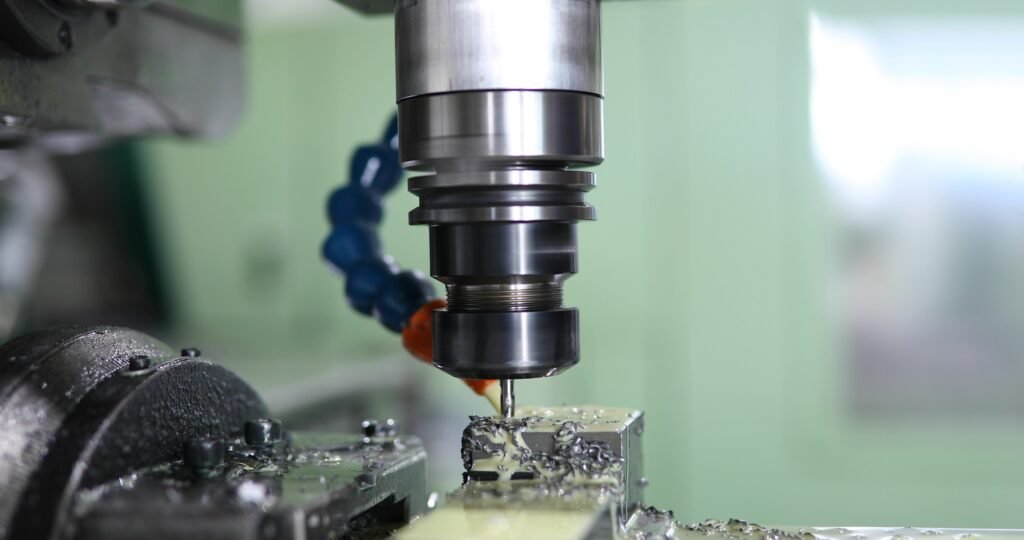
Why Is Metal Machining Important?
- Precision: Allows for tight tolerances and intricate designs.
- Versatility: Works with various metals, including aluminum, steel, titanium, and alloys.
- Customization: Offers tailored solutions for unique product requirements.
Key Types of Metal Machining Processes
1. Turning
Turning involves rotating the workpiece on a lathe while a cutting tool removes material to create cylindrical shapes. This process is ideal for producing shafts, bearings, and other rounded components.
- Advantages: High precision and smooth surface finishes.
- Applications: Automotive shafts, aerospace connectors, and machine parts.
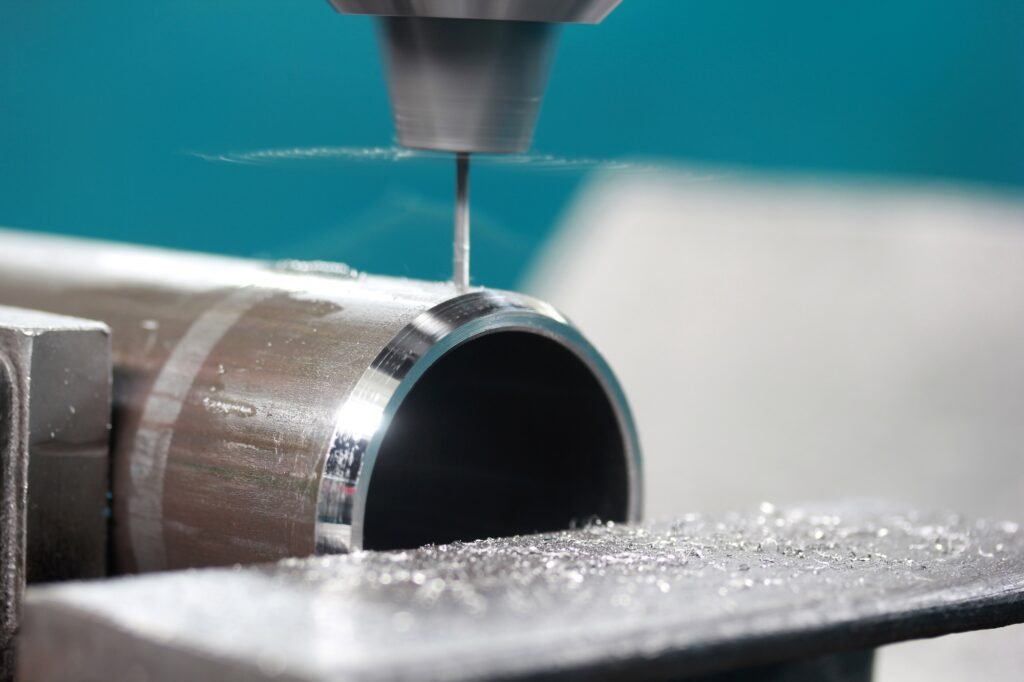
2. Milling
Milling uses rotary cutting tools to remove material, enabling the creation of flat surfaces, slots, and complex geometries.
- Advantages: Suitable for both 2D and 3D parts.
- Applications: Mold making, custom gears, and metal brackets.
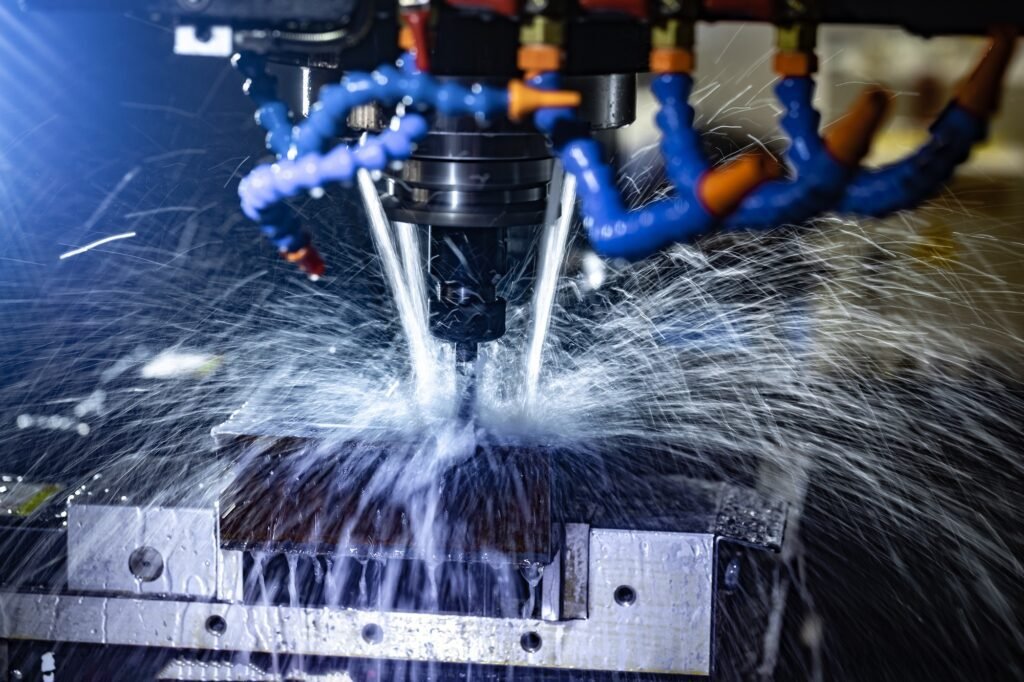
3. Drilling
Drilling creates precise holes in a workpiece using a rotating drill bit. It is one of the simplest and most commonly used machining techniques.
- Advantages: Efficient for creating holes of various sizes and depths.
- Applications: Fasteners, mechanical components, and tool fabrication.
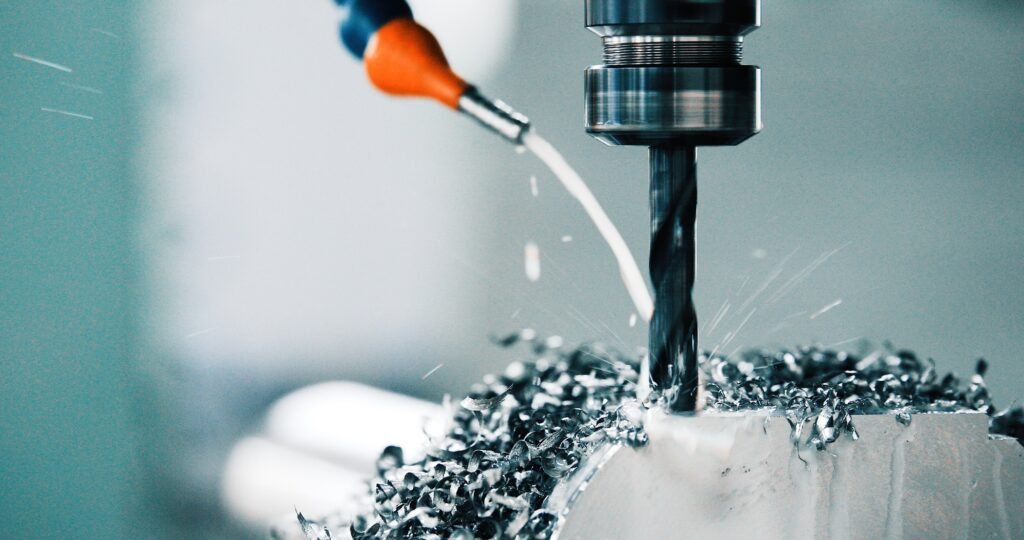
4. Grinding
Grinding utilizes abrasive wheels to achieve smooth and highly accurate surface finishes. This process is essential for polishing and refining parts.
- Advantages: High surface quality and dimensional accuracy.
- Applications: Aerospace parts, medical devices, and precision tools.

5. CNC Machining
CNC machining employs computer-guided tools for automated, high-precision manufacturing. It integrates processes like milling, turning, and drilling into a single workflow.
- Advantages: Scalability, repeatability, and complex geometry capabilities.
- Applications: Prototyping, custom components, and mass production.
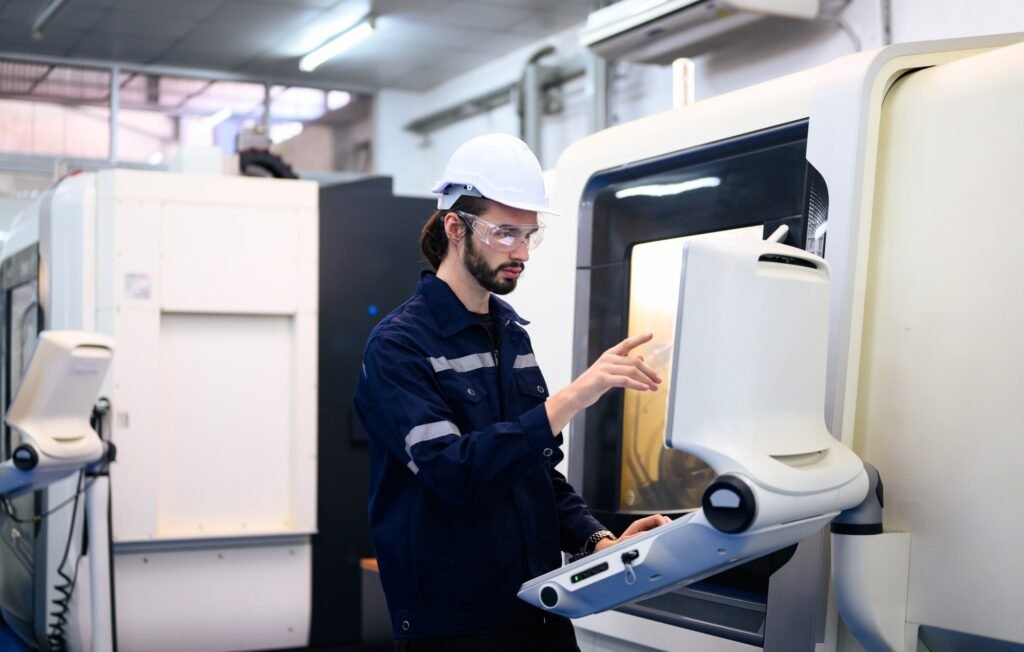
Advanced Metal Machining Techniques
1. Electrical Discharge Machining (EDM)
EDM uses electrical sparks to erode metal, making it suitable for intricate designs and hard metals.
- Advantages: No contact with the workpiece, ideal for fragile components.
- Applications: Die manufacturing, aerospace components, and micro parts.
2. Laser Cutting
Laser cutting employs focused light beams to cut and engrave metal precisely.
- Advantages: Clean edges and minimal waste.
- Applications: Custom signage, electronics enclosures, and decorative pieces.
3. Waterjet Cutting
This process uses high-pressure water mixed with abrasives to cut metal without generating heat.
- Advantages: Maintains material integrity without thermal distortion.
- Applications: Aerospace panels, automotive parts, and architectural designs.
Factors to Consider When Choosing a Metal Machining Process
- Material Type: Different metals require specific tools and techniques.
- Part Design: Complex geometries may need advanced processes like CNC machining.
- Volume: High-volume production favors automated methods like CNC or laser cutting.
- Surface Finish Requirements: Grinding or polishing may be necessary for aesthetic or functional purposes.
Benefits of Metal Machining for Your Business
- Improved Efficiency: Faster production times with minimal errors.
- Cost-Effectiveness: Advanced technologies reduce material waste and labor costs.
- Customizability: Tailored solutions for unique industry needs.
Why Choose BFY Mold for Your Metal Machining Needs?
At BFY Mold, we are committed to delivering precision and quality through our comprehensive manufacturing services. Our offerings include:
- Injection Molding & Mold Manufacturing: High-quality molds for diverse applications.
- Mass Production & On-Demand Production: Scalable solutions to meet your needs.
- CNC Machining: Cutting-edge technology for precise and efficient manufacturing.
- Mirror Spark Processing: Superior finishes for high-precision parts.
With our in-house factory and advanced capabilities, we ensure top-notch service and reliability for your projects. Partner with BFY Mold for unmatched expertise in metal machining and beyond.
Conclusion
Understanding the various types of metal machining processes is essential for optimizing manufacturing outcomes. Each process offers unique benefits to meet specific production needs, from traditional techniques like turning and milling to advanced methods such as CNC machining and laser cutting. BFY Mold is your trusted partner for precision machining, combining industry expertise with cutting-edge technology to deliver exceptional results.