Introduction
The automotive industry increasingly relies on plastics for manufacturing parts due to their lightweight, durability, and design flexibility. Not only do plastic materials improve fuel efficiency because they reduce the weight of vehicles, but they are also a cost-effective option for producing items with complex shapes.
This article delves into the various types of plastics used in automotive parts manufacturing, their properties, and applications, as well as the reason for their importance in modern vehicle design. For things like exterior components, interior finishes, and under-the-hood applications, the choice of plastic is crucial for performance and functionality.
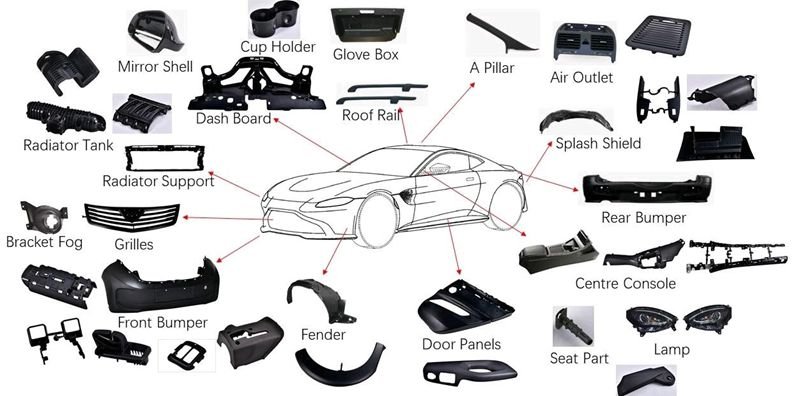
Why Use Plastics in Automotive Parts Manufacturing?
Benefits of Plastics in Automotive Applications
- Lightweight: Reduces the overall weight of vehicles, enhancing fuel efficiency.
- Durability: Resistant to corrosion, wear, and environmental factors.
- Design Flexibility: Allows for intricate designs and complex geometries.
- Cost-Effective: Enables mass production with lower material and labor costs.
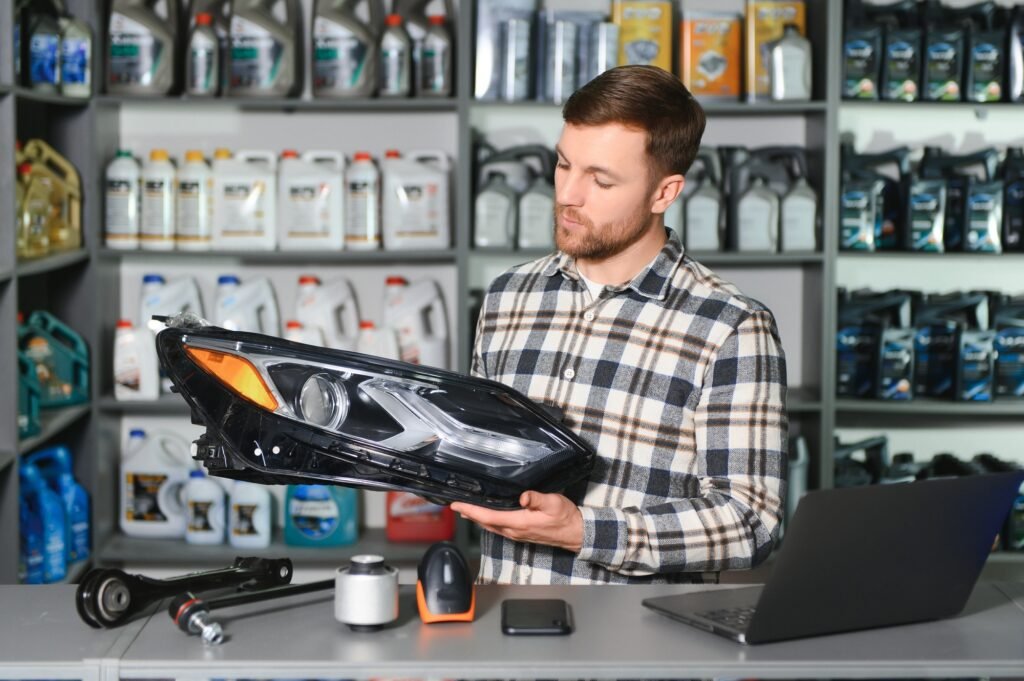
Automotive Components Commonly Made from Plastics
- Exterior parts: Bumpers, grilles, and mirrors.
- Interior parts: Dashboards, door panels, and seats.
- Engine components: Air intake manifolds, fuel systems, and battery casings.
Types of Plastics for Automotive Parts Manufacturing
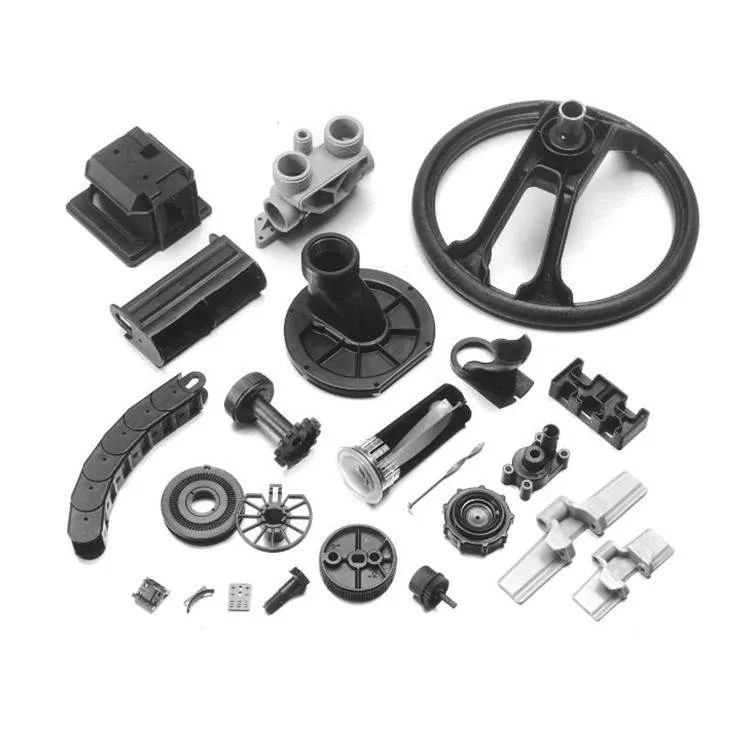
1. Polypropylene (PP)
Properties: Lightweight, chemical and fatigue resistant, and very versatile.
- Applications: Interior trim, battery housings, and bumpers.
- Advantages: Cheap and very recyclable, sustainable.
2. Acrylonitrile Butadiene Styrene (ABS)
Properties: Very high strength, good surface finish, thermal stability.
- Applications: Dashboard, instrument panels & door panels
- Advantages: Ideal for parts where both aesthetics and durability are required.
3. Polyvinyl Chloride (PVC)
Properties: Flexible, durable, and resistant to weathering and chemicals.
- Applications: Wire insulation, seals, and weather stripping.
- Advantages: Provides excellent insulation and sealing properties.
4. Polycarbonate (PC)
Properties: High impact strength, optical clarity, and heat resistance.
- Applications: Headlamp lenses, sunroof panels, and safety glasses.
- Advantages: Perfect for applications requiring transparency and toughness.
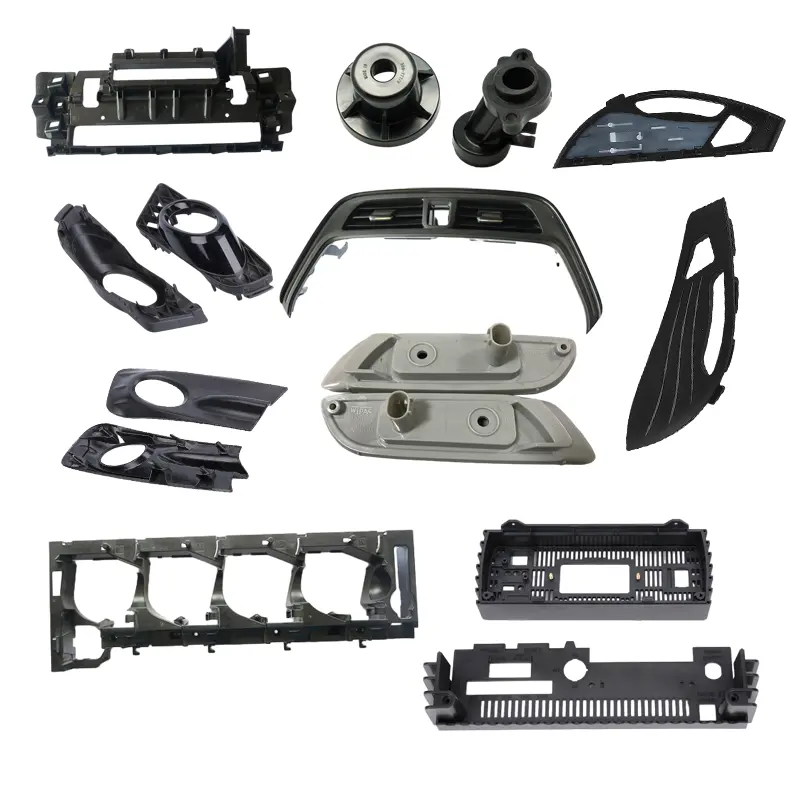
5. Polyethylene Terephthalate (PET)
Properties: Strong, lightweight, and moisture-resistant.
- Applications: Seat belts, fuel systems, and under-the-hood components.
- Advantages: Excellent for parts exposed to harsh environments.
6. Nylon (Polyamide)
Properties: High tensile strength, abrasion resistance, and heat tolerance.
- Applications: Gears, bushings, and engine covers.
- Advantages: Reduces wear and tear, extending the life of moving parts.
7. Thermoplastic Polyurethane (TPU)
Properties: Flexible, durable, and resistant to oil and grease.
- Applications: Hoses, gaskets, and suspension bushings.
- Advantages: Excellent for dynamic applications requiring flexibility.
8. Polyoxymethylene (POM)
Properties: High stiffness, low friction, and excellent dimensional stability.
- Applications: Lock systems, fasteners, and precision gears.
- Advantages: Provides long-lasting performance in mechanical applications.
Factors to Consider When Selecting Plastics for Automotive Parts
- Mechanical Properties: Strength, flexibility, and durability.
- Thermal Resistance: Ability to withstand high temperatures.
- Chemical Resistance: Resistance to fuels, oils, and other automotive fluids.
- Recyclability: Consideration for sustainability and environmental impact.
- Cost: Balancing material cost with performance requirements.
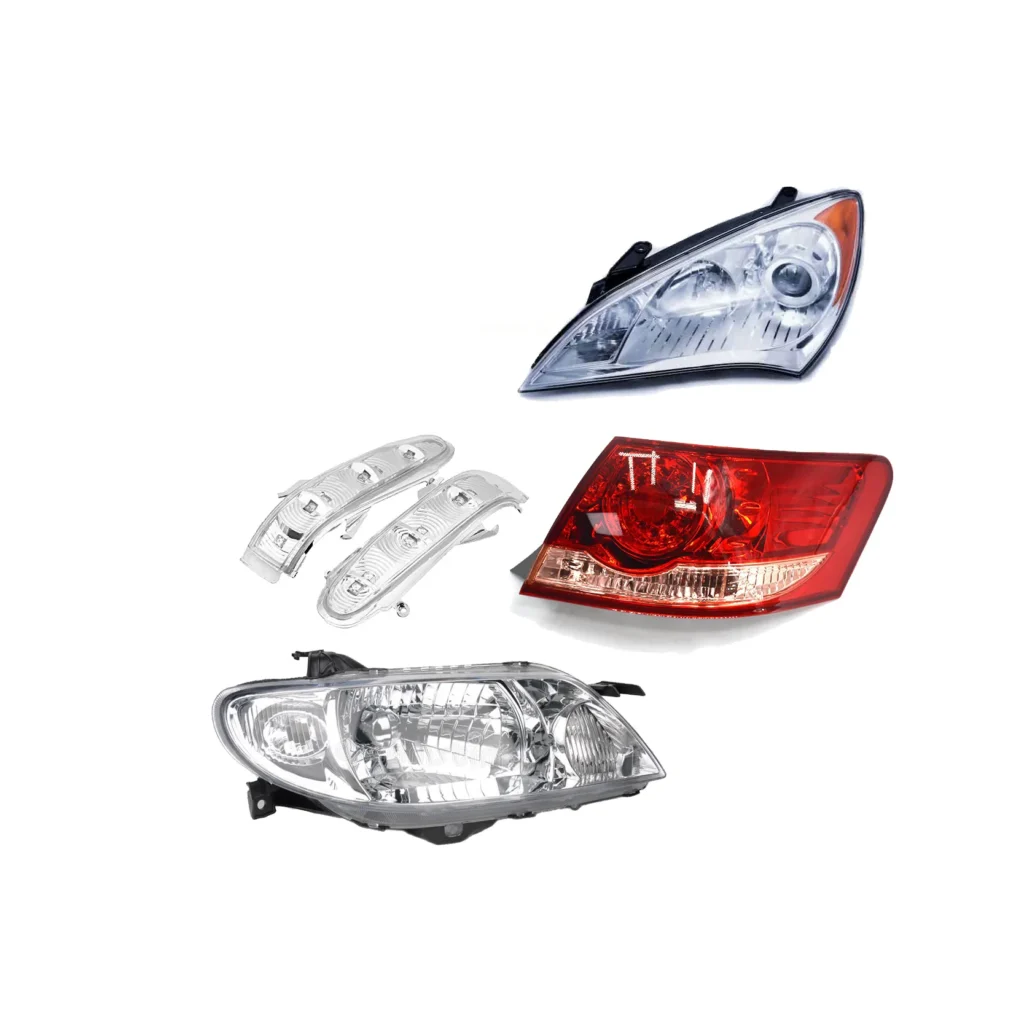
The Role of Injection Molding in Automotive Plastics Manufacturing
Injection molding is the most widely used manufacturing process for automotive plastics due to its ability to produce complex shapes with high precision and repeatability.
Advantages:
- Scalable for mass production.
- Cost-effective for high-volume runs.
- Produces parts with consistent quality.
Applications:
- Dashboard panels.
- Engine covers.
- Exterior trims.
Innovations in Automotive Plastics
Sustainable Plastics
Automotive manufacturers are incorporating recycled and bio-based plastics to reduce environmental impact.
- Examples: Recycled PET for interior trims and bio-based polyamides for engine components.
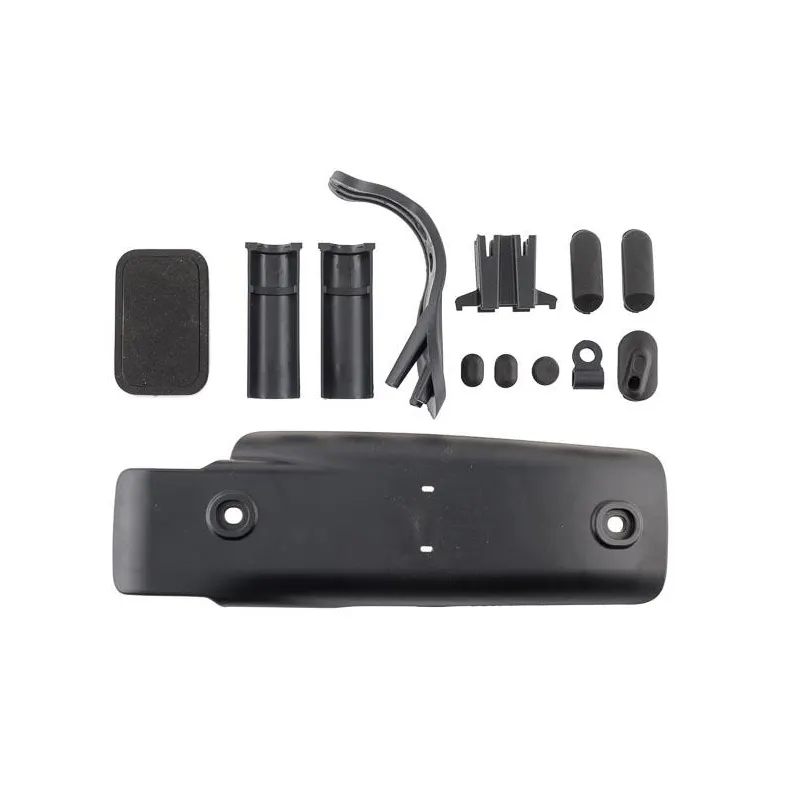
High-Performance Polymers
Advanced engineering plastics are now used for components requiring exceptional heat and wear resistance, such as turbocharger housings and fuel systems.
Why Choose BFY Mold for Automotive Parts Manufacturing?
At BFY Mold, we specialize in producing high-quality plastic components tailored to the automotive industry. Our key services include:
- Injection Molding & Mold Manufacturing: Custom molds for precision parts.
- Mass Production & On-Demand Production: Flexible solutions for all production volumes.
- CNC Processing: Advanced machining for intricate designs.
- Mirror Spark Finishing: Superior surface quality for critical components.
With our state-of-the-art factory and expertise, BFY Mold ensures top-notch quality and performance for every project.
Conclusion
Plastics play a crucial role in modern automotive manufacturing, offering a perfect blend of performance, durability, and cost efficiency. By understanding the properties and applications of various plastic types, manufacturers can optimize material selection to meet specific design and functional requirements.
Partner with BFY Mold for innovative solutions in plastic parts manufacturing. With our advanced capabilities and industry expertise, we deliver excellence in every project.