Insert molding is a highly versatile and efficient manufacturing process that involves encapsulating a preformed component, or insert, with molten plastic to create a single, integrated part. The technique is widely used in producing complex and high-performance parts across various industries, offering numerous benefits over traditional manufacturing methods.
What is Insert Molding?

Insert molding is a specialized injection molding process where pre-made inserts, typically metal or other materials, are placed into the mold cavity before the plastic injection process begins. Once the inserts are positioned correctly, molten plastic is injected into the mold, encapsulating the inserts and forming a cohesive part. This process allows for the combination of multiple materials into a single part, enhancing the functionality and durability of the final product.
Benefits of Insert Molding
- Enhanced Part Strength and Durability
- It allows for the integration of strong, rigid materials, such as metals, with flexible and lightweight plastics. This combination results in parts that are both strong and lightweight, ideal for applications requiring high structural integrity and durability.
- Improved Product Functionality
- By incorporating inserts into molded parts, manufacturers can enhance the functionality of the product. For example, metal inserts can provide electrical conductivity, heat resistance, or improved mechanical performance, making the parts suitable for demanding applications.
- Reduced Assembly Costs
- It eliminates the need for additional assembly steps, as the insert is encapsulated during the molding process. This reduces labor costs and minimizes the risk of assembly errors, leading to more efficient production and cost savings.
- Design Flexibility
- The insert molding process offers significant design flexibility, allowing for the creation of complex geometries and intricate part designs. This flexibility enables manufacturers to produce parts that meet specific performance and aesthetic requirements.
- Enhanced Aesthetics
- It can improve the visual appeal of parts by seamlessly integrating different materials and eliminating the need for visible fasteners or joints. This results in a cleaner, more professional-looking final product.
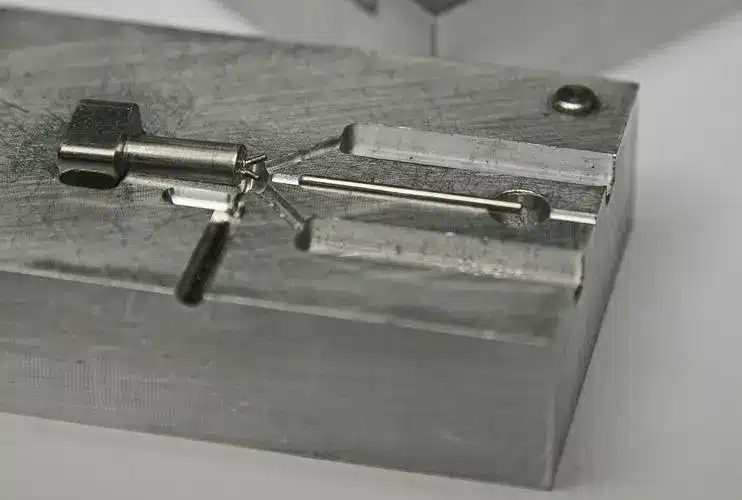
Industry Application
Insert molding is used across various industries to manufacture a wide range of products, including:
- Automotive Industry
- It is used to produce automotive components such as gears, housings, and interior trim parts. The combination of metal and plastic provides the necessary strength and durability for these demanding applications.
- Electronics Industry
- In the electronics industry, insert molding is used to create connectors, switches, and other components that require precise alignment and electrical conductivity. Metal inserts provide the necessary pathways for electrical currents while plastic encapsulation offers insulation and protection.
- Medical Devices
- Medical device manufacturers produce parts such as surgical instruments, needle hubs, and implantable devices. The process allows for the integration of biocompatible materials, ensuring the safety and functionality of the medical devices.
- Consumer Products
- Insert molding is also employed in the production of various consumer products, including kitchen appliances, power tools, and sporting goods. The technique allows for the creation of durable and aesthetically pleasing products that meet consumer expectations.
- Aerospace Industry
- The aerospace industry benefits from insert molding through the production of lightweight and strong components used in aircraft and spacecraft. The ability to combine different materials ensures that the parts can withstand extreme conditions and meet stringent performance standards.
Summary
Insert molding is a powerful manufacturing technique that offers numerous benefits, including enhanced part strength, improved functionality, reduced assembly costs, and design flexibility. Its applications span across multiple industries, making it a valuable process for producing high-quality, durable, and functional parts.
10 FAQs on Insert Molding Techniques
1. What is insert molding, and how does it improve precision?
Insert molding embeds components (e.g., metal pins, sensors) into plastic parts during injection. It achieves ±0.05mm accuracy by securing inserts in predefined cavities, eliminating post-assembly errors.
2. Which industries benefit most from insert molding?
Industry | Applications | Key Benefits |
Automotive | Sensors, connectors, bushings | Vibration resistance, weight reduction |
Electronics | Circuit boards, USB housings | EMI shielding, compact design |
Medical | Surgical tool handles, IV components | Sterility, ergonomic grips |
3. How does insert molding reduce production costs?
- Eliminates secondary assembly steps (saves $0.50–$1.20/part).
- Reduces material waste by 15–30% via precise resin flow control.
4. What materials work best for insert molding?
- Plastics: PBT (high heat resistance), LCP (low warpage).
- Inserts: Brass, stainless steel, or pre-molded silicone.
5. How to prevent insert shifting during molding?
- Use mechanical interlocks (undercuts, grooves).
- Optimize mold temperature (80–120°C) and injection speed (20–40 cm³/s).
6. Can insert molding handle complex geometries?
Yes. BFY Mold’s multi-cavity tools produce parts with 0.02mm positional accuracy, even for micro-inserts (<1mm).
7. What design considerations ensure insert durability?
- Wall thickness: 1.5–3.0mm around inserts.
- Resin selection: Glass-filled nylon for high-stress areas.
8. How does insert molding compare to overmolding?
Factor | Insert Molding | Overmolding |
Cycle Time | 20–40 seconds | 30–60 seconds |
Material Bond | Mechanical adhesion | Chemical fusion |
Cost | $0.80–$2.50/part | $1.50–$4.00/part |
9. What quality checks are critical for insert-molded parts?
- Pull tests: Verify insert bond strength (>50N for automotive parts).
- X-ray inspection: Detect voids or misalignments in sealed components.
10. Why choose BFY Mold for insert molding?
- Precision: ±0.03mm tolerance guarantees.
- Speed: Prototype tooling in 7 days, mass production in 3 weeks.
- Compliance: ISO 9001, IATF 16949, and FDA-certified processes.
About BFY Mold
At BFY Mold, we provide top-notch insert molding services and a wide range of other manufacturing solutions. With our state-of-the-art factory, we offer services in injection molding and mold manufacturing, mass production, on-demand production, CNC machining, and mirror spark. Our commitment to quality and precision ensures that we deliver exceptional products that meet the unique needs of our clients. Whether you need complex geometries, high-performance parts, or aesthetically pleasing products, BFY Mold is your trusted partner for all your manufacturing needs.