1. What is ABS Plastic?
Glossy Acrylonitrile Butadiene Styrene (ABS) is a specific type of thermoplastic polymer that combines strength to withstand shocks, toughness, and freedom from impact. It has a broad use across old-line industries stretching from automotive to electronics, toys, and household goods. ABS is made through a process called polymerization, where acrylonitrile, butadiene, and styrene are combined, which each gives the material specific properties:

- Acrylonitrile contributes to chemical resistance and heat stability.
- Butadiene enhances impact resistance and toughness.
- Styrene provides rigidity and a glossy finish.
ABS has been widely used in the manufacturing process of injection molding. This process makes the most out of ABS’s excellent mechanical properties, such as its high impact resistance and toughness. ABS injection molding is ideal for making items that need strength and durability and is commonly used for automotive dashboards, electronic housings, and appliance components.
2. Types of ABS Plastics
There are many types or grades of ABS plastics for many applications. The main types include:
- ABS Standard: The most popular grade, providing a compromise of strength, flexibility, and processability. It has favorable properties when it comes to injection molding.
- High-Impact ABS (HI-ABS): This grade is designed with improved toughness and impact resistance, making it suitable for applications like automotive parts or protective cases.
- Flame-Retardant ABS: Additives in this type of ABS reduce the plastic’s flammability, making it ideal for use in electrical components and household goods that require flame resistance.
- ABS/Polycarbonate (PC) Blends: This material is a hybrid of the two. It’s commonly used for electronic housings.
- ABS Plus: A newer variant of ABS with superior surface quality and ideal processing properties for producing smooth, high-precision end products.
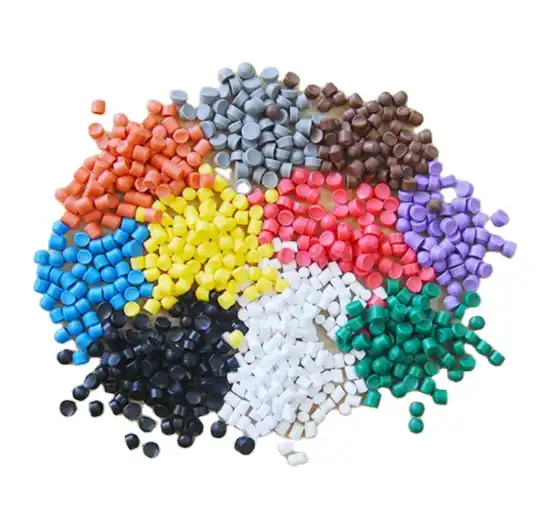
Several types of ABS plastic provide various benefits, and each has a specific grade suited for different applications that typically consider factors such as strength, durability, and resistance to environmental conditions.
6 Properties of ABS Materials
Impact Resistance: ABS is used in products subjected to physical stress, such as automotive parts and electronics, due to its high durability and impact resistance.
Rigidity and Toughness: Provides a good balance of rigidity and toughness and is used in demanding applications.
Thermal Stability: It accepts heat without much impact (up to 100°C/212°F), making it perfect for heat resistance in automotive and electronics.
Aesthetic Appeal: Its smooth, glossy surface can be easily painted or textured, making it ideal for consumer products such as toys and electronics.
Easy to Process: ABS is a material that is easy to mold and shape, especially in injection molding, which can provide complex designs with little waste.
Chemical Resistance: Many chemicals are unaffected, but solvents such as acetone can make an impact.
3. Performance of ABS
Performance of ABS
ABS plastic has excellent mechanical properties and is suitable for many applications. Key capabilities for performance include:

Physical Properties
Because of the procedures in which it is made, ABS has very good mechanical properties — hardness, rigidity, and toughness. Thus, it is frequently utilized as an all-purpose engineering plastic. ABS resins are white or light cream in color, opaque, non-toxic, and have an approximate density of 1.05. The melt flow rate is from 0.2% to 0.7%. When burned, it emits a yellow flame, produces black smoke, and does not drip or soften without dripping.
Heat Resistance
ABS is heat-resistant but moderate, with a 1.86MPa thermal deformation temperature of around 85°C. 10 °C can raise this temperature via heat treatment, and the range of ABS use is 40 °C to 85 °C while exceeding 100 °C is not recommended. ABS’s thermal conductivity wides from 0.16 to 0.29W/(m·K), and the linear expansion coefficient is (6.2-9.5) × 10⁻⁵K⁻¹. As a result, it has one of the lowest coefficients of expansion among thermoplastics, making it great for creating precise dimensional parts.
Mechanical Properties
It is a tough thermoplastic with high impact strength. Thanks to the energy absorption properties of the rubber component, this could prevent the formation of silver lines. Acrylonitrile Butadiene Styrene has high impact strength and decent low-temperature toughness, even below -40C. It also exhibits great creep resistance, with corresponding pipes under a 7.2MPa loading, keeping their size for two years.
Chemical Resistance
ABS resists water, inorganic salts, alkalis, and dilute acids. However, it is sensitive to oxidizing acids such as agricultural sulfuric and nitric acids. Stress cracking comes from prolonged exposure to aliphatic hydrocarbons, alcohol, mineral, and vegetable oils. ABS might dissolve in ethyl acetate, acetone, and methylene chloride, or it might form emulsions.
Weather Resistance
Its structure contains double bonds, which make ABS more footloose to sunlight, heat, and oxygen. Ultimately, this leads to oxidation and degradation. For example, after six months of outdoor exposure, ABS will lose 45% of its impact strength. UV light, heat, and oxygen make it brittle. Additives such as carbon black or phenolic antioxidants are commonly incorporated to enhance weather ability.
4. ABS Injection Molding Guide
ABS injection molding is one of the most popular processes for manufacturing parts composed of Acrylonitrile Butadiene Styrene. Here are the steps used in ABS injection molding:

Step 1 — Material Preparation
The ABS pellets are loaded into the injection machine. They are heated to a molten state and ready to be injected into the mold.
Step 2 — Injection into the Mold
Melted ABS is injected into the mold cavity under high pressure. The injection process is carefully regulated to guarantee that the material completely and uniformly penetrates the mold.
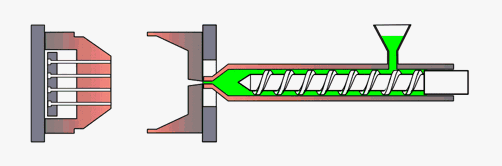
Step 3 — Cooling and Solidifying
Once injected, the mold is cooled, causing the ABS to solidify into the targeted form. Cooling time differs depending on the part thickness and the mold design.
Step 4 — Opening the Mold and Removing the Parts
Once the part cools and solidifies, the mold opens, and the part is ejected. It is then inspected for defects and quality before proceeding to the next phase of the process.
Step 5 — Post-processing (If Required)
Depending on the application, the molded ABS part may be subject to trimming, painting, or surface finishing.
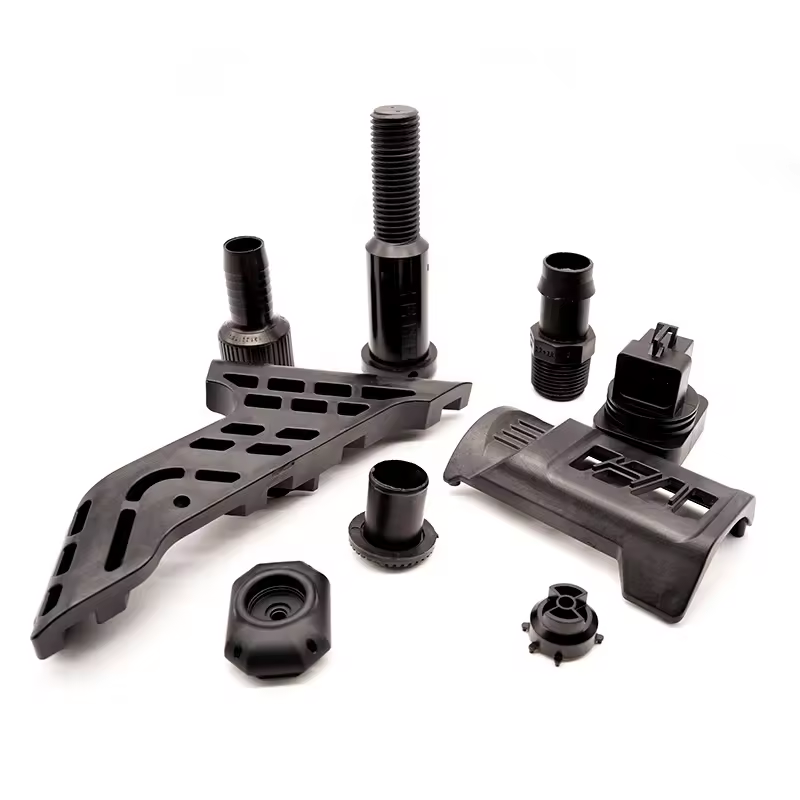
3 Tips to Successful ABS Injection Molding:
- Temperature Control: The barrel, mold, and material temperature should be controlled to prevent defects such as warping, poor surface finish, etc.
- Injection Speed: The injection speed must be adjusted carefully to avoid issues like short shots or incomplete filling.
- Ejection: When a part is ejected from a mold, it must be solidified enough for the part to maintain its shape, so a sufficient amount of cooling time is needed to wear the part so that it is non-deformable on ejection.
ABS Injection Mold Temperature Guide
Parts’ shrinkage rate increases and the molding cycle lengthens. The heated mold method is used to address this. Mold temperatures of 60-70°C are ideal for parts with high surface quality, complex shapes, and performance requirements.
ABS Injection Molding Pressure
Injection pressure depends on wall thickness, equipment type, and resin grade. Higher pressure is better for thin-wall, long-process, small-gate, heat-resistant, or flame-retardant products. This helps fill the cavity, but excessive pressure can cause release issues or damage. For minimal internal stress, control the pressure holding at 60-70MPa.
ABS Injection Molding Speed
Injection speed affects ABS melt fluidity. Slow speeds can cause surface defects like corrugation and poor welding. Fast speeds leave insufficient time for proper mold filling, resulting in poor surface finish. For normal production, use medium to low speeds. High speeds are only needed for tricky mold filling.
ABS Plastic Forming Post-Processing
ABS parts may have internal stress. Low-usage parts need heat treatment. Heat high-performance parts at 70-80°C for 24 hours, then let them cool to room temperature. To test internal stress, soak parts in glacial acetic acid. If no cracks appear after 2 minutes, stress is low. Cracks within 5-15 seconds indicate high internal stress.
6 Key Advantages of ABS Injection Molding
Impact Resistance and Durability – ABS is incredibly strong and tough, making it a great option for products that will endure wear and tear. It is ideal for mechanically stressed components, such as automotive parts or electronic housings, and assures that they remain intact under difficult conditions.
Low Material Cost – Extensive use of ABS can keep part costs low and, hence, overall production costs. Its ease of processing via injection molding allows for mass production without compromising quality, and its cost efficiency for mass production runs is on a whole other level.
Facilitates Molding or Design flexibility – Due to its good fluidity, ABS is less likely to have defects, such as distortion or incomplete filling, and thus is easy to process for injection molding. It also facilitates the ability to produce complex shapes and intricate designs, allowing manufacturers to create fine-featured, functional compositions accurately.
Great Aesthetic Finish – ABS parts’ glassy tops give them a highly sought-after finish that many products seek for a cleaner look. They are simple to paint, texture, or finish with the highest-quality visual result, requiring no additional steps, which makes them perfect for consumer-facing products.
Excellent Temperature Resistance – ABS performs well under moderate-temperature environments, making it experience and work experience capable of operating in automotive or electrical applications where parts may be exposed to higher temperatures. It stands up to heat without compromising its structure or performance.
Wide Range of Applications – ABS is a commonly used thermoplastic polymer in a multitude of industries, from automotive parts to consumer electronics to medical devices. It can be enhanced with additives (e.g., flame retardants), providing flexibility with respect to performance. The supply chain will also be much more flexible.
5. ABS Plastic Injection Molding Problems and How to Solve Them
ABS is a widely used injection molding material; however, there are a few challenges in the injection molding process. Here are some of the common issues and how to prevent them:

Issue | Cause | Solution |
Warpage | Uneven cooling or mold design issues | Adjust cooling channels and molding parameters |
Short Shots | Inadequate injection pressure or improper mold temperature | Increase injection pressure and optimize mold temperature |
Flow Marks | High injection speed or improper mold temperature | Reduce injection speed and fine-tune mold temperature |
Sink Marks | Thick-walled parts with improper cooling | Optimize wall thickness and cooling time |
Air Traps | Poor venting in the mold cavity | Improve mold venting and exhaust systems |
Surface Imperfections | Contamination or moisture in material | Ensure proper material drying and mold cleanliness |
Addressing these issues early in molding can improve product quality and reduce scrap rates.
Conclusion
Tough and inexpensive, ABS plastic is a trusted material for thousands of applications. By knowing its types, performance, and injection molding process, manufacturers can optimize production, improve product quality, reduce costs, etc. Additionally, ABS injection molding is especially beneficial for components requiring high strength and impact resistance, provided that optimal mold design, material preparation, and processing parameters are undertaken.
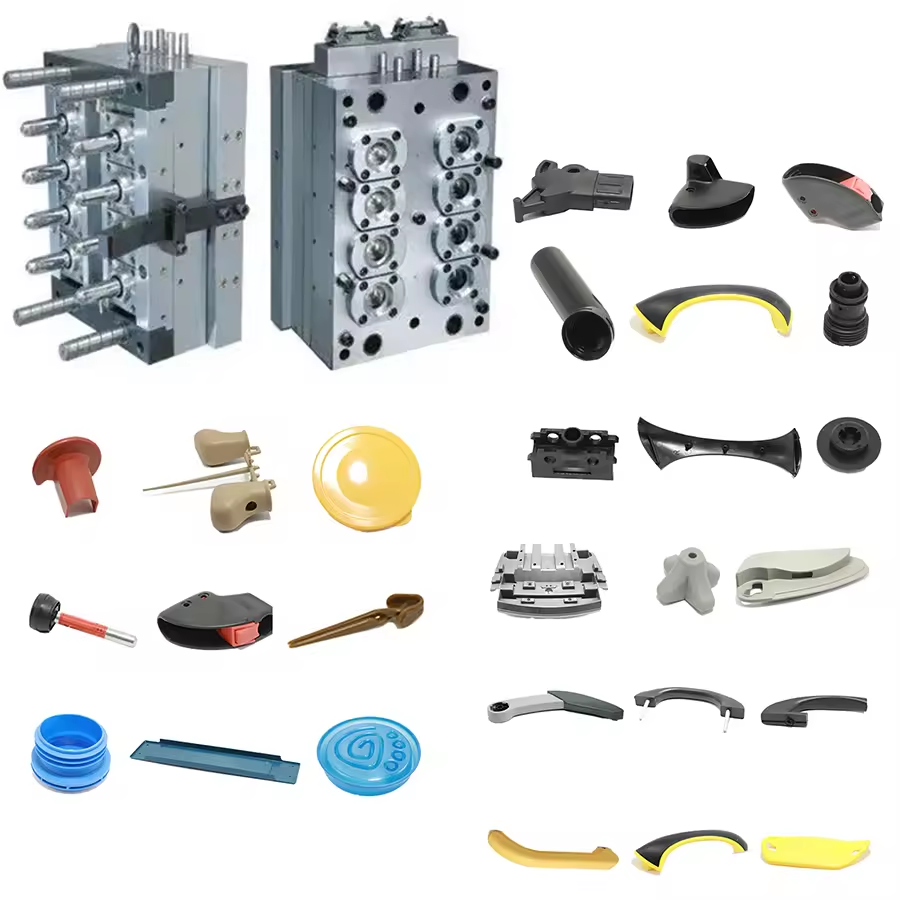
About BFY Mold
BFY Mold focuses on injection molding and mold manufacturing, providing mass production, on-demand production, CNC processing, and mirror spark finishing services. Our well-equipped in-house factory and dedicated, skilled labor can guarantee a high-quality, low-cost solution to your project.
Contact BFY Mold today to begin your new ABS injection molding projects!
Top 10 FAQs About ABS Injection Molding
1. What makes ABS a preferred material for injection molding?
ABS (Acrylonitrile Butadiene Styrene) offers high-impact resistance, excellent machinability, and cost-effectiveness. Its balanced properties (e.g., tensile strength: 40–50 MPa, heat resistance up to 80°C) make it ideal for automotive trim, consumer electronics, and industrial housings.
2. What certifications should an ABS injection molding supplier have?
Verify ISO 9001 (quality management), IATF 16949 (automotive), and UL certification for flame-retardant grades (e.g., ABS+PC). For medical applications, ensure ISO 13485 compliance.
3. How do you prevent warping or sink marks in ABS parts?
- Optimized Cooling: Maintain mold temperature at 60–80°C.
- Uniform Wall Thickness: Design walls between 1.2–3.5mm.
- Material Drying: Preheat ABS pellets at 80–90°C for 2–4 hours to reduce moisture.
4. What surface finishes can be achieved with ABS injection molding?
- SPI Standards: Glossy (SPI-A1), textured (SPI-C1), or matte (SPI-D3).
- Post-processing: Painting, electroplating, or laser etching for branding.
5. What is the typical tooling cost for ABS injection molds?
- Aluminum molds: 3,000–3,000–15,000 (prototyping/low-volume).
- Steel molds: 15,000–15,000–80,000+ (high-volume production).
Costs vary with part complexity, cavity count, and surface finishes.
6. Can recycled ABS be used in injection molding?
Yes, but ensure:
- Post-consumer ABS meets FDA 21 CFR for food-contact applications.
- Recycled content ≤30% to maintain mechanical properties.
- Suppliers provide material traceability and testing reports.
7. How does ABS compare to other plastics like PP or PC?
Property | ABS | PP | PC |
Impact Strength | High | Moderate | Very High |
Heat Resistance | 80°C | 100°C | 130°C |
Cost | $2–4/kg | $1–3/kg | $4–8/kg |
ABS balances cost and performance, while PC excels in high-heat applications. |
8. What industries commonly use ABS injection molding?
- Automotive: Dashboard components, interior trim.
- Electronics: Keyboard keys, printer housings.
- Appliances: Vacuum cleaner parts, refrigerator liners.
9. How do suppliers ensure color consistency in ABS parts?
- Masterbatch Mixing: Precise pigment dosing for uniform color.
- In-Line Spectrophotometers: Real-time color monitoring.
- Batch Testing: Compare against Pantone or RAL standards.
10. What post-molding support do ABS suppliers provide?
- Assembly Services: Ultrasonic welding or snap-fit integration.
- Quality Assurance: CMM reports, drop testing, and flammability checks.
- Inventory Management: JIT (Just-in-Time) delivery to reduce warehousing costs.