Metals comprise the gist of manufacturing processes, specifically in mold and mass production. When it comes to metals, they all have different properties that make them better suited for certain things than others. This blog will discuss 20 types of metals, their traits, and their applications in injection molding, CNC machining, and mold manufacturing. Whether your projects are high-volume production runs or custom builds, knowing these metals’ properties will help you make educated selections of materials.
The Characteristics of Different Types of Metal Materials
1. Stainless Steel
Anyway, stainless steel is an alloy of iron, chromium, and other elements, giving it a remarkable resistance against corrosion and staining. It is very durable and strong and has plentiful resistance to oxidation and rust even in high humidity conditions. It is also fairly easy to clean, making it ideal for food safety applications. And because stainless steel can withstand extreme heat and high-pressure environments, it is versatile in many industries.
This article is focused on high-volume production molds (in which hundreds of thousands of parts will be produced in a given time), specifically for manufacturers involved in food processing. Stainless steel’s corrosion resistance is critical in manufacturing injection molds in industries like food and related sectors where cleanliness and sturdiness are needed. Stainless steel finds application in machinery components, tools, and even surgical instruments.

2. Aluminum
Aluminum is one of the most commonly used metals thanks to its lightweight nature, high strength-to-weight ratio, and excellent corrosion resistance. Due to its ease of machining and forming, it is commonly used for molds in which detail and precision are paramount. As it has very high thermal and electrical conductivity, aluminum is ideal for heat dissipation applications.
Aluminum is a commonly used material for mold making, aimed at prototype and low-quantity production. It is relatively inexpensive and easy to machine. Aluminum molds are commonly favored in the automotive, aerospace, and consumer goods industries, where lightweight and high-precision components are necessary. They’re also used in the production of products such as electronics, HVAC systems, and components needing effective heat dissipation.
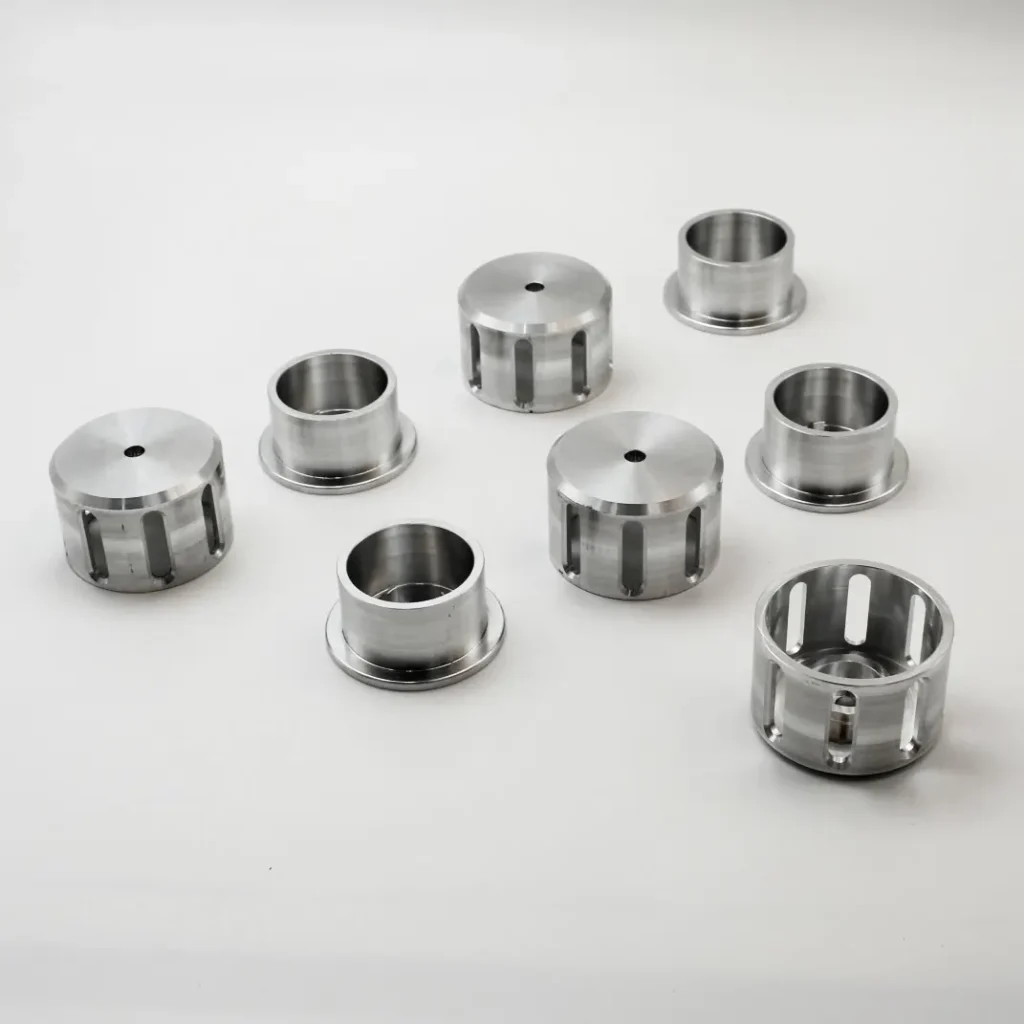
3. Carbon Steel
The filler material will be carbon steel, which is the main alloying element in steel. Low, medium, or high carbon steels also exist, segmented by how much carbon the steel contains. Each offers different properties regarding hardness, ductility, or strength. Carbon steel has high durability, low cost, and good tensile strength, which makes it the best option for heavy-duty applications.
Carbon steel is usually used to make high-strength tools and other parts. It is also commonly specified for large-volume molds demanding toughness but not the high wear resistance of tool steels. The automotive, manufacturing, and construction sectors also regularly use carbon steel molds.

4. Tool Steel
It can be carbon or alloy, and its hardened state is commonly used for tools, hence the name tool steel. Its mechanical properties are frequently improved by heat treatment. It’s made especially for forming tools, dies, and molds, where wear resistance, toughness, and pressure-holding ability for sharp edges are important. Moreover, due to its resistance to thermal fatigue, it is an excellent material for molds that go through various heating and cooling cycles.
Tool steels are vital in forming paring in molds, including injection molding, die-casting, and stamping. Tool steel grades include D2, H13, and A2, which are commonly used in automotive, aerospace, and precision manufacturing, where durability and precision are of the utmost importance.
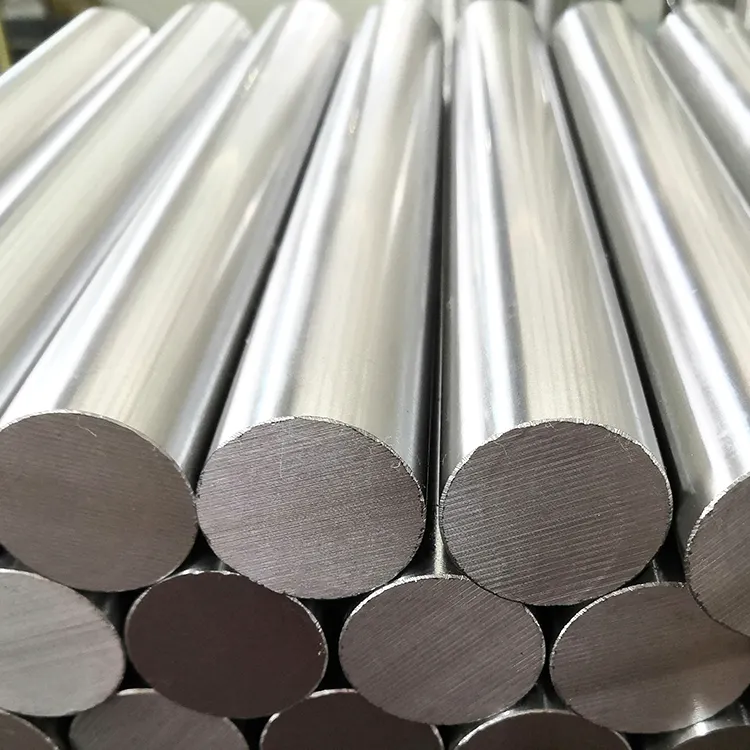
5. Brass
Brass—an alloy of copper and zinc—has a unique blend of strength, corrosion resistance, and aesthetic appeal. It has good machineability, great electrical conductivity, and rust and corrosion resistance. Brass is also recognized for its golden finish, making it sought after to be used as much in decorative and functional applications.
Brass is widely used in mold-making compound molding for parts that need intricate designs and good wear resistance. The most common uses for copper include electrical connectors, fittings, and components in industries like automotive and electronics and decorative housing for wiring in jewelry, plumbing, and hardware.

6. Copper
Copper is a ductile, malleable metal with high thermal and electrical conductivity. It also has excellent corrosion resistance and is resistant to the effects of moisture, air, and some acids. It is easy to form and weld, making copper a good material for many manufacturing applications. Combined with its reddish-brown hue and natural antimicrobial properties, bamboo is appealing in specific health-oriented applications.
Copper is often used in electrical parts, heat exchangers, and precision molds that demand fast heat conduction. Copper is also used for its fast heat dissipation properties, which is useful in industries like electronics and automotive, where being able to cool rapidly is vital.
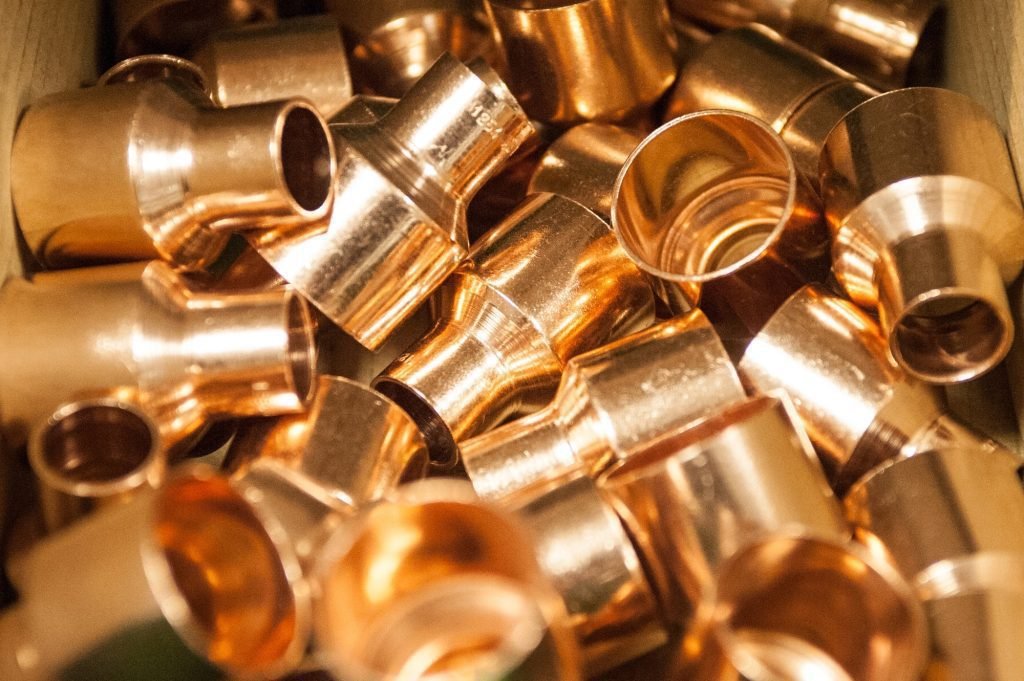
7. Bronze
Bronze is a copper-tin alloy that is more corrosion-resistant than others, particularly in marine settings. It is more robust and harder than pure copper but is still extremely machinable. In addition, Bronze has excellent resistance to wear and low friction, which is also why it is used in moving parts that are expected to work for a long time.
Bronze is used in high-wear applications, like bearings, gears, and bushings. It is also used in mold making to manufacture high-performance parts that face constant abrasion or need to endure extreme environmental conditions. Bronze is often used in the aerospace, automotive, and industrial industries.

8. Titanium
Titanium is a robust metal with a high specific strength and excellent resistance to corrosion and high-temperature degradation. It has one of the best strength-to-weight ratios among metals, perfect for weight-sensitive applications. Its low density makes it useful in aerospace applications. In contrast, its high corrosion resistance from salt water and chemicals makes it useful in any number of industries where exposure to harsh conditions is common.
Used in aerospace, medical, and high-performance manufacturing. Titanium is utilized for mold making where high temperatures and pressures are present, such as in aerospace component production, medical devices, and other high-performance automotive parts. This is especially useful in molds that require strength without the weight of excess material.

9. Nickel
Nickel is an odorless, silvery-white metallic element with high ductility, corrosion resistance, and high-temperature stability. Its high melting point makes it suitable for higher-heat environments. Nickel alloys are renowned for their oxidation and wear resistance and for their ability to perform in extreme and industrial environments.
Nickel is commonly used in high-stress, high-temperature mold making and tooling applications. This form of additive machining is frequently utilized in the aerospace, chemical, and energy manufacturing sectors when molds and tools are needed that will withstand severe wear and high temperatures. Nickel is also vital to producing corrosion-resistant parts for marine and chemical processing applications.
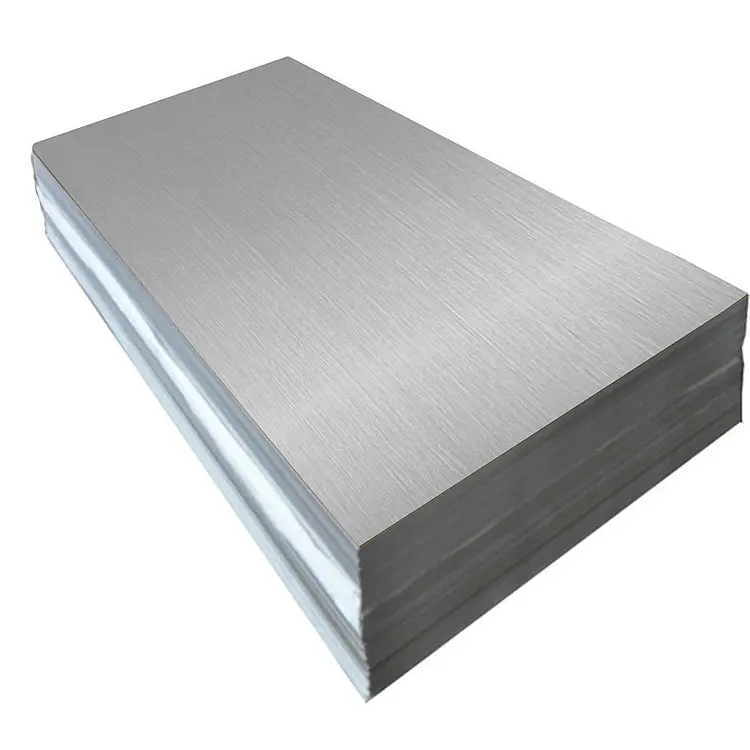
10. Zinc
It is a soft, malleable metal that offers good corrosion resistance — a positive characteristic when used in applications exposed to moisture and atmospheric elements. It can be cast and molded readily, thus demonstrating its utility in die-casting. The relatively low melting point of zinc allows for rapid production cycles.
Examples of zinc die-cast parts include diecast aluminum, Which is used in die-casting to make things like engine parts, electrical connectors, and consumer products. Because of this, Zamak or zinc alloys are widely used for mass-production molds. It has extensive applications in the automotive, electronics, and construction industries.
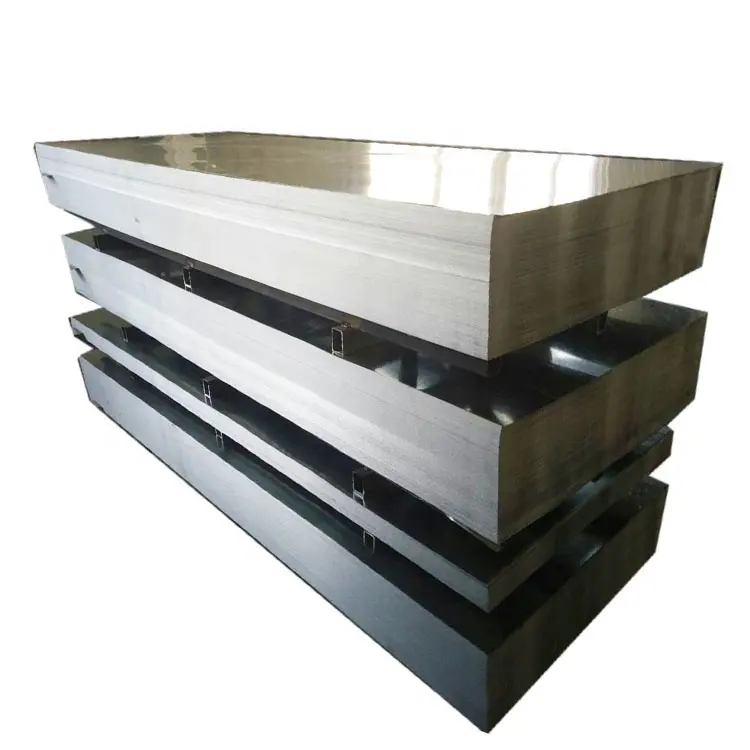
11. Molybdenum
Molybdenum is a dense metal with excellent anti-corrosive properties, maintaining hardness at very high working temperatures. The major use of alloy steels and superalloys increases the final product quite significantly in terms of heat and wear resistance. It also has resistance to fatigue and endurance in high-stress environments.
Molybdenum is used primarily in the aerospace, automotive, and energy industries for components that need extreme heat and strength. It is frequently applied in the manufacture of molds for components that need to withstand high temperatures or corrosive environments, such as turbine blades, heating elements, and heavy-duty machinery.
12. Tungsten
One of the heaviest metals or with the highest melting point, tungsten is extremely resistant to both heat and wear. It’s very hard and dense, so it has a wide range of applications where high wear resistance and high temperature are required. Tungsten is corrosion-resistant as well but can be brittle in certain conditions.
Tungsten is widely used in processing high-performance molds, cutting tools, and wear-resistant parts, especially in the aerospace, military and heavy machinery industries. It is suitable for use in high-wear and high-heat mold-making applications where conventional metals would simply wear out too soon.

13. Inconel
Inconel is a series of superalloys made from nickel and chromium. It grows strong with exposure to heat and is highly resistant to oxidation, making it very productive in extreme heat, high-pressure, and corrosive environments. Inconel also retains high strength at elevated temperatures.
Some industries employing Inconel are aerospace, chemical processing, and power generation. It is commonly used in mold making for manufacturing parts that must operate in high-temperature environments, such as engine turbine blades, exhaust systems, and other demanding parts.

14. High-Speed Steel (HSS)
High-speed steel is a class of tool steel designed to retain its hardness and cutting edge when used at high temperatures. It is particularly known for its fast, efficient cutting and is often used in high-performance cutting and shaping tools and molds.
HSS is widely used for precision making of molds, as well as for cutting tools, drill bits, and machine tools. This is the best fit for automotive, aerospace, metalworking, and manufacturing when you need to hurry up CNC machining.
15. Cast Iron
Cast iron is a robust metallic material composed of iron, carbon, and silicon. Due to its good casting properties, it is used for complex shapes. Cast iron is also very wear-resistant and resistant to deformation but can shatter with impact.
Cast iron molds are used to make parts that need high strength and wear resistance, such as heavy machinery parts, engine blocks, and pipes. Automotive, construction, and machinery manufacturing are common industries that use cast iron.
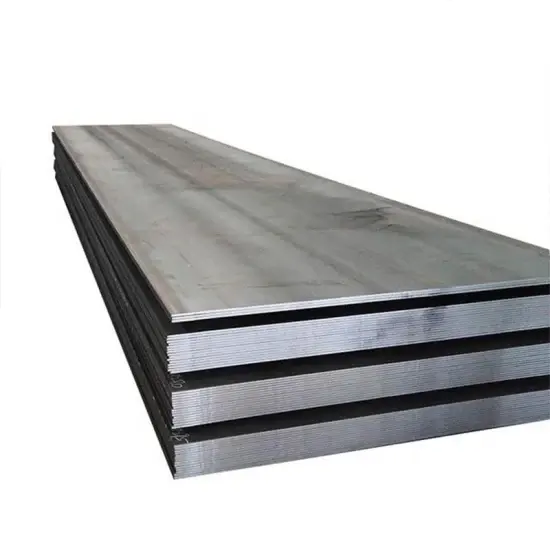
16. Forged Steel
Both are made by heating steel to its molten point and pouring it into a mold to set, but forged steel is made by applying heat and pressure to flex the steel, hardening it to be stronger than cast steel. This makes it fatigue—and stress-resistant with high tensile strength. Forged steel can handle extreme forces and is ideal for components in a high-load or high-stress environment.
This is used in high-stress applications such as tool manufacturing, mold making, and parts for machinery and heavy-duty equipment. Its resilience makes it well-suited for molds in the automotive and aerospace industries.
17. Duralumin
Duralumin is a lightweight alloy that adds copper to aluminum, making it stronger than pure aluminum. It is much more resistant to corrosion and extremely durable, but it is lighter than most other metals. This makes it extremely popular for weight-sensitive applications without sacrificing strength.
Duralumin is a common emergence in aerospace and military engineers for operational devices and structural honesty. In mold making, it is utilized for lightweight molds that require high strength like molds for consumer electronics and automotive components.
18. Stainless Steel 17-4 PH
17-4 PH, stainless steel 17-4 PH is a precipitation-hardening nobility steel that offers superior mechanical properties and corrosion resistance combined with ease of machining. It was often used in demanding applications due to its strength and corrosion resistance.
Widely used for fatigue and extreme environment handling, 17-4 PH stainless steel is used in aerospace, chemical processing, and high-stress mold applications. It is frequently chosen for precision molds and die-making.
19. Alloy Steel
Alloy steel incorporates extra alloying elements like chromium, nickel, or vanadium to further improve its mechanical properties. These elements enhance the steel’s hardenability, toughness, and resistance to corrosion and wear. They are famously well-suited for high stress, extreme conditions, and a myriad of engineering applications.
When it is not advisable to use high-resistance steels for heavy-duty mold states, it is better to use alloy steels. This is particularly true where tools and molds are subjected to heavy loads, such as in the construction, automotive, and aerospace industries.
20. Lead-Free Steel
Lead-free steel is an environmentally sound substitute for conventional lead-containing steel. It has a lot of the same mechanical properties (strength, hardness, toughness, etc.) but is much safer and more sustainable than regular steel.
Lead-free steel is used in numerous industrial activities, such as automotive components, mold design, machinery, etc. It is especially useful for projects where reinforcement of environmental laws is required.
Chemical Properties of Metals Used in Injection Molds
Metal Type | Advantages | Approximate Price Range (per kg) | Industry Applications | Chemical Properties |
Stainless Steel (e.g., 420, 440C, H13) | – Excellent corrosion resistance – High durability – Retains hardness at high temperatures – Ideal for high-volume, high-precision molds | $8 – $15 | Automotive, Medical, Consumer Goods Used for producing long-lasting, high-precision molds with excellent corrosion resistance. | Composition: Iron (Fe), Chromium (Cr) (12-18%), Nickel (Ni) (6-10%), Molybdenum (Mo) (2-3%). Properties: High corrosion resistance, magnetic properties, good weldability, and can be hardened through heat treatment. |
Aluminum (e.g., 7075, 6061) | – Lightweight – Excellent thermal conductivity – Cost-effective for prototype and low-volume molds – Easy to machine | $4 – $7 | Prototype Molding, Consumer Electronics, Automotive Preferred for fast, low-cost tooling, especially in prototyping and short-run production. | Composition: Aluminum (Al) (90-98%), Silicon (Si) (0.4-0.8%), Magnesium (Mg) (1.2-1.8%), Copper (Cu) (0.2-0.4%). Properties: Lightweight, high thermal conductivity, corrosion-resistant, and high strength-to-weight ratio. |
Carbon Steel (e.g., 1045, P20) | – High tensile strength – Cost-effective – Good wear resistance – Suitable for low-to-medium-volume molds | $2 – $5 | General Manufacturing, Packaging, Automotive Common in mass production and low-to-medium-volume applications. | Composition: Iron (Fe), Carbon (C) (0.45%), Manganese (Mn) (0.6-0.9%), Silicon (Si) (0.1-0.4%). Properties: High strength, relatively low corrosion resistance, can be heat-treated for additional hardness. |
Tool Steel (e.g., H13, D2, S7) | – Excellent wear resistance – Hardness retention at high temperatures – Ideal for high-precision molds and tools | $12 – $25 | Automotive, Aerospace, Medical Devices Used for durable, high-precision molds that require strength and resistance to heat and wear. | Composition: Iron (Fe), Carbon (C) (0.5-1.5%), Chromium (Cr) (5-12%), Vanadium (V) (0.5-2%), Molybdenum (Mo) (0.3-2%). Properties: High hardness, wear resistance, and toughness, especially after heat treatment. |
Brass (e.g., C36000) | – Excellent machinability – Good corrosion resistance – Aesthetic finish – Ideal for small, intricate molds | $7 – $12 | Consumer Goods, Decorative Items, Electrical Components Ideal for molds requiring intricate details and smooth finishes, such as in electronics and decorative products. | Composition: Copper (Cu) (60-90%), Zinc (Zn) (10-40%), Small amounts of Lead (Pb) for machinability. Properties: High machinability, corrosion-resistant, good conductivity, and attractive golden color. |
Copper (e.g., C10100) | – Excellent thermal conductivity – Good corrosion resistance – High machinability | $8 – $15 | Electronics, Automotive, Aerospace Used for molds that require rapid heat dissipation, especially in high-precision molding of electronic components. | Composition: Copper (Cu) (99.9% pure). Properties: Superior thermal and electrical conductivity, corrosion-resistant, excellent machinability. |
Bronze (e.g., C93200) | – High wear resistance – Low friction – Excellent corrosion resistance | $8 – $18 | Aerospace, Automotive, Industrial Equipment Frequently used in high-performance applications requiring superior wear resistance and low friction. | Composition: Copper (Cu) (85-90%), Tin (Sn) (5-7%), Lead (Pb) (5-7%). Properties: High strength, good corrosion resistance, and low friction properties. |
Nickel Alloys (e.g., Inconel 718) | – High resistance to oxidation and heat – Excellent strength at high temperatures | $50 – $120 | Aerospace, Power Generation, High-Temperature Applications Used in molds exposed to high-stress and high-heat environments such as in the aerospace and power generation industries. | Composition: Nickel (Ni) (50-60%), Chromium (Cr) (17-21%), Iron (Fe), Molybdenum (Mo) (3-5%), Titanium (Ti) (0.9-1.3%). Properties: Exceptional high-temperature strength, oxidation resistance, and corrosion resistance. |
Zinc Alloys (e.g., Zamak) | – Low melting point – High fluidity for detailed molds – Cost-effective for mass production | $3 – $5 | Automotive, Consumer Electronics, Household Products Ideal for high-volume, low-cost mold applications with detailed, complex shapes. | Composition: Zinc (Zn) (95-99%), Aluminum (Al) (0.5-4%), Copper (Cu) (0.5%), Magnesium (Mg) (0.03%). Properties: Low melting point, excellent fluidity, good corrosion resistance. |
Forged Steel (e.g., 4140) | – High toughness – Excellent fatigue resistance – Ideal for high-stress applications | $6 – $12 | Automotive, Heavy Machinery, Military Often used in molds exposed to heavy-duty stress and pressure. | Composition: Iron (Fe), Carbon (C) (0.38-0.43%), Chromium (Cr) (0.8-1.1%), Molybdenum (Mo) (0.15-0.25%), Manganese (Mn) (0.75-1.0%). Properties: High toughness, good fatigue resistance, and hardness. |
Alloy Steel (e.g., 4340) | – Improved hardness and toughness – Corrosion-resistant – Suitable for heavy-duty tools and molds | $6 – $10 | Automotive, Aerospace, Military Used in mold manufacturing for applications requiring high strength and resistance to wear. | Composition: Iron (Fe), Carbon (C) (0.38-0.43%), Chromium (Cr) (0.7-0.9%), Nickel (Ni) (1.6-2.0%), Molybdenum (Mo) (0.2-0.3%). Properties: High tensile strength, good impact resistance, excellent wear resistance. |
Explanation of Chemical Properties:
Iron (Fe): The principal element in most metals, it provides strength and durability.
Chromium (Cr): Increases corrosion resistance, hardness, and wear resistance. Contains a Passivation Layer (commonly seen in Stainless Steel)
Nickel (Ni): Provides strength, toughness, and resistance to corrosion. It is commonly found in high-temperature alloys such as INCONEL.
Copper (Cu): Well known for its great thermal and electrical conductivity, it is used in some high-conductivity molds.
Lightweight, corrosion-resistant, good thermal conductivity. Found in thin-wall structures such as 6061.
Tin (Sn): Used in bronze; adds corrosion resistance and improves strength.
Molybdenum (Mo): Improves temperature and wear resistance of the steel.
Magnesium (Mg): Increases the strength-to-weight Ratio and is used in alloys such as Zinc and Aluminium.
Common Choices of Metal Types in Processing and Production
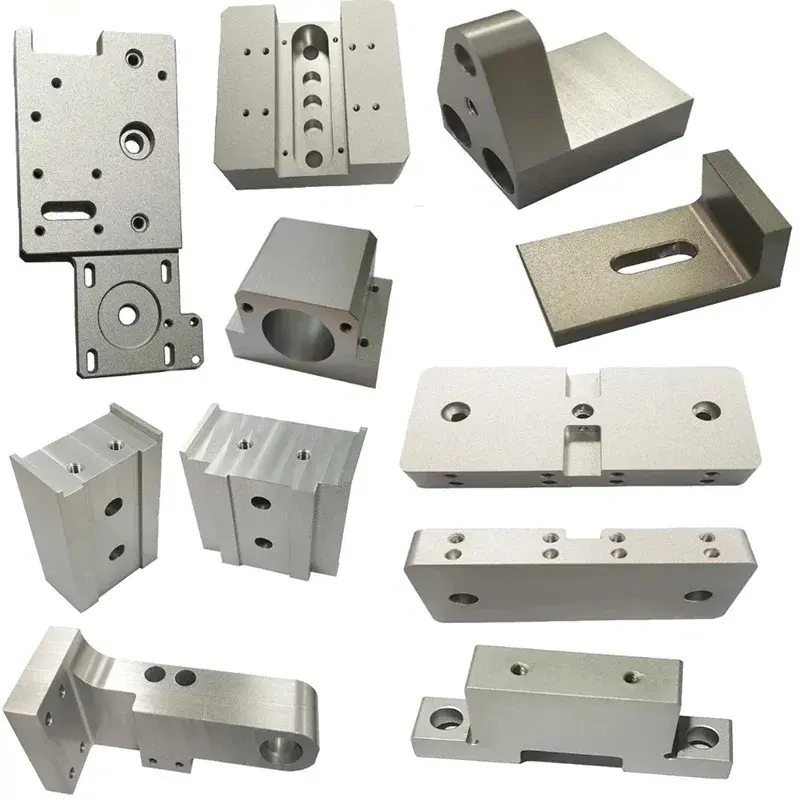
There are several things to consider when choosing the best type of metal for your mold manufacturing process:
Sturdiness Required:
- For heavy molds, tool steel, alloy steel, or high-speed steel are usually chosen because of their strength and toughness under large pressure.
Corrosion Resistance:
- Materials like stainless steel, bronze, and Inconel are commonly chosen when the mold is exposed to aggressive environments.
Heat Resistance:
- Titanium, tungsten, and molybdenum are good materials for applications in high-temperature molds.
Machinability:
- Metals such as aluminum, brass, and copper are also used frequently because they are easy to machine and shape.
Cost Considerations:
- Zinc, aluminum, and lead-free steel are good choices for higher-volume runs when you need performance but a lower cost structure.
Summary of Common Types of Metal Choices for Molding
- For Prototyping and Low-Volume Production: Aluminum is the most cost-effective, offering excellent machinability and thermal conductivity. It’s commonly used for prototypes and low-volume production, especially in the automotive, electronics, and consumer goods sectors.
- For High-Precision and High-Temperature Applications: Tool steel (e.g., H13, D2) and stainless steel are the go-to choices. These materials are commonly used in aerospace, automotive, and medical device industries for high-precision, durable molds that withstand repeated use and high temperatures.
- For High-Wear and Stress-Resistant Molds: Nickel alloys (e.g., Inconel 718) and forged steel are often selected for molds that need to endure extreme wear, fatigue, and high temperatures, such as in the aerospace and power generation sectors.
- For High-Volume, Detailed Molds: Zinc alloys (e.g., Zamak) are widely used for mass-production molds that require a detailed finish, particularly in the automotive, consumer electronics, and household product industries.
10 Frequently Asked Questions About Types of Metal Selection
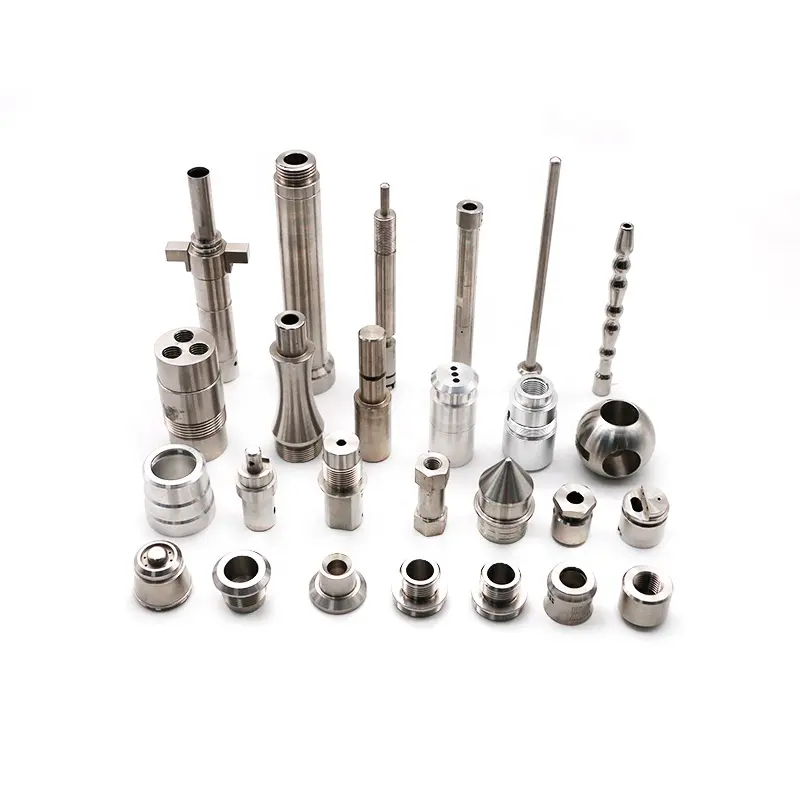
Q1: What are the metal materials you will be considering using for mold manufacturing?
- Evaluate the strength, corrosion resistance, machinability, heat resistance, and cost. The application demands metallurgy, where high-stress tooling will use metals such as tool steel or corrosion-resisting molds for stainless steel.
Q2: Is injection molding possible with aluminum?
- Aluminum is commonly used in injection molding as a lightweight, machinable, and moderate-temperature material.
Q3: Which metal is best for making molds for high temperatures?
- Due to their thermal resistance, excellent candidates for high-temperature molds include titanium, Inconel, and tungsten.
Q4: Is copper suitable for a mold?
- Yes, copper is also used in tooling, such as electrodes, where thermal conductivity is important, making it suitable for molds for electronics and precision parts.
Q5: For mass-production molds, what is the lowest-cost metal?
- Zinc and aluminum are the most economical metals commercially; they are used for many processes, including die-casting and injection molding.
Q6: Which is the BEST Material Used for High Precision Injection Mould?
- Tool steels, like H13 and D2, are considered the most suitable for high-precision molds because they are hard at high temperatures and wear-resistant.
Q7: What is the most economical metal for low-volume production molds?
- Aluminum is the cheap material of choice for low-volume production due to its cost but is also relatively easy to machine.
Q8: While brass is stronger than many materials, it should be avoided in high-stress applications.
- Brass does not lend itself well to high-stress applications. It is more suited for low-wear, decorative, and intricate molds than molds that undergo a high level of stress.
Q9: What would be the reason Zinc should be kept in high-volume molds?
- Therefore, Zinc is used in high-volume production molds due to its low melting point, good fluidity, and high detail reproduction, which allows for fast and cost-effective production cycles.
Q10: What material is suitable for aerospace molds?
- Nickel alloys (Inconel) and high-performance tool steels are great candidates for aerospace molds due to their high-temperature hardness, strength, and resistance to tremendous stress.
About BFY Mold
At BFY Mold, we provide high-quality injection molding and mold manufacturing services. Our factory offers mass production, on-demand production, CNC machining, and mirror spark services, ensuring precision and reliability for every project. Whether you need custom mold making or high-volume production, we’re equipped to deliver cost-effective, high-performance solutions for your manufacturing needs.