Product color difference is a common defect in injection molding, and it is not uncommon for injection molding machines to be scrapped in batches due to different colors of accessories. There are many factors affecting the color difference, touching the material resin, color masterbatch, color masterbatch mixing with the material, injection molding products, injection molding machines, molds, etc. Because it involves a wide range of areas, color difference control skills are also recognized as one of the more difficult skills in injection molding. Here is a detailed introduction for you.
Reduce Impact of Machines and Mold Components
To select an injection molding machine with the appropriate capacity for the main product of plastic mold processing, assume that the injection molding machine has material dead corners and other titles, and replace the equipment. For the mold casting system, exhaust tank, etc., the color difference can be dealt with by the repair die of the corresponding part of the mold. It is necessary to first deal with the injection molding machine and mold title to organize production to reduce the complexity of the title.

Injection Mold Processing
To eliminate the influence of material resin and color master control raw materials are the key to dealing with the color difference. Therefore, especially when producing light-colored products, the significant influence of different thermal stability of the material resin on the glorious shaking of the product can not be ignored. Since most injection molding manufacturers do not produce plastic or color masterbatches themselves, the focus of attention can be placed on production management and raw material inspection. That is to strengthen the inspection of raw materials in the warehouse. In the production of the same product as far as possible choose the same manufacturer, the same trademark masterbatch, and color masterbatch production.
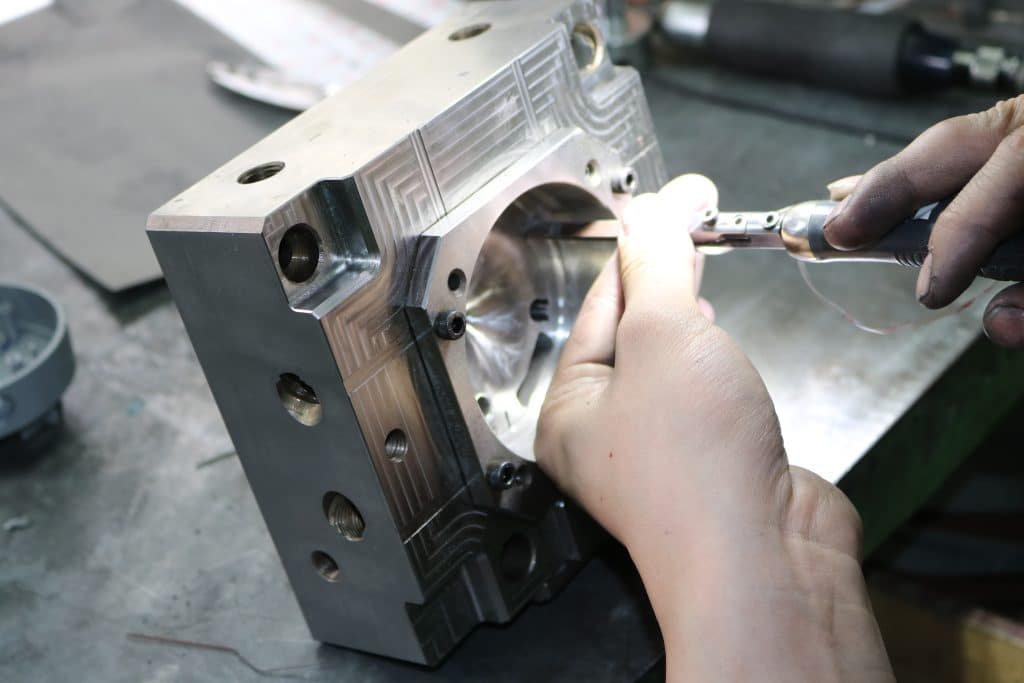
Conduct Color Test Before Mass Production
Both with the previous correction, but also in this comparison, assuming that the color difference is not large, can be qualified, as if the batch color master has a slight color difference, the color master can be mixed from the beginning and then used to reduce the color difference formed by the uneven mixing of the color master itself. In addition, it is necessary to check the thermal stability of the material resin and the color masterbatch. If the thermal stability is not secure, we advise the manufacturer to exchange it.
Minimize Cylinder Temperature Impact on Color Variation

In the production of plastic mold processing plants, it is often encountered that a heating ring is damaged or the heating control part is out of control for a long time to form a drastic change in the temperature of the barrel and then the color difference occurs.
The color difference caused by such reasons is easy to determine, and the color difference caused by the general heating ring damage and failure will be accompanied by uneven plasticization, and the heating control part is often accompanied by gas spots, severe discoloration and even coking. Therefore, it is necessary to check the heating part often in production and replace the heating part in time when it is damaged or out of control to reduce the probability of such color differences.