Customizing precision molds is essential for creating high-quality electronic products that meet specific performance and design requirements. In a rapidly evolving tech landscape, manufacturers must adapt their molding processes to accommodate the unique features of electronic components. By employing advanced techniques and materials, businesses can enhance mold precision and ensure optimal functionality.
Precision molds play a crucial role in the manufacturing of electronic products, ensuring that components are produced with high accuracy and consistency. This article will provide a detailed overview of how to customize precision molds for electronic products, focusing on the runner system, slider, mold layout, and water layout.
Understanding Precision Molds
Precision molds are used to create intricate and precise components, essential for the high standards required in the electronics industry. The customization of these molds involves several critical steps and components, each contributing to the overall quality and functionality of the final product.
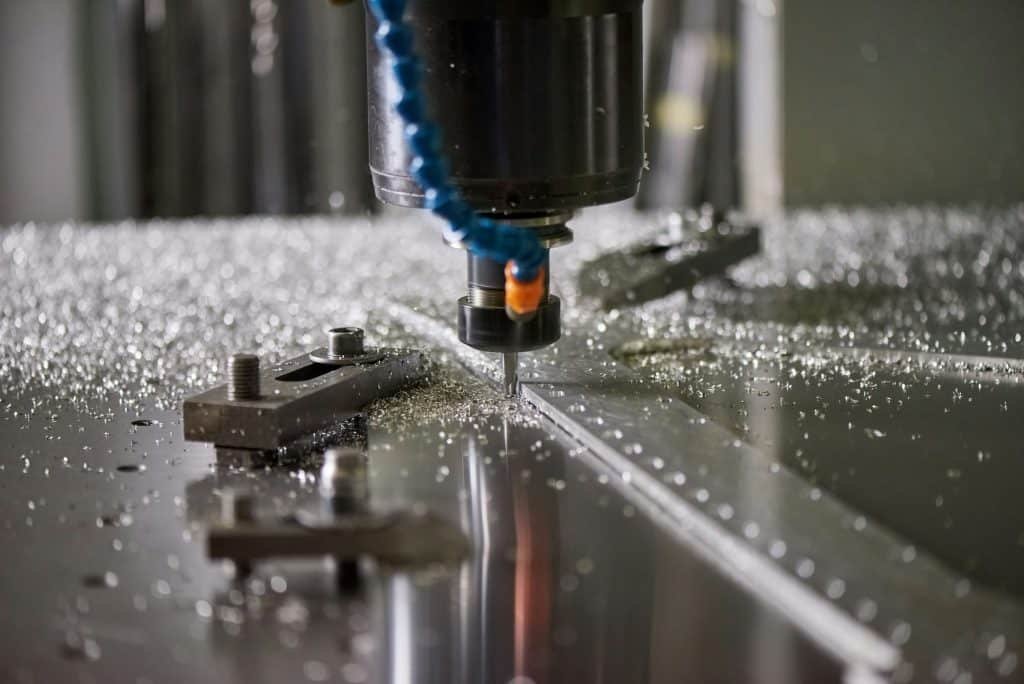
Runner System of Precision Molds
The runner system is the pathway through which molten plastic flows from the injection molding machine to the cavities in the mold. It is a vital part of the mold design that influences the quality and efficiency of the molding process.
Types of Runner Systems
- Cold Runner Systems: These systems have a simple design and are cost-effective. However, they generate waste material that needs to be trimmed and recycled, which can be a drawback for high-volume production.
- Hot Runner Systems: These systems maintain the plastic in a molten state within the runner, reducing waste and cycle times. They are more complex and expensive but offer better efficiency and quality control.

Designing the Runner System
When customizing the runner system for electronic products, consider the following:
- Flow Balance: Ensure that the plastic flows evenly to all cavities to prevent defects such as warping or short shots.
- Thermal Regulation: Maintain consistent temperatures to avoid issues like sink marks or inconsistent fills.
- Gate Location: Place gates strategically to minimize visible marks and ensure uniform filling.
Slider Mechanism
Sliders, also known as side actions, are used in molds to create undercuts or complex geometries that cannot be achieved with a straight-pull mold. They move perpendicular to the mold opening and closing direction, allowing for more intricate designs.
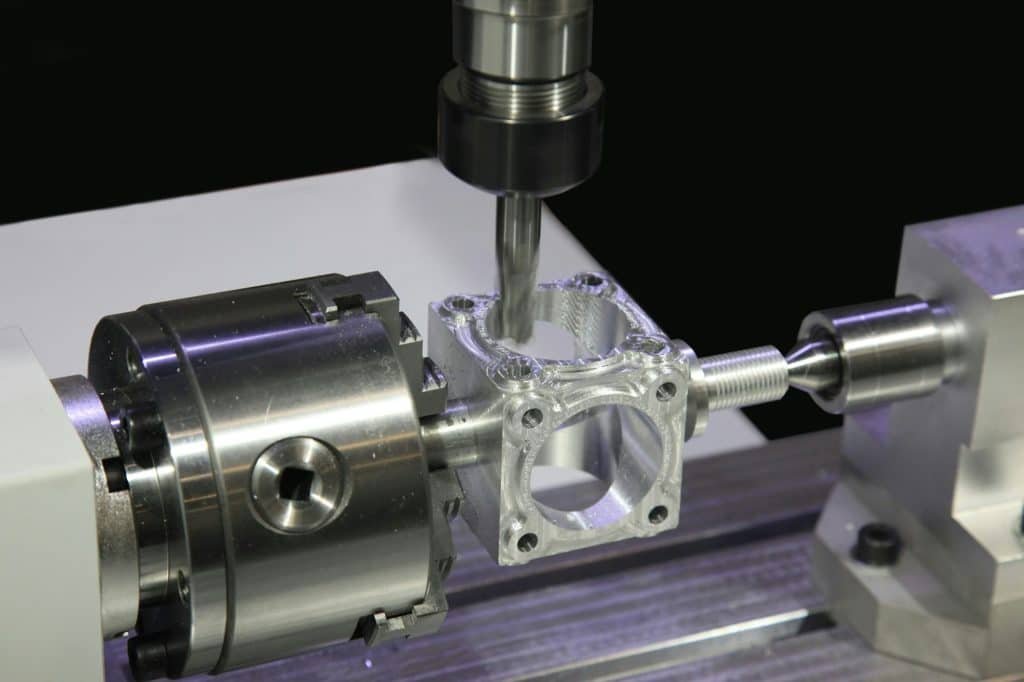
Designing Sliders
When incorporating sliders into your mold design:
- Material Selection: Use durable materials that can withstand repeated sliding motions without wear.
- Precision Engineering: Ensure that sliders move smoothly and align perfectly to avoid defects in the molded parts.
- Cooling Considerations: Integrate cooling channels to maintain the optimal temperature of the sliders, preventing overheating and deformation.
Mold Layout
The mold layout determines the arrangement of cavities, runner system, and other components within the mold. A well-designed layout optimizes space utilization, reduces material waste, and enhances production efficiency.
Key Considerations for Mold Layout
- Cavity Arrangement: Arrange cavities in a way that balances the mold, preventing uneven wear and tear.
- Runner Placement: Position runners to ensure even flow distribution and minimize material usage.
- Ejection System: Design the ejection system to remove parts without damaging them, considering the shape and size of the components.

Balancing and Venting
- Balancing: Balance the mold to ensure uniform pressure distribution during injection, reducing the risk of defects.
- Venting: Incorporate vents to allow trapped air to escape, preventing voids and surface blemishes.
Water Layout
The water layout, or cooling system, is critical for controlling the mold temperature during the injection process. Proper cooling ensures consistent quality and reduces cycle times.
Designing the Water Layout
- Cooling Channels: Design cooling channels to follow the contours of the mold, providing uniform cooling.
- Temperature Control: Use temperature control units to maintain precise cooling temperatures, preventing warping and shrinkage.
- Flow Rate: Optimize the flow rate of the cooling medium to ensure efficient heat removal.
Advanced Cooling Techniques
- Conformal Cooling: Utilize conformal cooling channels that match the shape of the mold cavity, providing more efficient and uniform cooling.
- Baffles and Bubblers: Use baffles and bubblers to enhance cooling in areas that are difficult to reach with standard channels.
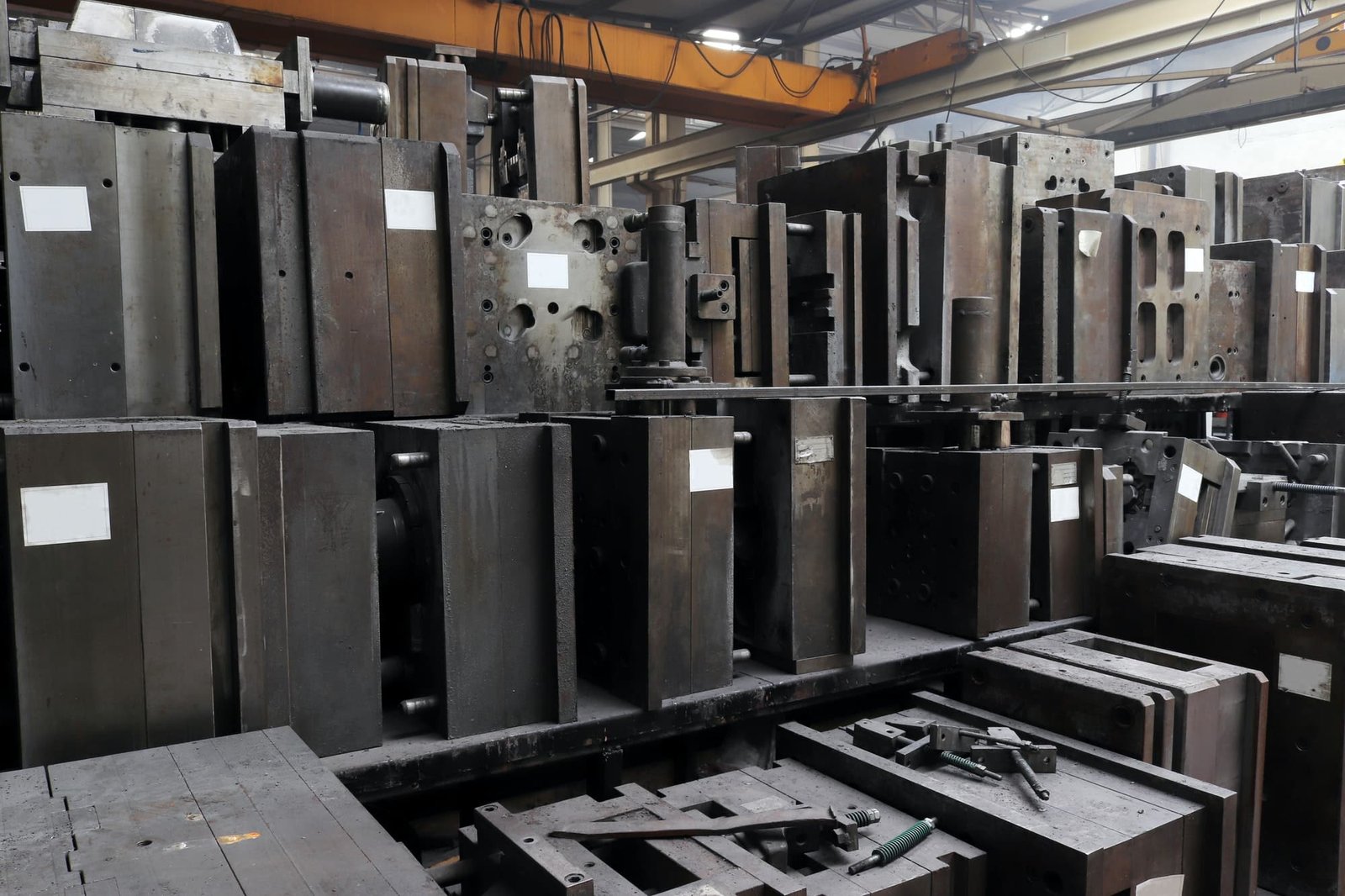
Precision Molds Manufacturer
Customizing precision molds for electronic products involves careful consideration of the runner system, slider mechanism, mold layout, and water layout. Each component plays a vital role in ensuring the quality and efficiency of the final product. At BFY Mold, we leverage our expertise in mold design and production to create precision molds that meet the stringent demands of the electronics industry. By focusing on these critical aspects, we can deliver high-quality, reliable components that drive innovation and performance in electronic devices.