Introduction
Injection molds are crucial in the manufacturing of plastic parts. Their structure typically consists of two main halves: the mold cavity and the mold core. The mold cavity is the outer part that forms the external shape of the product, while the mold core shapes the inner features. These halves come together to create a hollow space, replicating the final product.
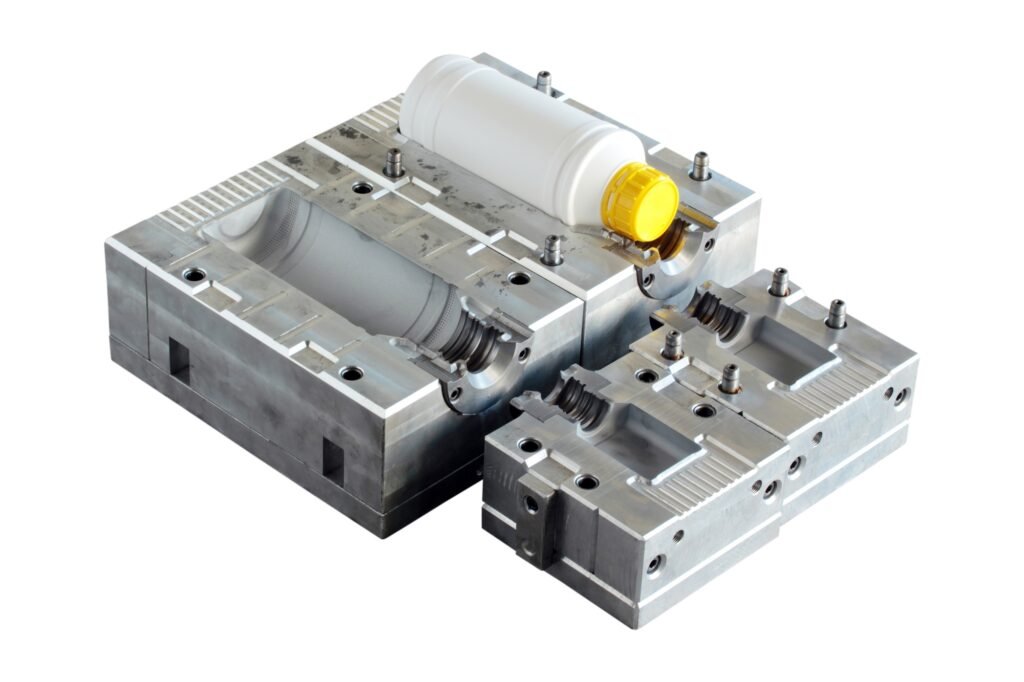
Key components include
Sprue: The entry point for molten plastic into the mold.
Runner System: Channels guiding the plastic from the sprue to the mold cavities.
Gate: The point where the molten plastic enters the mold cavity from the runner system.
Cavities: Hollow spaces within the mold where the final product takes shape.
Ejector Pins: Components that push the finished part out of the mold once it has solidified.
Cooling System: Channels and inserts for circulating coolant, ensuring proper cooling and solidification of the plastic.
Venting System: Allows air and gases to escape during the injection process.
Draft Angles: Tapered surfaces aiding in the ejection of the finished product.
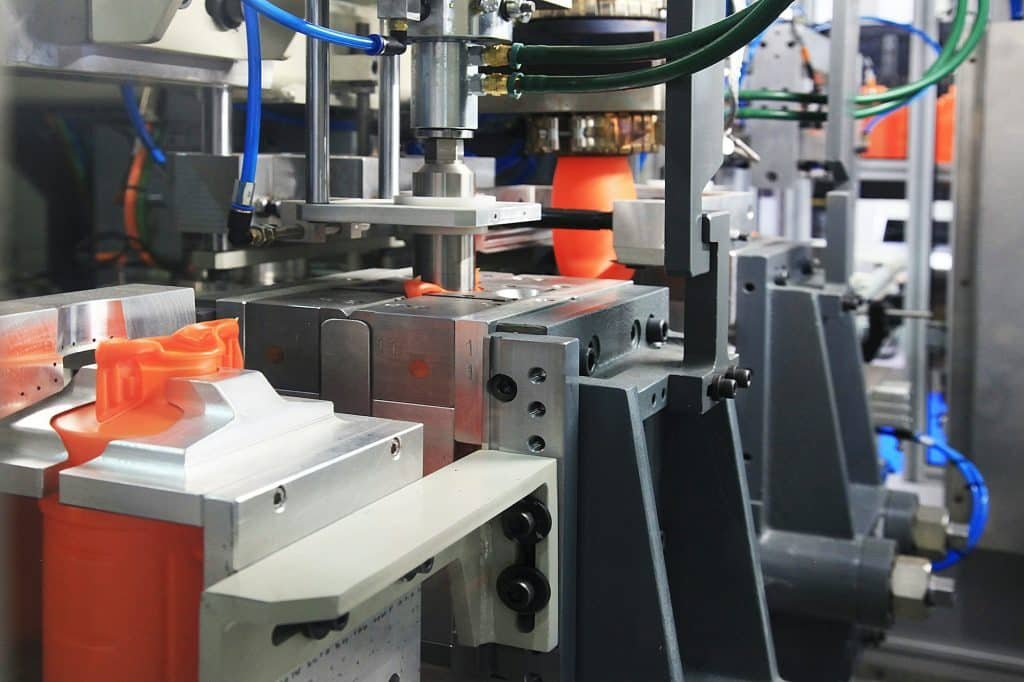
Materials like steel or aluminum are commonly used to make injection molds due to their durability and heat resistance. Molds are precision-engineered to ensure high-quality, repeatable production of plastic parts. Proper design and maintenance of injection molds are crucial for achieving consistent and defect-free manufacturing.
About BFY Mold
BFY Mold integrates product conception with product forming and mainly undertakes plastic mold product development and design, mold design and manufacturing, product injection molding, product surface treatment, and other services. With more than 20 years of production experience in mold design and mold manufacturing, the injection molding processing industry can create competitive molds for you. Let’s Start A New Project Today!