When considering the purchase of an injection mold, especially for mass production of plastic parts, it’s essential to understand the total cost involved. How much does an injection mold cost? For those looking to buy plastic injection molds from China, estimating the overall cost includes several components: mold design, materials, machining, surface treatment, sampling, shipping, and duties. Here is a breakdown of the key cost factors:
1. Mold Design Costs
Mold design typically accounts for about 10% of the total injection mold cost. For a simple part, Design for Manufacturability (DFM) can take 1-2 days, and 3D mold design may take 2-3 days. More complex molds can take weeks to design. The design phase is critical as it significantly impacts the overall cost and quality of the mold. Skilled designers can optimize costs while ensuring the mold meets all specifications.

Mold Design Cost
2. Material Costs
Materials represent 20-30% of the total injection mold cost and include several components:
Die Steel
For larger molds, the quality of the steel is crucial as it determines the mold’s durability and the number of cycles it can endure before needing repairs. It’s advisable not to compromise on steel quality despite the cost.
Mold Base
This typically uses lower-grade steel. However, the mold supplier must provide a cost-effective mold base with quick delivery and minimal processing errors.
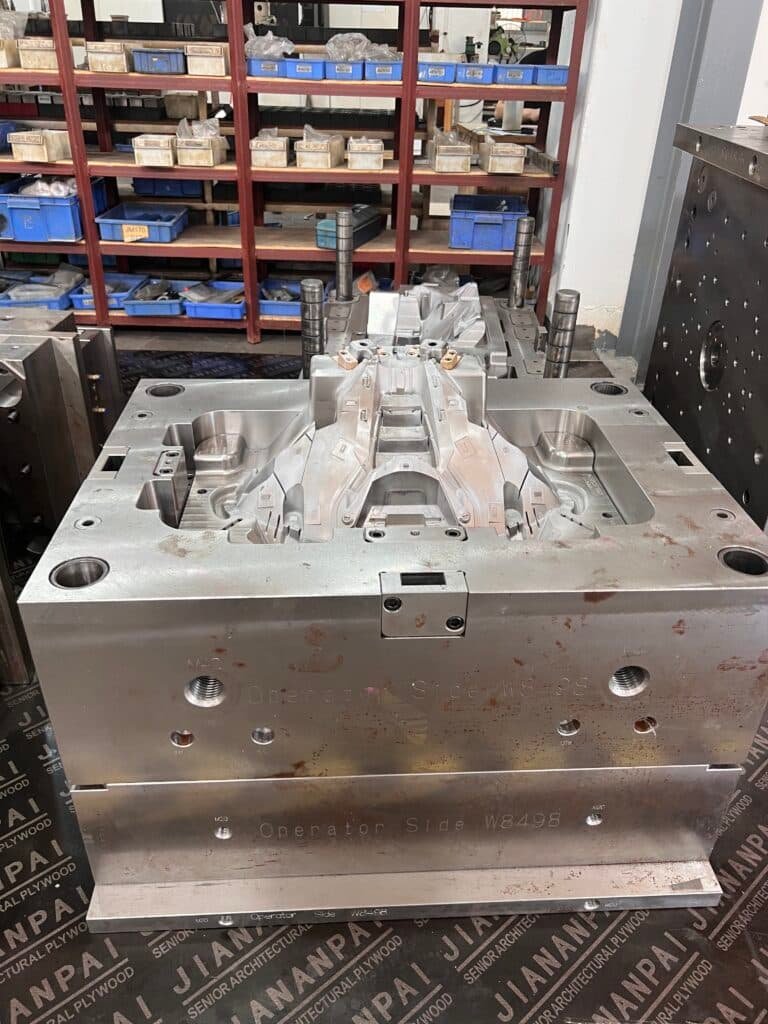
Mold Accessories and Assemblies
This includes components like ejector pins, locks, springs, cooling line connectors, cycle counters, and safety switches.
EDM Electrode
Depending on mold complexity, Electrical Discharge Machining (EDM) might be required, especially for molds with intricate details and deep grooves. The choice between graphite and copper electrodes affects both the cost and the mold quality.
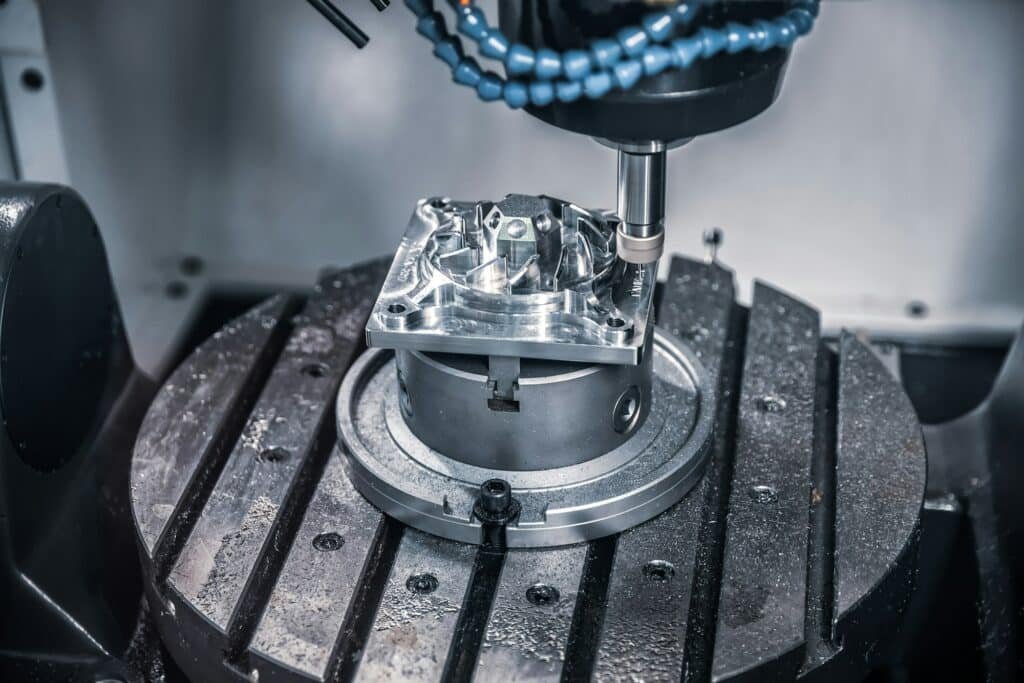
Plastic Resin
Mold validation often requires 2-3 rounds of sampling, which involves preparing the specified plastic resin in advance based on the part weight and sample size.
3. Processing Costs
Processing costs account for 20-30% of the total injection mold cost. Key processes include CNC machining, EDM, wire cutting, milling, grinding, and drilling. Maintaining high quality while controlling costs requires significant investment in advanced machinery and skilled labor, making this a major competitive factor for mold manufacturers.
4. Surface Treatment Costs
Standard surface treatments such as polishing to SPI-SPE B/C standards or EDM texturing are relatively inexpensive. However, specialized finishes like mirror polishing or unique textures can add significantly to the cost, depending on the specific requirements.

5. Sampling Costs
Sampling constitutes about 3-5% of the injection mold’s total cost. New molds typically require 2-3 rounds of proofing to ensure quality and fit. Effective mold manufacturers minimize sampling time and cost through superior design, processing, and assembly.
6. Freight Costs
If the mold is manufactured in one location and used in another, shipping costs must be considered:
Air Freight:
Costs range from $6-8 per kg. For shipments under 300 kg, express services are recommended; above 300 kg, air freight becomes more economical.
- Sea Freight: Starting at approximately $700, sea freight is suitable for bulk shipments.
- Rail Freight: Faster than sea freight but sometimes less reliable, with costs starting around $600.
- For shipping, it’s advisable to use a single shipping agent for door-to-door service to avoid complications and additional costs.

7. Duties and Taxes
Customs duties and taxes vary by region and can impact the overall cost. It’s recommended to consult with a local shipping agent for specific advice on applicable taxes and duties.
By understanding these cost components, you can make informed decisions when purchasing injection molds, especially when sourcing from different regions like China.
Conclusion
The injection mold cost can vary significantly based on several factors, including the complexity of the mold design, the type of material used to make the mold, the number of cavities, and the required production volume. Here’s a detailed breakdown of the factors affecting the injection mold cost:
Injection Mold Cost Factor | Details | Estimated Cost Range |
Mold Type | – Prototype Mold: Typically made from aluminum or soft steel for low-volume production or testing. | $1,000 to $5,000 |
– Production Mold: Made from hardened steel for high-volume production and longevity. | $5,000 to $100,000+ | |
Material Used for Mold | – Aluminum: Lower cost, suitable for low-volume or prototype molds. | $1,000 to $10,000 |
– Steel (P20, H13, etc.): Higher cost, suitable for high-volume and durable molds. | $5,000 to $100,000+ | |
Number of Cavities | – Single Cavity Mold: Produces one part per cycle; lower cost but higher per-part cost. | $5,000 to $25,000 |
– Multi-Cavity Mold: Produces multiple parts per cycle; higher initial cost but lower per-part cost. | $20,000 to $100,000+ | |
Complexity of Design | – Simple designs with basic geometries (e.g., flat or non-complex shapes). | $5,000 to $15,000 |
– Complex designs with intricate details, undercuts, threads, or tight tolerances. | $20,000 to $100,000+ | |
Size of the Mold | – Small molds (e.g., for small plastic parts). | $3,000 to $20,000 |
– Large molds (e.g., for automotive or large consumer goods). | $50,000 to $200,000+ | |
Mold Features | – Standard features (simple ejectors, basic cooling channels). | Included in base cost |
– Advanced features (complex ejector systems, hot runners, conformal cooling). | $10,000 to $50,000+ | |
Tooling and Machining Requirements | – Basic tooling with standard machining processes (milling, drilling). | $5,000 to $20,000 |
– Advanced tooling with precision machining, EDM, and additional treatments (polishing, texturing). | $20,000 to $50,000+ | |
Mold Longevity Requirements | – Short-run molds designed for lower volumes (less durable). | $1,000 to $10,000 |
– Long-run molds designed for high volumes (more durable, longer lifespan). | $20,000 to $100,000+ | |
Location of Manufacturing | – Molds made in regions with lower labor and production costs (e.g., Asia). | 30% to 50% less than Western countries |
– Molds made in regions with higher labor and production costs (e.g., North America, Europe). | Higher than in lower-cost regions |
Summary of Injection Mold Costs
- Simple Prototype Mold: $1,000 to $5,000
- Small, Low-Complexity Production Mold: $5,000 to $20,000
- Medium to High-Complexity Production Mold: $20,000 to $100,000+
- Large, Complex Mold for High-Volume Production: $50,000 to $200,000+
The exact cost of an injection mold depends heavily on the specific requirements of the project, including the material, size, complexity, and volume of production. For an accurate quote, it is recommended to consult with a professional mold-making company or service provider.
About BFY Mold’s Injection Mold Services
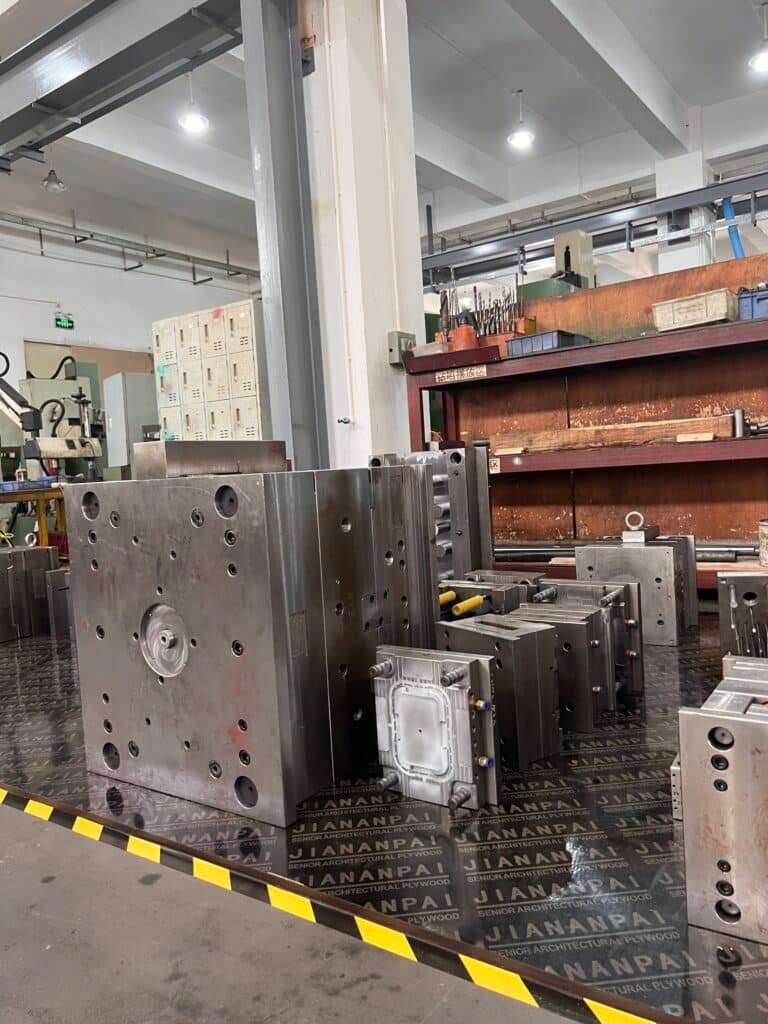
At BFY Mold, we specialize in providing high-quality injection molding and mold manufacturing services tailored to meet diverse industry needs. With our advanced technology and skilled team, we ensure precision and efficiency in every project, from mass production to on-demand manufacturing. Our comprehensive services also include CNC machining and mirror sparking, supported by our state-of-the-art facility. Contact us to learn more about how we can support your next project.