Quality control in injection molding is a critical aspect of the manufacturing process that directly impacts product quality and customer satisfaction. By implementing effective quality control measures, manufacturers can identify defects early, ensuring that only the highest-quality products reach the market.
In the competitive world of manufacturing, quality control is more than just a process—it’s a commitment to excellence. At BFY Mold, we understand that ensuring the highest quality in injection molded parts is essential for maintaining customer satisfaction and trust. This blog post will take you through the comprehensive quality control measures we employ, from material selection and mold design to inspection and testing techniques, ensuring that each part we produce meets the highest standards.
Quality Control Measures in Injection Molding
Material Selection and Preparation
Quality starts with the right materials. Using high-quality resins and additives is the foundation of producing durable and reliable parts. At BFY Mold, we work only with certified suppliers who provide materials that meet stringent specifications. Before production begins, we conduct rigorous testing to check for consistency, including melt flow index and moisture content analysis.
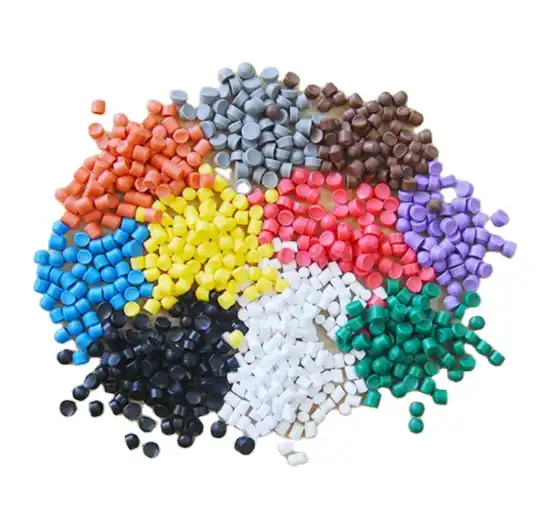
- Supplier Certification: Ensuring our suppliers are reliable and consistent in their quality.
- Material Testing: Performing tests to confirm the material properties meet our standards.
Mold Design and Maintenance
The design and maintenance of molds are crucial for producing parts with high precision and minimal defects. Our team of engineers at BFY Mold employs advanced design software to create molds that ensure uniform material flow and prevent common issues like warping and shrinkage. Regular maintenance schedules are followed to inspect and repair molds, extending their lifespan and maintaining production quality.
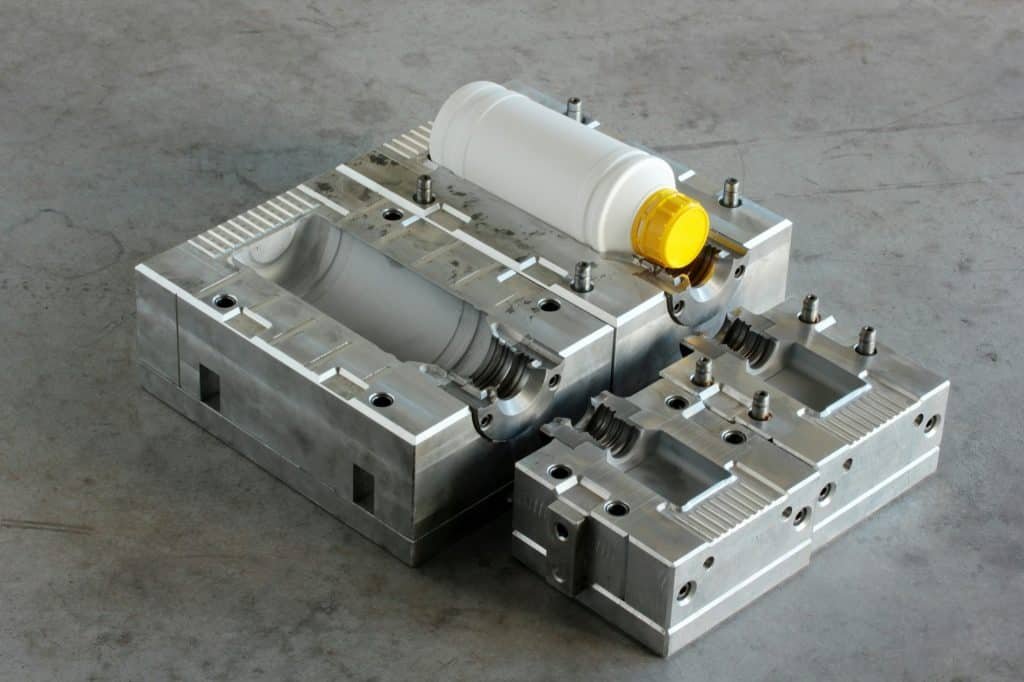
- Precision Engineering: Crafting molds with exact specifications.
- Routine Maintenance: Regularly inspecting and maintaining molds to ensure optimal performance.
Process Control
Controlling the injection molding process is key to producing consistent, high-quality parts. We use state-of-the-art monitoring systems to monitor critical parameters such as temperature, pressure, and cooling time. Adjustments are made in real time to maintain optimal conditions throughout the production cycle.
- Process Monitoring: Utilizing advanced software and sensors for real-time adjustments.
- Standard Operating Procedures (SOPs): Following SOPs to ensure consistency and reliability in production.
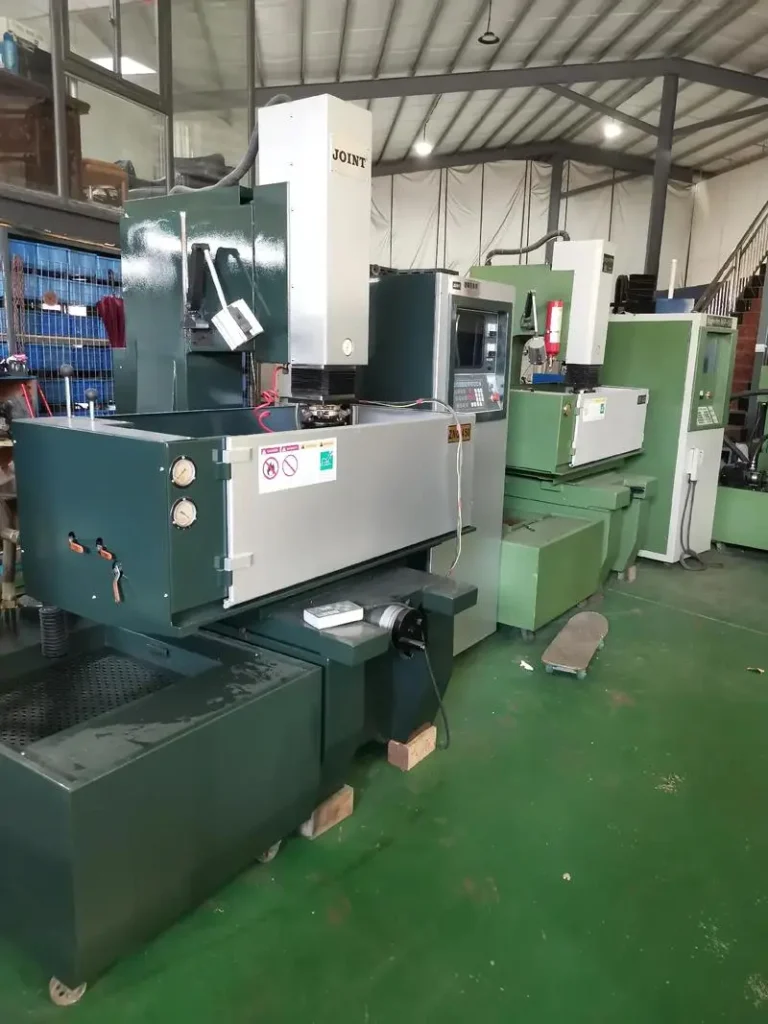
Inspection Techniques
Visual Inspection
Visual inspection is the first step in our quality control process. This involves a thorough examination of parts for surface defects like scratches, burn marks, and discoloration. Our trained inspectors use magnifying tools to catch even the smallest imperfections.
- Manual Inspection: Experienced inspectors examine each part closely.
- Automated Systems: Implementing machine vision systems for consistent and accurate inspections.
Dimensional Inspection
Dimensional accuracy is critical, especially for parts that must fit together precisely. We employ advanced tools like Coordinate Measuring Machines (CMMs) to measure parts with high precision, ensuring they meet the specified dimensions and tolerances.
- Coordinate Measuring Machines (CMM): High-precision measurement of part dimensions.
- Calipers and Micrometers: Quick and accurate measurement tools for dimensional checks.
Testing Techniques
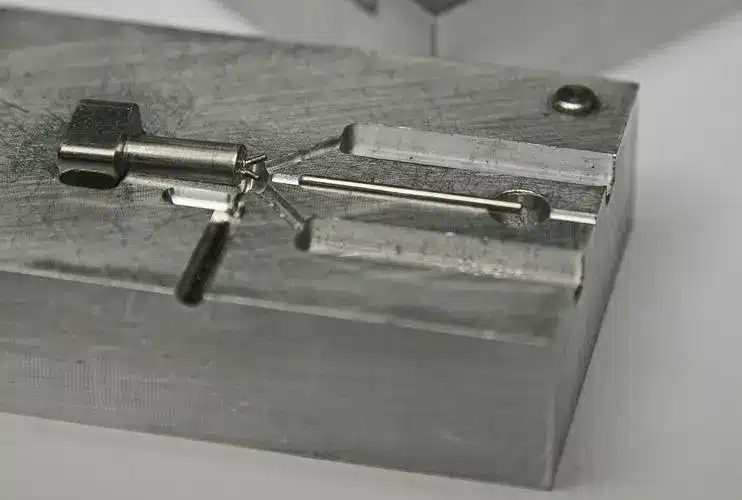
Mechanical Testing
To ensure our parts can withstand their applications’ demands, we conduct various mechanical tests. These include tensile testing to measure how much force a part can handle before breaking, impact testing to assess resistance to sudden forces, and hardness testing to determine surface resistance to indentation.
- Tensile Testing: Measuring the part’s strength under pulling forces.
- Impact Testing: Evaluating resistance to sudden impacts.
- Hardness Testing: Assessing surface resistance to wear and indentation.
Environmental Testing
Parts often need to perform well under various environmental conditions. We expose parts to extreme temperatures, humidity, and UV light to test their durability and reliability in different environments.
- Thermal Cycling: Testing parts under extreme temperature changes.
- Humidity Testing: Assessing resistance to moisture and potential corrosion.
- UV Testing: Ensuring parts can withstand exposure to UV light without degrading.
Functional Testing
Functional testing is essential to confirm that parts perform their intended functions reliably. This includes testing parts within their assemblies, conducting life cycle tests to simulate real-world use, and stress testing to ensure parts can handle extreme conditions.

- Assembly Testing: Verifying correct fit and function within assemblies.
- Life Cycle Testing: Simulating long-term use to test durability.
- Stress Testing: Applying high forces to test performance under extreme conditions.
Continuous Improvement
Quality control is an ongoing process at BFY Mold. We continuously review and update our quality control procedures to enhance efficiency and effectiveness. This includes gathering feedback from production teams and customers, implementing training programs, and adopting lean manufacturing principles to reduce waste and improve quality.
- Feedback Loops: Analyzing feedback to identify areas for improvement.
- Training Programs: Keeping our team updated on the latest quality control techniques.
- Lean Manufacturing: Reducing waste and improving overall efficiency.
Conclusion
At BFY Mold, quality control is at the heart of everything we do. From selecting the best materials and designing precise molds to implementing rigorous inspection and testing techniques, we are dedicated to producing the highest quality injection molded parts. Our commitment to continuous improvement ensures that we not only meet but exceed industry standards, providing our customers with reliable and superior products.
For more information about our quality control measures and how we can support your manufacturing needs, please visit our website or contact us directly.

About BFY Mold
BFY Mold is a leading provider of injection molding and mold manufacturing services. With our factory and a team of skilled professionals, we offer a range of services including mass production, on-demand production, CNC machining, and mirror spark. Our commitment to quality and customer satisfaction ensures that we deliver exceptional products that meet the highest standards. Contact us today to learn how we can support your manufacturing needs.