1. Access to CAD Drawings or Samples
The data must be correct for an injection molding quote, which means they need either CAD drawings or physical copies of the part. Mold manufacturers rely on CAD (Computer-Aided Design) drawings to grasp your part’s specifications, including the required dimensions, tolerances, and other design features. While CAD drawings can be a great reference point, CAD files are better for accuracy and as a guide to make the injection process easier.

Why is it important for injection molding quotes?
- Pricing Accuracy: Providing CAD drawings means the manufacturer knows the complete geometry of your part, which aids in providing an accurate injection molding quote.
- Quicker Prototyping: Prototyping can happen faster with CAD files, as the modernized model can be used to simulate or design the mold.
- Flexibility: CAD files can easily be adjusted or modified based on design improvements or manufacturing needs.
If you don’t have CAD drawings, be ready to submit detailed physical samples, sketches, or photos that demonstrate the part’s shape, size, and intended function.

2. End Use and Environmental Considerations
Knowing how your part will be used at the end of its lifecycle is critical to material selection, design features, and even quality control procedures. You need to know how your part will be used and what environmental conditions it will encounter.
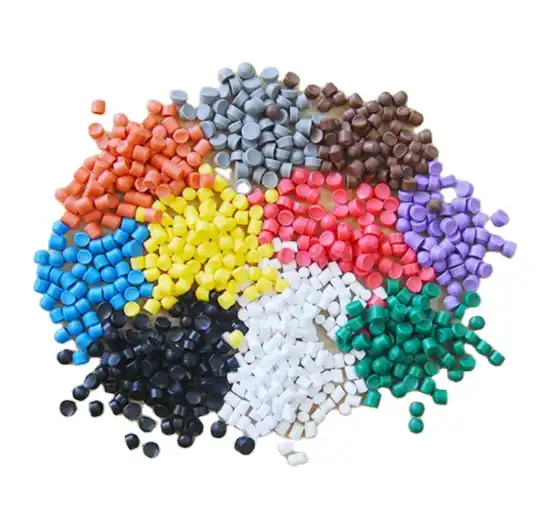
Questions to Consider:
- Is your part going to be subjected to high temperatures or chemicals?
- Is it going to be outdoors or in a high-stress environment?
- Does it represent a regulated part (medical, automotive, etc.)?
Examples of Environmental Factors:
Environmental Factor | Example of Impact |
High Temperature | Parts for automotive engines may need heat-resistant materials |
Chemical Exposure | Medical equipment may require materials resistant to certain chemicals |
UV Exposure | Outdoor parts may need UV-resistant materials to avoid degradation |
Manufacturers with a deep understanding of the end use and environmental considerations can recommend the right material and processes. This ensures the part performs as expected and lasts through its lifecycle, leading to a more accurate injection molding quote.
3. Quantity Requirements
One primary way we measure the cost and time associated with your injection molding project is the number of parts you require. Although injection molding is fantastic for mass production, the tooling and setup costs can vary significantly depending on the quantity of your part order.
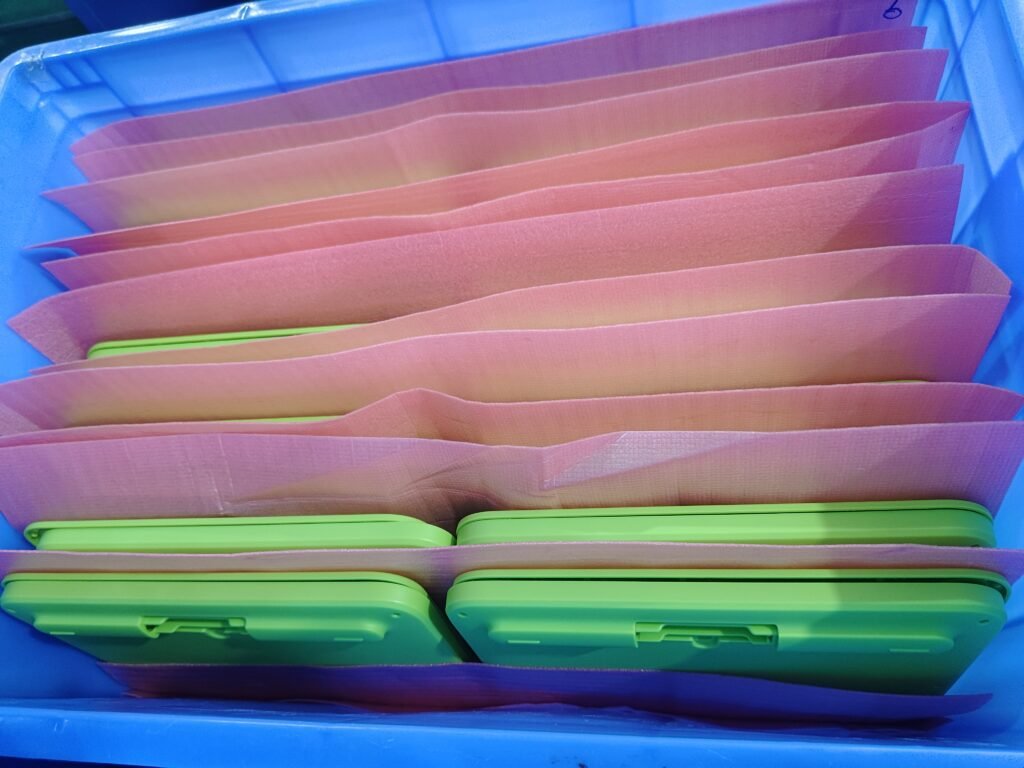
Small Batch Production vs. High Volume Production:
- Small Batch Production: A manufacturer may propose methods such as on-demand production or low-volume tooling to lower startup costs with prototypes or limited production runs.
- High-Volume Production: Large-scale manufacturing with custom molds and full-scale injection molding processes can be more economical, decreasing cost-per-unit as quantities increase.
If you don’t know your exact number, you can give a range (e.g., 500–1000 units) to help manufacturers give an accurate injection molding quote.
4. Injection Molding Part Size and Complexity
The injection molding quote depends on the size and complexity of your part. Injection molding allows for rapid manufacturing of parts with complex shapes or fine details; however, the larger and more complicated the design, the greater the associated cost and time needed.
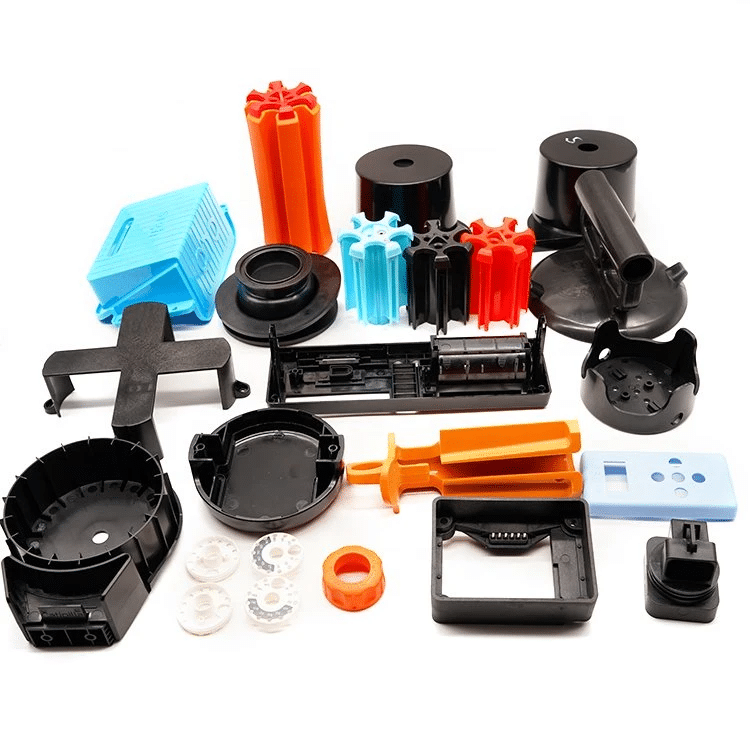
Key Factors:
- Mold Handling: How hard is getting the mold to and from storage? On the other hand, down-scales may necessitate calibrated equipment and specifications, affecting price.
- Part Complexity: Parts characterized by complex geometries, including undercuts, thin walls, or molds with multiple components, usually require sophisticated tooling and extended cycle times.
To conceptualize the link between part complexity and cost, below is a comparison between a simple and complex part:
Feature | Simple Part | Complex Part |
Mold Complexity | Low (fewer cores and cavities) | High (multiple cores, inserts, etc.) |
Cycle Time | Shorter | Longer (due to intricate details) |
Tooling Cost | Lower | Higher (advanced machining required) |
Unit Cost (high volume) | Lower | Higher (due to complexity and time) |
Thus, being aware of the size and complexity of your part will allow you to make an informed decision regarding design and manufacturing approaches.
5. Material Selection
The material or resin is one of the most important aspects of your injection-molded part, as it influences performance, durability, and cost. Some materials have the attributes to withstand strength, flexibility, or resistance to certain chemicals or temperature extremes.
Common Injection Molding Material Types:
- Thermoplastics (ABS, polypropylene, and polyethylene, for example): These are the most commonly used materials in injection molding because they are versatile, cost-effective, and can be reheated and recycled.
- Thermosetting Plastics (epoxy, phenolic, etc.): These materials are set upon molding and are best for components requiring high temperature or extreme environmental stability.
- Thermoset elastomers (for example, silicone): Used as flexible elements, such as gaskets or seals, that need stretchability and resilience.
Material vs. Performance:
Material Type | Characteristics | Ideal Use |
ABS | Durable, impact-resistant, easy to machine | Consumer electronics, automotive parts |
Polypropylene | Flexible, chemical-resistant | Packaging, medical parts |
Silicone | High flexibility, heat resistance | Seals, gaskets, automotive applications |
Selecting the appropriate material involves knowing the mechanical properties required for the part and the environmental conditions that could impact material behavior.
6. Conclusion and Company Overview
Injection molding is a complex process. Understanding these key factors will help you receive a more precise injection molding quote and ensure a better manufacturing experience. No DFM analysis, no DFM process can take the place of clear communication and information sharing; by giving your manufacturer a thorough overview of the part design, the intended use, number required, size, complexity, material to be used, etc., you limit the chances of a sub-par product, a delay, or an unsustainable cost.

BFY Mold is engaged in injection molding and mold making, with specialties such as mass production, on-demand production, CNC machining, and mirror sparking. With our fully equipped factory and trained staff, we can ensure precision and quality at every step of the manufacturing process. We offer budget-friendly services for all of your molding and manufacturing needs.
If you’re looking for a reliable partner for your injection molding needs, we offer free drawing optimization services to enhance your design and ensure cost efficiency. Additionally, we provide discounts on molds, making it easier to get the best value for your investment.
Contact us today for a precise injection molding quote, starting your project from start to finish.