In the intricate world of injection molding, where precision is paramount, the emergence of defects can be a stumbling block to achieving flawless end products. The process, although highly efficient, is not immune to challenges that may arise during manufacturing. Here are the common pitfalls of injection molding and explore proactive strategies to prevent defects, ensuring a seamless production process and impeccable final results.
I. The Precision Puzzle of Injection Molding:
Injection molding is a precision-driven process where molten material is injected into a mold cavity to produce intricate and detailed components. The success of this method lies in its ability to reproduce complex geometries with high accuracy and efficiency. However, like any manufacturing process, injection molding is susceptible to defects that can compromise the quality of the final product.
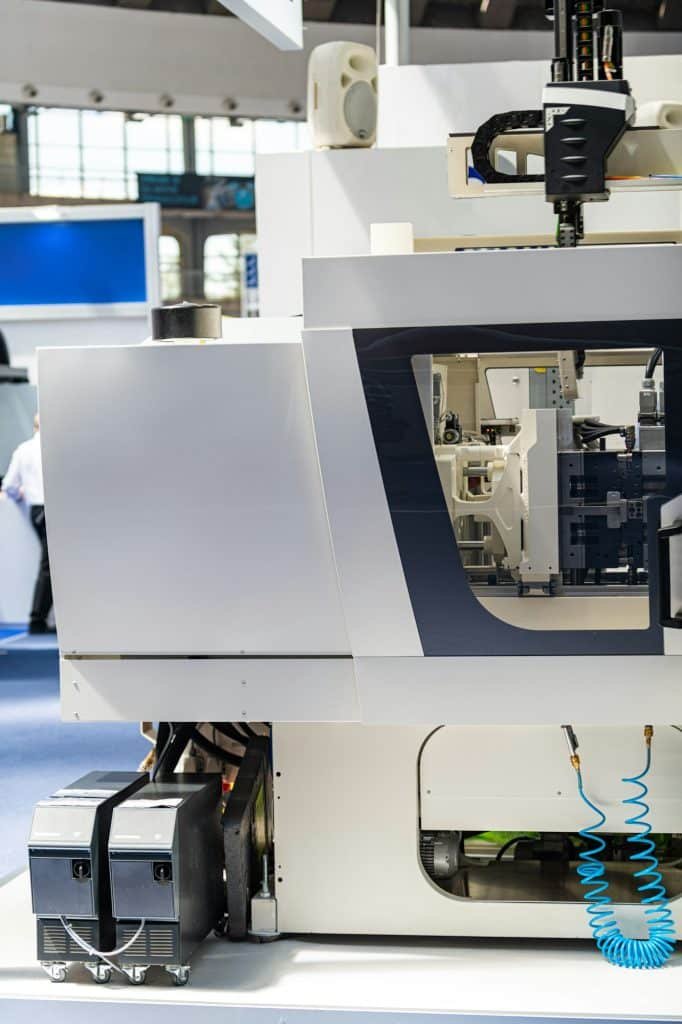
II. Common Injection Molding Defects:
Flash
Flash occurs when excess material escapes the mold, leaving a thin layer of excess material around the edges of the final product. This defect can result from issues such as excessive injection pressure or poorly designed molds.
Sink Marks
Sink marks manifest as depressions on the surface of the molded part, usually caused by uneven cooling or insufficient packing of the material within the mold.
Weld Lines
Weld lines occur when two flow fronts meet and solidify, creating a visible line on the surface of the part. This defect is common in complex geometries or when using materials with poor flow characteristics.
Short Shots
Short shots happen when the mold does not fill with material, resulting in incomplete parts. Causes include inadequate injection pressure, improper material temperature, or insufficient gate size.
Warpage
Warpage refers to the distortion of the final product due to uneven cooling or improper ejection from the mold. It can lead to dimensional inaccuracies and compromise the functionality of the part.
III. Preventive Strategies for Injection Molding Defects:
Meticulous Mold Design
The foundation of defect prevention lies in meticulous mold design. Ensuring that the mold is designed with precision, proper venting, and appropriate cooling channels can significantly reduce the risk of defects.
Optimized Processing Parameters
Fine-tuning processing parameters, including injection speed, temperature, and pressure, is crucial for preventing defects. Regular monitoring and adjustment of these parameters during production help maintain optimal conditions.
Material Selection and Preparation
Choosing the right material for the application and ensuring proper material preparation are essential steps in defect prevention. Material inconsistencies can lead to defects such as discoloration, degradation, or poor flow characteristics.
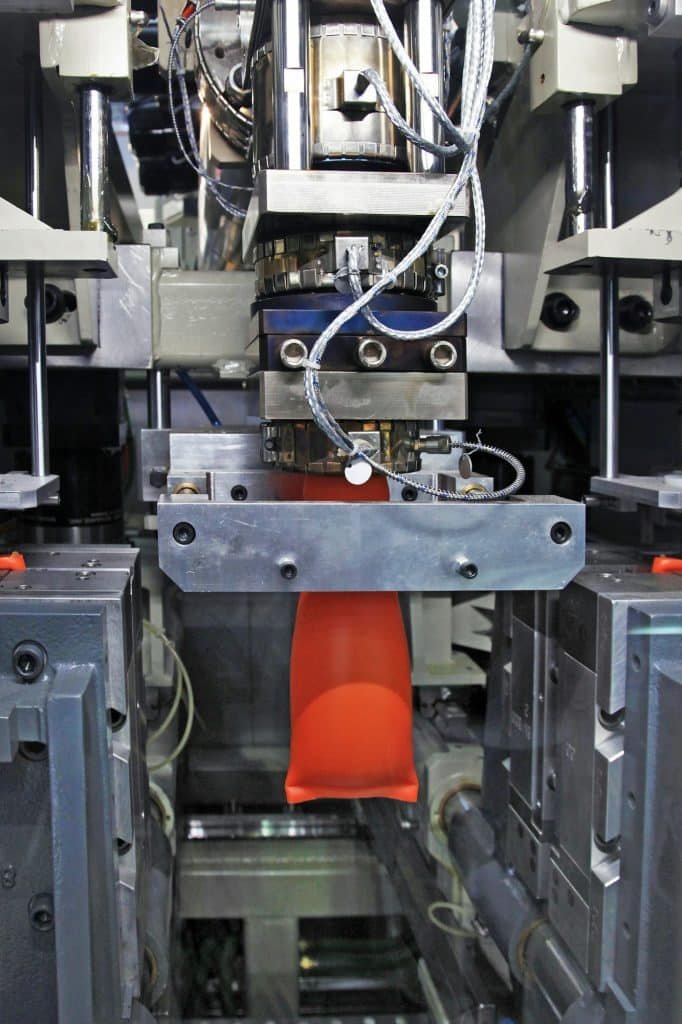
Gate Design and Placement
The design and placement of gates, the points through which material enters the mold, play a critical role in preventing defects. Proper gate design and placement help ensure uniform filling of the mold cavity, minimizing the risk of short shots and weld lines.
Quality Control and Inspection
Implementing rigorous quality control measures and regular inspections throughout the production process can help identify and rectify potential defects early on. Real-time monitoring systems can aid in maintaining consistency and reducing the likelihood of defects.
What is the Injection Molding Process?
Regular maintenance of injection molding machines and molds is paramount. Addressing wear and tear, replacing damaged components, and ensuring the overall integrity of the equipment contribute to defect-free production.
Conclusion:
Injection molding, with its precision and efficiency, stands as a cornerstone in modern manufacturing. However, the journey from molten material to the finished product is not without challenges. Understanding common defects and implementing proactive prevention strategies is imperative for manufacturers seeking excellence in their production processes. By embracing meticulous design, optimized processing parameters, and a commitment to quality, manufacturers can navigate the intricate landscape of injection molding, ensuring a seamless path toward flawless and high-quality end products. In the dynamic realm of manufacturing, where precision is non-negotiable, the proactive prevention of defects becomes the key to unlocking the full potential of injection molding.