In the world of plastic manufacturing, Injection molding and blow molding are essential techniques that have transformed the production of numerous plastic products.
These methods play pivotal roles in shaping everyday items, from intricate components in electronics to common household containers. Each technique boasts its own unique set of advantages, catering to diverse industrial needs and product specifications.
Injection Molding: Precision in Complexity
Injection molding, a stalwart in plastic manufacturing, is renowned for its precision and versatility. The process injects molten plastic into a mold, where it cools and solidifies to shape. It’s prized for precision in making intricate parts, which is crucial in industries needing complex designs and tight tolerances.
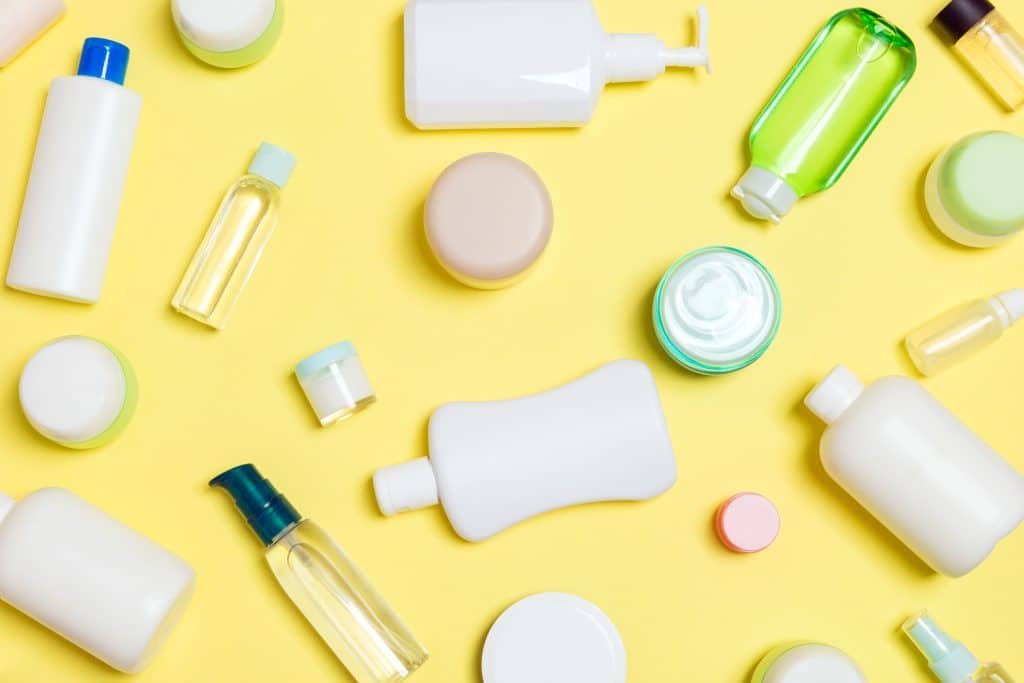
One of the standout advantages of injection molding lies in its ability to accommodate a diverse range of materials. This method accommodates thermoplastics, thermosetting polymers, and elastomers, offering manufacturers flexibility to select materials tailored to their product’s specific properties. The process also facilitates the incorporation of additives and reinforcements, enhancing the structural and functional attributes of the final product.
Additionally, injection molding excels in scalability, enabling consistent quality mass production. The process’s efficiency and speed make it perfect for high-volume manufacturing, cutting production costs and ensuring consistency across large batches. Industries like automotive, medical, and consumer goods regularly use injection molding to produce intricate components and products with precise specifications.
Blow Molding: Forming Hollow Vessels with Efficiency
Blow molding shines when making hollow items like containers and bottles. Here, a heated plastic tube is inflated within a mold, taking shape as it cools. Blow molding’s hallmark advantage lies in its efficiency in producing lightweight, durable, and cost-effective hollow products.
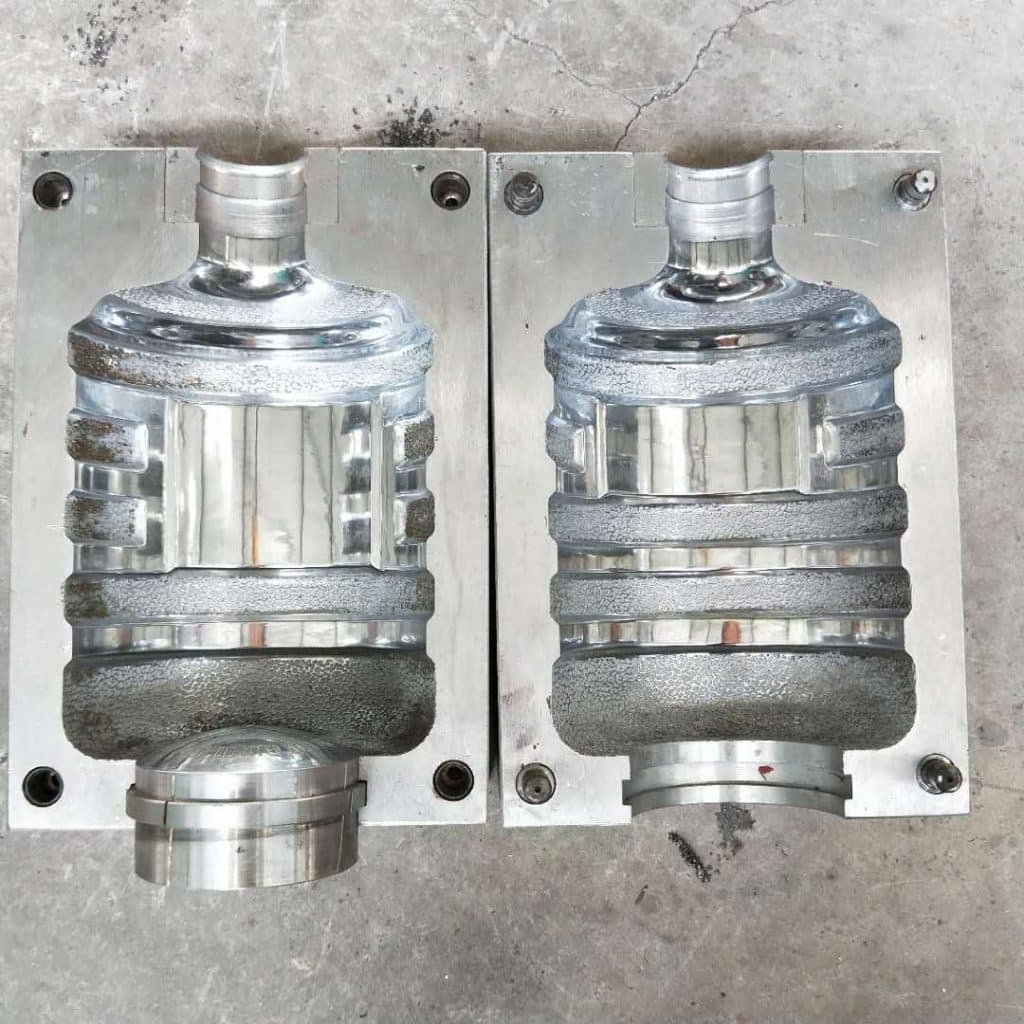
The clear benefit of blow molding is seen in a smooth, hollow, seamless product. It is the preferred method for industries where the majority of products are containers, bottles, and packaging. The process stands out with uniform wall thickness and the flexibility to manufacture containers with different shapes and sizes suitable for different needs of the packaging industry.
Blow molding also scores high on resource efficiency. The technique optimizes material usage by focusing on creating hollow structures, reducing the product’s overall weight without compromising strength. This lightweight characteristic contributes to cost savings and aligns with the growing emphasis on sustainability and eco-friendly practices in modern manufacturing.
Contrasting Strengths: Finding the Right Fit
Injection molding and blow molding have their pros and cons, but they are heavily dependent on the end product required. Injection molding is ideal when you need small parts with lots of detail and high accuracy; for example, in the electronics, automotive, and medical devices industries. Its versatility in materials and its capability of large-scale production solidify its dominance in these fields.
On the other hand, blow molding is specifically great when it comes to hollow structures (in fact, there would be no packaging industry without blow molding). Blow molding is a highly efficient method for creating lightweight containers with consistent wall thickness, which addresses the demands of various industries such as beverages, cosmetics, and pharmaceuticals. Its resource-efficient methodology reduces material consumption while promoting sustainable objectives for contemporary manufacturing practices.
Striking a Balance in Plastic Manufacturing
Injection molding and blow molding are both essential to the ever-evolving world of plastic manufacturing. Both methods, injection molding and blow molding, stand as leaders in plastic manufacturing, each crafted to serve specific purposes, fill particular needs, and extract higher profitability and reliability.
From the automotive sector to medical devices, the plastic products of tomorrow will rely on the unique advantages of these processes, with injection molding and blow molding working together in harmony to meet the evolving needs of various industries.