Acrylonitrile Butadiene Styrene (ABS) is a cornerstone of modern manufacturing, renowned for its unmatched balance of strength, durability, and processability. Since its commercialization in the 1950s, ABS has revolutionized industries from automotive to consumer electronics, offering a lightweight yet robust alternative to metals and other plastics. This article provides a comprehensive analysis of ABS plastic, supported by comparative graphs and regulatory insights, to address critical questions about its safety, environmental impact, and applications in the U.S. market.
1. What Is ABS Plastic?
ABS is a thermoplastic polymer that is made from three monomers:
- Acrylonitrile (15–35%): Improves chemical/thermal stability.
- Butadiene (5–30%): A rubbery phase for impact strength
- Styrene (40–60%): Provides rigidity and glossy finish.
Additionally, ABS’s construction allows for an excellent surface finish and wear resistance, ensuring that products are not just durable but look great, too. This balance of its molecules allows it to be subjected to extreme processing techniques, including injection molding and extrusion, with little loss of properties.

Key Properties:
Property | Value Range | Application Relevance |
Tensile Strength | 29–45 MPa | Structural components |
Impact Resistance | 200–400 J/m | Automotive bumpers, toys |
Melting Point | 105–125°C | Heat-resistant housings |
Density | 1.04–1.06 g/cm³ | Lightweight consumer goods |
2. The Manufacturing Process of ABS
ABS production involves emulsion polymerization:
- Monomer Mixing: Acrylonitrile, butadiene, and styrene are combined.
- Reaction: Polymerized at 50–150°C with initiators (e.g., peroxides).
- Compounding: Additives (UV stabilizers, flame retardants) are blended.
- Pelletizing: Extruded and cut into feedstock pellets.
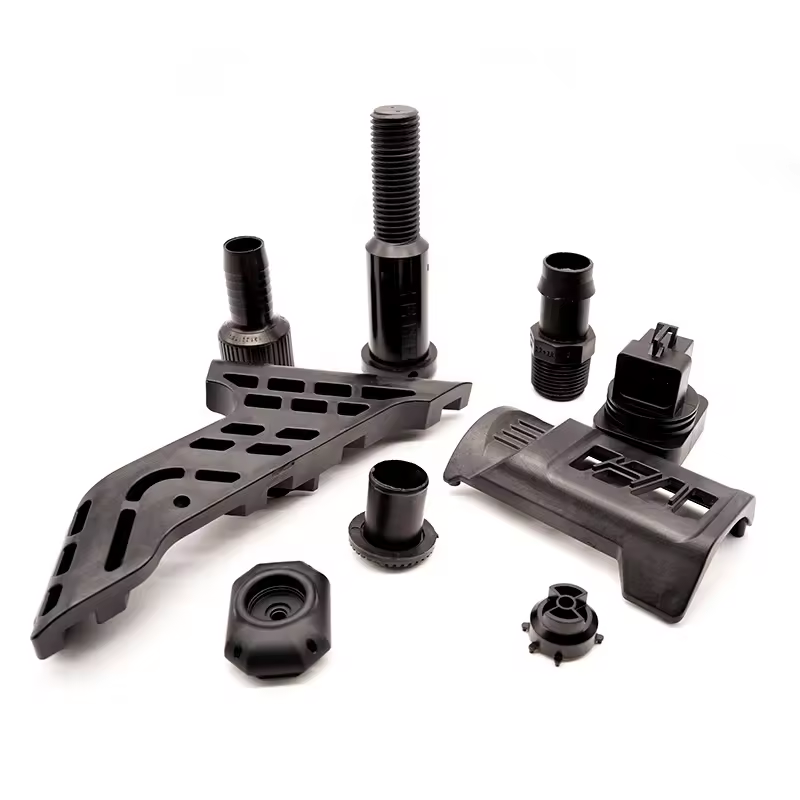
Energy Consumption:
- ABS: 85–100 MJ/kg
- Polypropylene (PP): 70–85 MJ/kg
- Polycarbonate (PC): 110–130 MJ/kg
3. Is ABS Plastic Safe?
Safety is a critical concern for any material used in consumer-facing products. ABS plastic is generally considered safe due to its chemical inertness and stability under normal use conditions. Extensive research and regulatory assessments have confirmed that ABS does not leach harmful substances during everyday use. This makes it particularly suitable for products in close contact with humans—from automotive components and electronic housings to toys and kitchen appliances.
ABS is FDA-compliant for food-contact applications and certified non-toxic by the CPSC for toys.

Safety Factors:
- No BPA/Phthalates: Unlike PVC, ABS avoids endocrine-disrupting additives.
- Thermal Stability: Minimal off-gassing below 80°C.
- Leaching Tests: <0.1 ppm styrene migration (FDA limit: 0.5 ppm).
Case Study: A U.S. toy manufacturer reduced recalls by 60% after switching to ABS from PVC.
4. Common Applications for ABS
ABS plastic is also a widely used material for injection molding due to its excellent balance of properties, which includes good impact resistance, durability, and ease of processing. That is why everyone commonly uses it, from the automotive to the consumer electronics industry. For example, ABS is commonly used in the automotive sector, where dashboard molding and interior trim components must withstand high-impact and low-temperature situations without losing their shape or integrity. In the consumer electronics sector, you’ll commonly find ABS used to produce printer housings, remote controls, and enclosures for power tools, where a smooth finish and accurate molding are paramount. This quality makes ABS plastic equally well-suited for the toy industry, where creating non-toxic, durable products is paramount. This is evident in products like action figures and building blocks.

Industry | Use Case | Benefit |
Automotive | Dashboard panels | Impact resistance, UV stability |
Electronics | Keyboard keys | Rigidity, aesthetic finish |
Medical | Device housings | Sterilizability (autoclave-safe) |
Toys | LEGO bricks | Non-toxic, colorfast |
5. ABS vs. Other Materials
The most significant competition for ABS plastic is against other commercial polymer materials like polycarbonate (PC), polypropylene (PP), and polyethylene (PE). These materials have unique strengths, but ABS tends to be the middle ground. While polycarbonate has better clarity and impact resistance, it is typically more expensive and less resistant to surface scratches, for example. Polypropylene and polyethylene, while boasting chemical resistance and flexibility, don’t have the rigidity and aesthetic benefits that ABS does.
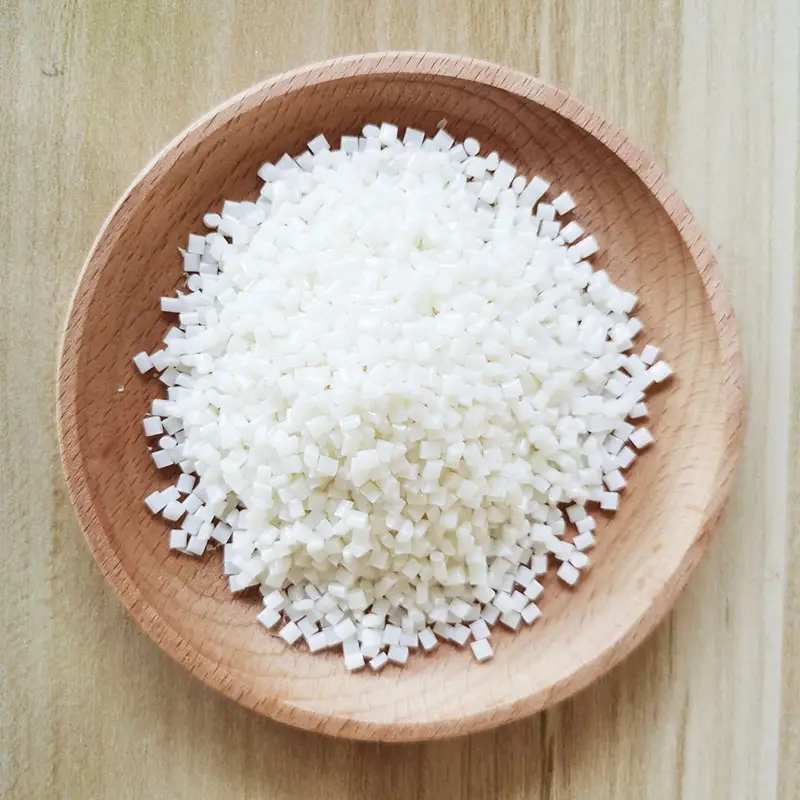
Property | ABS | PC | PP |
Impact Strength | High | Very High | Low |
Cost ($/kg) | 2.5–3.5 | 4.5–6.0 | 1.8–2.5 |
Recyclability | Moderate | Low | High |
UV Resistance | Fair | Excellent | Poor |
6. Environmental Impact of ABS
- Recycling Rate: 18–22% in the U.S. (vs. 30% for PET).
- Challenges: Limited closed-loop systems; 65% of ABS ends in landfills.
Innovations:
- Chemical Recycling: Breaking ABS into monomers (70% yield).
- Bio-ABS: 30% plant-based content (e.g., Terluran® ECO).
7. Regulatory Compliance in the US
- FDA: Food Contact Substance Notification (FCN) for kitchenware.
- CPSC: ASTM F963-17 certification for toys.
- UL 94: V-0 flammability rating for electronics.
8. Cost of ABS Plastic in Injection Molding
Regarding cost, ABS plastic is an economical material option compared to other high-performance thermoplastics, which is an attractive option for mass production. Based on grades and market conditions, ABS resin usually costs around $1.50 to $3.00 per pound. Like other thermoplastics, the costs of injection molding with ABS depend on factors like mold design complexity, cycle times, and production volume.
For instance, a high-volume run of simple enclosures for consumer products can achieve low per-unit costs through economies of scale, whereas well-detailed custom parts that require complex tooling and initial mold costs belong here. To achieve cost efficiency, these costs are typically amortized across large production runs, demonstrating how ABS plastic continues to be an affordable material for a wide range of manufacturing applications.
Conclusion
ABS plastic remains a versatile, safe choice for manufacturers, balancing performance with regulatory compliance. While its environmental footprint poses challenges, advancements in recycling and bio-based alternatives pave the way for sustainable use.