In the ever-evolving world of manufacturing, optimizing processes and reducing costs are paramount. One crucial concept that has gained traction in recent years is Design for Manufacturing (DFM).
In this blog post, we will delve into the principles of DFM and explore how it applies to injection molding, highlighting its benefits in optimizing the manufacturing process and reducing overall costs.
Understanding Design for Manufacturing (DFM)
Design for Manufacturing (DFM) is a comprehensive approach that involves designing products with the manufacturing process in mind. The primary goal of DFM is to simplify product designs to make them easier and more cost-effective to manufacture without compromising on quality or functionality.
By considering the manufacturing process during the design phase, companies can identify potential issues early and make necessary adjustments, leading to more efficient production and reduced costs.

Principles of DFM
The principles of DFM are centered around creating designs that are easy to manufacture. Here are some key principles:
- Simplification of Design: The more complex a design, the more challenging and costly it is to manufacture. Simplifying designs by reducing the number of parts, using standard components, and minimizing intricate features can significantly streamline the manufacturing process.
- Material Selection: It is crucial to choose the right materials that are readily available, cost-effective, and suitable for the manufacturing process. The selected materials should also meet the functional requirements of the final product.

- Standardization: Using standard parts and components can reduce costs and lead times. Standardization also simplifies inventory management and improves compatibility with existing manufacturing processes.
- Ease of Assembly: Designing products that are easy to assemble can reduce labor costs and minimize assembly errors. Features like snap-fit joints, self-locating parts, and minimized fasteners contribute to easier assembly.
- Tolerance and Fits: Properly defining tolerances and fits ensures that parts fit together as intended without excessive adjustments or rework. Overly tight tolerances can drive up manufacturing costs and complexity.
- Design for Testing and Quality Control: Incorporating features that facilitate testing and inspection during and after manufacturing can help identify defects early, ensuring high-quality products.
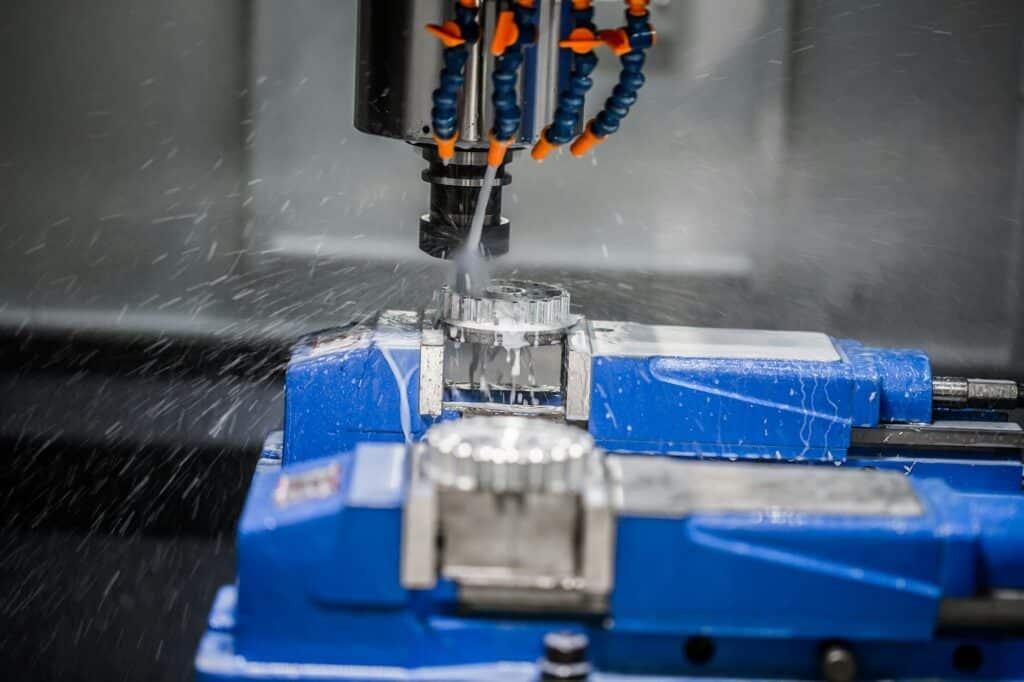
Application of DFM in injection molding
Injection molding is a popular manufacturing process for producing a wide range of plastic parts. Applying DFM principles to injection molding can lead to substantial efficiency and cost-reduction benefits.
- Optimizing Part Design:
- Uniform Wall Thickness: Maintaining consistent wall thickness throughout the part helps in avoiding defects like warping and sink marks. It also ensures uniform cooling and reduces cycle times.
- Draft Angles: Incorporating appropriate draft angles facilitates easier ejection of the part from the mold, reducing the risk of damage and improving cycle times.
- Ribs and Gussets: Adding ribs and gussets can enhance the structural integrity of the part without increasing material usage. These features also aid in uniform cooling and reduce the risk of warping.
- Material Considerations:
- Material Selection: Choosing the right material for the part based on its mechanical, thermal, and chemical properties is crucial. The selected material should also be compatible with the injection molding process.
- Recyclability: Considering the recyclability of materials can contribute to sustainable manufacturing practices and reduce material costs.
- Simplified Mold Design: Designing molds with fewer components and simpler mechanisms can reduce manufacturing and maintenance costs. It also leads to shorter lead times for mold fabrication.
- Cooling Channels: Optimizing the design of cooling channels within the mold ensures efficient heat dissipation, reducing cycle times and improving part quality.
- Gate Design: Proper gate design is essential for ensuring uniform filling of the mold cavity, minimizing defects, and reducing cycle times.
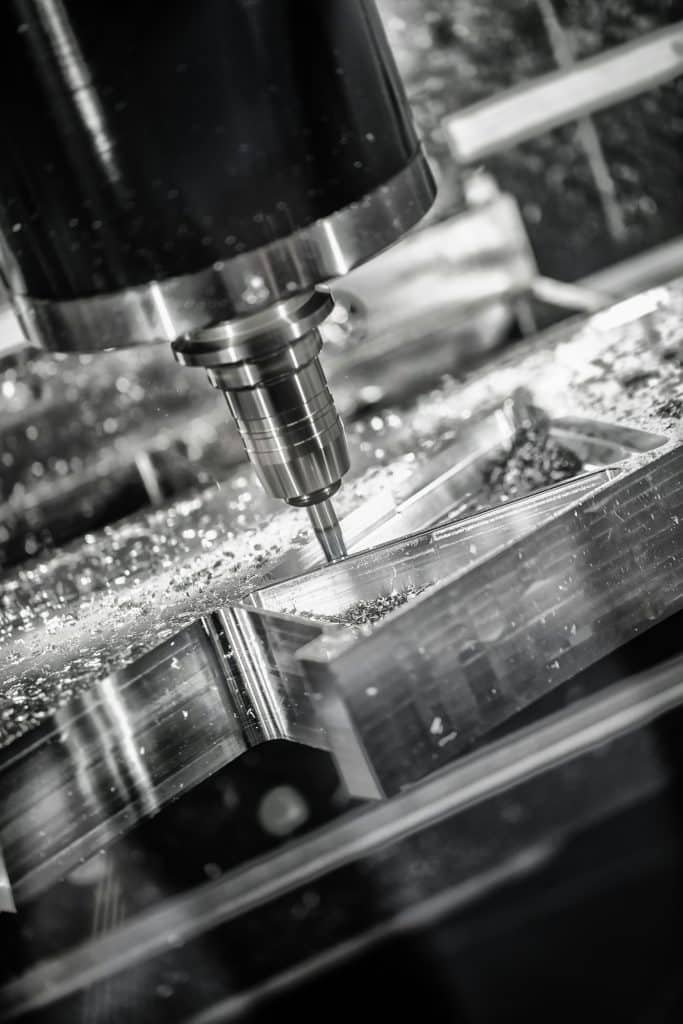
- Process Optimization:
- Cycle Time Reduction: Designing parts and molds that enable faster cycle times can significantly increase production efficiency. This can be achieved through optimized cooling, efficient ejection systems, and streamlined mold design.
- Automation: Incorporating automation in the injection molding process can reduce labor costs and improve consistency. Automated systems for material handling, part extraction, and quality control enhance overall efficiency.
- Cost Reduction Strategies:
- Material Efficiency: Minimizing material usage through optimized part design and mold layout can lead to significant cost savings.
- Waste Reduction: Implementing strategies to reduce waste during the injection molding process, such as reusing scrap material and optimizing process parameters, can lower overall production costs.
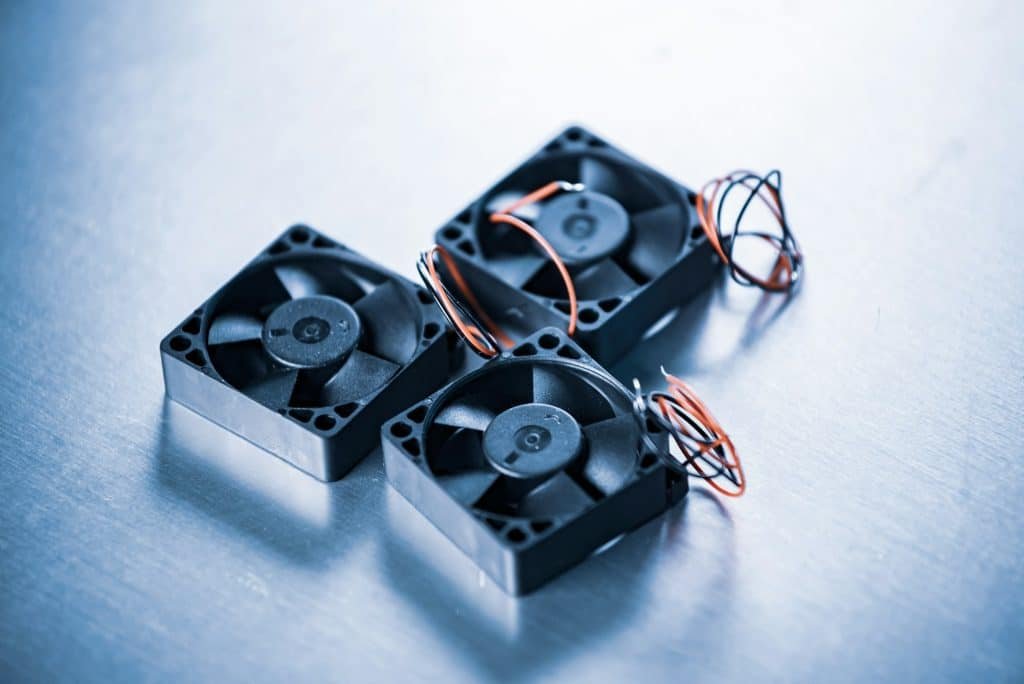
Conclusion
Design for Manufacturing (DFM) is a powerful approach that, when applied to injection molding, can lead to significant improvements in efficiency, quality, and cost reduction. By considering the manufacturing process during the design phase, companies can create products that are easier and more cost-effective to produce. This not only enhances competitiveness but also ensures the delivery of high-quality products to customers.
At BFY Mold, we specialize in injection molding and mold manufacturing, offering a range of services including mass production, on-demand production, CNC machining, and mirror spark. With our factory and a commitment to excellence, we are dedicated to providing innovative solutions that meet the unique needs of our clients. Contact us today to learn more about how we can help optimize your manufacturing processes.
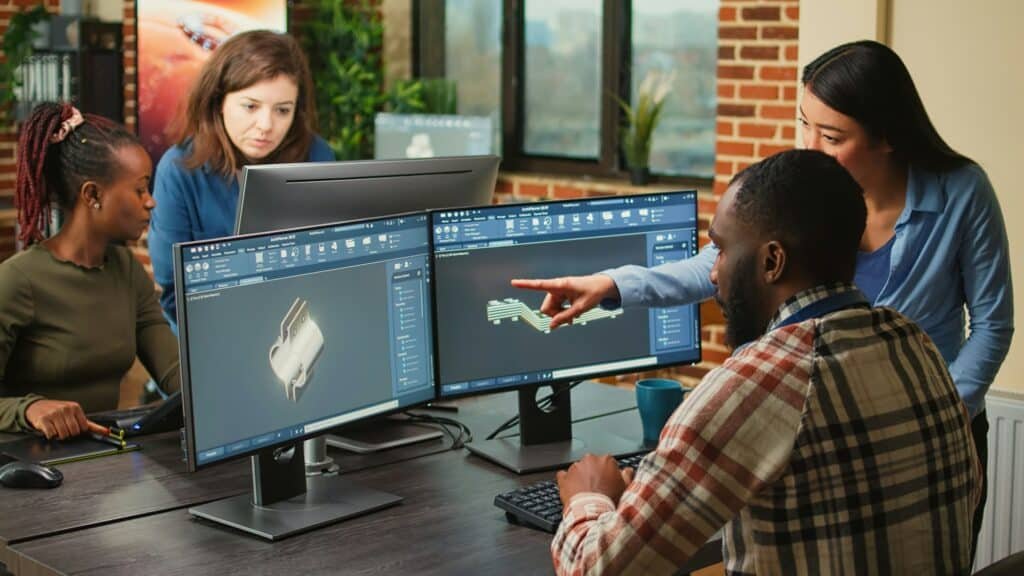
10 FAQs For DFM in Injection Molding
1. What DFM Principles Reduce Injection Molding Costs?
Adopt uniform wall thickness (1.5–3.0 mm) and draft angles (1–3°) to cut tooling expenses by 20–35% while preventing defects.
2. How Do Top Suppliers Implement DFM for Complex Geometries?
Advanced vendors use Moldflow simulations to optimize gate locations, minimizing weld lines and sink marks in multi-cavity molds.
3. Which Material Choices Align with DFM Best Practices?
Material | DFM Advantage | Cycle Time Reduction |
Polypropylene | Low shrinkage (1.5–3.0%) | 15–25% |
ABS | Easy ejection (low sticktion) | 10–20% |
4. How to Validate a Supplier’s DFM Expertise?
Demand case studies showing:
- ≥30% cost reduction via part consolidation
- GD&T compliance
5. What DFM Guidelines Prevent Common Injection Molding Defects?
- Sink Marks: Maintain rib-to-wall ratio ≤60%
- Warpage: Use conformal cooling channels (±0.1°C uniformity)
6. How Does DFM Impact Tooling Lead Times?
AI-driven DFM analysis cuts mold design time from 2 weeks to 3–5 days.
7. Can DFM Strategies Support Sustainable Manufacturing?
Yes:
- Material-saving designs (nesting optimization)
- Bio-based resins (e.g., PA610 with 60% renewables)
8. What DFM Metrics Do Automotive Suppliers Prioritize?
- Tooling life ≥500k cycles (H13 steel, HRC 48–52)
- Cycle time ≤30 seconds for high-volume parts
9. How to Transition Prototypes to Production Using DFM?
Leverage aluminum prototype molds (5k–10k cycles) to validate designs before investing in hardened steel tools.
10. What DFM Software Tools Do Experts Recommend?
- Siemens for tolerance stack analysis
- SolidWorks Plastics for fill pattern prediction