Injection-molded products can change color due to several factors:
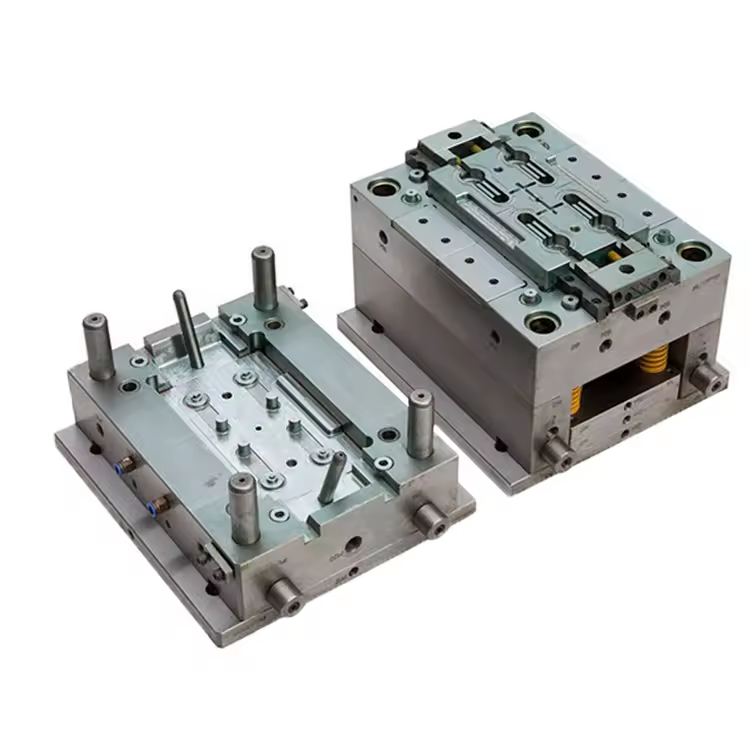
Reasons for discoloration of plastic products:
1. Plastic and pigment mixed with debris;
2. Plastic and pigment pollution or degradation, decomposition;
3. The pigment quality is not good or the mixing is not uniform when used;
4. The temperature of the barrel and nozzle is too high, which makes the rubber material burnt and discolored;
5. The injection pressure and speed are set too high, causing the additives and colorants to decompose;
6. Mold surface moisture, oil, or excessive use of release agent;
7. Uneven distribution of fiber fillers, products, and solvent contact resin loss, so that the fiber is bare;
8. There are obstacles in the melt tube to promote material degradation.

Plastic products discoloration solution:
1. Avoid mixing with debris when mixing;
2. The raw materials should be dry, the equipment should be clean, and the refueling should be cleaned to avoid leaving excess materials;
3. To ensure the quality of all pigments, the pigments should be evenly attached to the surface of the particles when mixing;
4. Reduce the melting tube and nozzle temperature to remove burnt glue material.
5. Reduce the injection pressure and speed parameter values to avoid the decomposition of additives;
6. Dry the surface of the mold with water and oil, rational use of release agent;
7. Set the process parameters of the fiber filler reasonably, use the solvent reasonably, make the plasticization good, and eliminate the fiber exposure;
8. Pay attention to the removal of obstacles, especially for refueling, to strictly follow the step procedure or use the transition refueling method.