Injection molding, an unparalleled important manufacturing process, has revolutionized plastic components manufacturing across industries. Whether it be high-end medical devices or low-end consumer goods, the stability of finished products after injection molding is a staple of reliability, functionality, and uniformity. The following exploration seeks to, at a point-by-point level, break down the parts that, as a whole, create the stability of an injection-molded product.
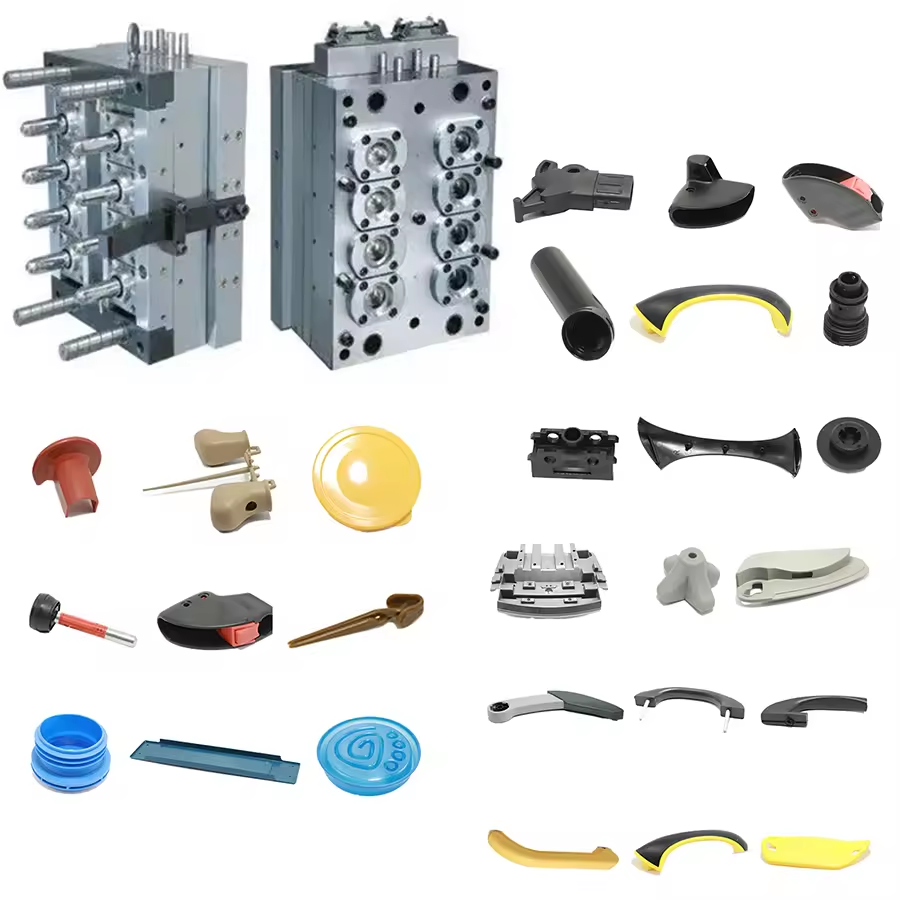
Injection Molding Products
1. Injection Molding Material Selection: The Genesis of Stability
Melting Temperature: The starting point in achieving stability lies in selecting a material with an optimal melting temperature. This crucial parameter ensures that the material can be effectively transformed from a solid to a molten state during the injection molding process, laying the foundation for successful molding.
Flowability: The ease with which molten plastic flows within the mold is determined by the Melt Flow Index (MFI) or Melt Mass Flow Rate (MFR). A judicious choice of material with appropriate flow properties ensures that intricate details are faithfully replicated in the finished product, contributing to its stability.
Shrinkage: Understanding and managing shrinkage is imperative for maintaining dimensional stability. By selecting materials with predictable shrinkage characteristics, manufacturers can compensate for the natural contraction that occurs during the cooling phase, preventing deviations from design specifications.
Mechanical Properties: Tensile strength, flexural strength, and impact resistance are pivotal mechanical properties that influence the functionality and durability of the finished product. Tailoring material selection to match the mechanical demands of the application enhances the stability and performance of injection-molded products.
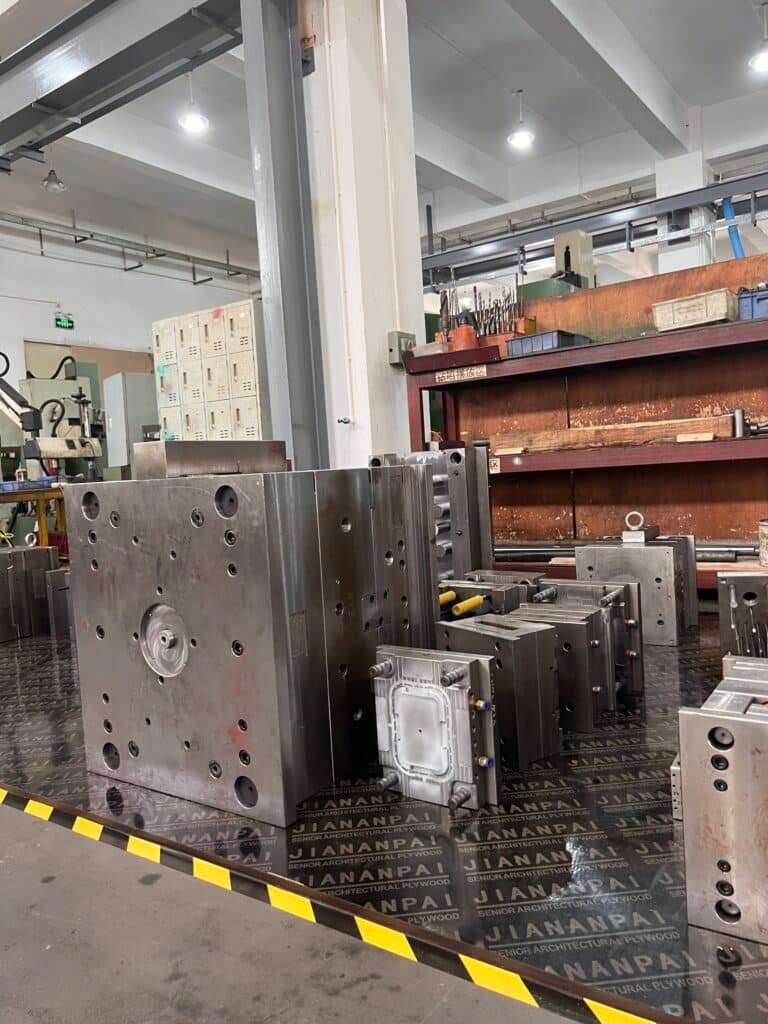
Injection Mold
2. Injection Molding Process Optimization: Precision at Every Stage
Temperature Control:
The injection molding process involves a delicate balance of temperatures, from melting the raw material to cooling the molded product. Maintaining precise temperature control throughout ensures consistent material behavior, minimizing defects and enhancing product stability.
Injection Pressure and Speed:
Mold filling is critical, requiring precise calibration of injection pressure and speed to prevent defects like flash or incomplete filling, thus ensuring process stability.
Cooling Rates:
Controlled cooling rates are pivotal in influencing the material’s crystallinity and, consequently, its mechanical properties. Careful cooling minimizes warping risk and preserves the material’s intended shape, improving the finished product’s stability.
Mold Design and Maintenance:
The design and maintenance of the mold are integral aspects of process optimization. A well-designed mold maintained regularly reduces defects and inconsistencies, stabilizing the injection molding process.
3. Molding Quality Assurance: Safeguarding Stability
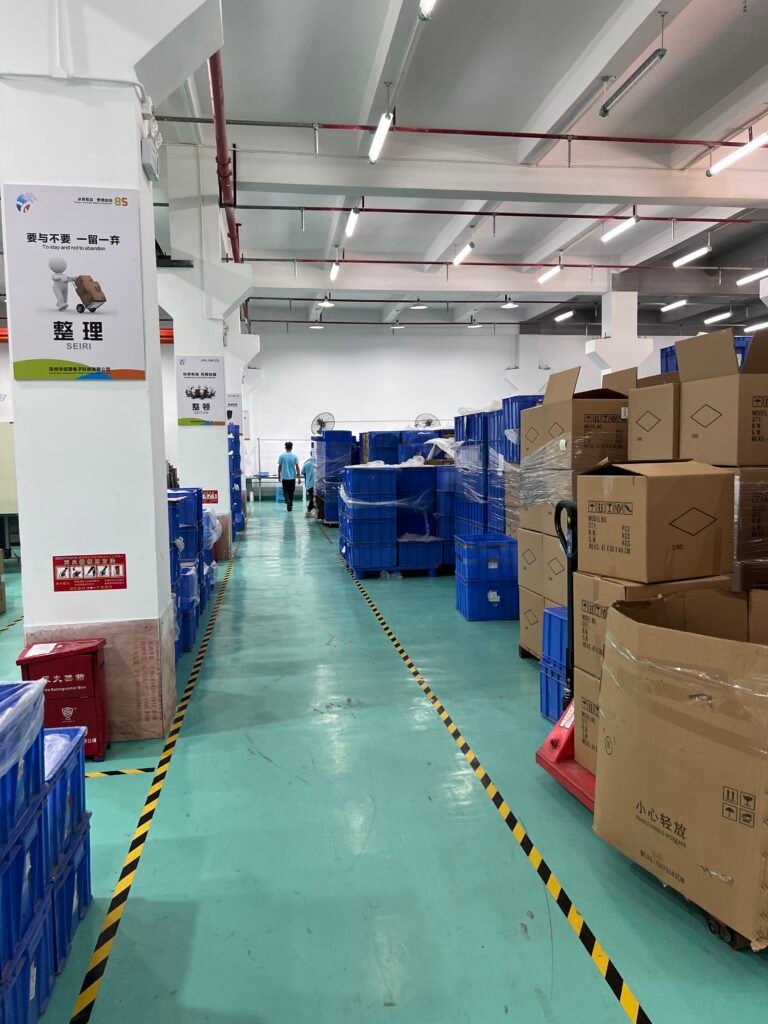
injection mold company
Testing and Inspection Protocols
Robust testing and inspection protocols are essential to identify deviations from specifications early in the process. Dimensional checks, visual inspections, and non-destructive tests verify product adherence to standards, enhancing finished product stability.
Traceability
Documenting material batches, process parameters, and production data facilitates swift issue identification and resolution. Traceability is a key factor in enhancing the stability and consistency of the manufacturing process.
Employee Training and SOP Adherence
Skilled and knowledgeable operators contribute to the precision and repeatability of the injection molding process.
Employee training and adherence to standardized procedures are key to quality assurance, guaranteeing stability in finished product production.
Conclusion
The overall stability of injection-molded products relies on careful material selection, process optimization, and quality control practices. Every point in this exploration is a hallmark in the quest for quality, consistency, and reliable products. With mass production in mind, the industry constantly looks for stability in the injection process.