1. 3D Cavity & Core Design in Precision Mold Manufacturing
The internal and external shapes of the plastic parts are directly injection-molded by the cavity and the core of the plastic mold. The shape of the cavity and the core is also the reaction of the plastic parts. These complex three-dimensional shapes are difficult to process, especially the product surface processing in the blind area of the cavity, which is enhanced by the common machine tool. This not only requires high technical level workers, a variety of auxiliary tools to be more, and a long processing cycle.

2. High-Precision Tooling for Mold Manufacturing Standards
The dimension precision of the cavity and core of modern mold is generally required to be IT8-9, and the dimension precision of the cavity and core of precision mold for plastic parts is required to be IT6-7, a part of the accuracy of IT7-8. In addition, the mold on the size of each mechanism must be very high requirements to make the mold open and close reliable. So after the development of mold to adopt high-precision mold processing and product measurement means to reduce errors.
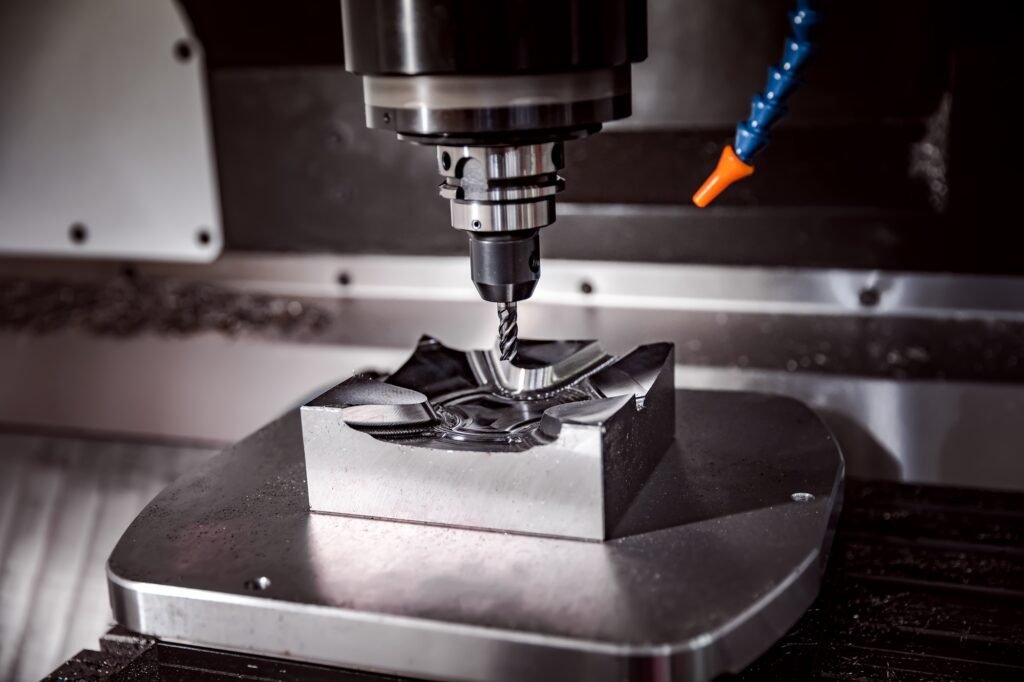
3. Surface Finish Excellence in Mold Manufacturing
The surface roughness of modern mold cavities and cores is generally Ra0.2-0.1um, and the surface roughness of the cavity of the mirror finish mold is lower than Ra0.05um, to meet the roughness requirements, the surface of the cavity and core must be refined and polished by an electric pulse. However, most of them are manually polished at present, and the workload of the manual part accounts for about 40% of the whole mold. If you want to improve the service life of the mold, some molding parts also need to be quenched.
4. Advanced Mold Tooling Performance for Demanding Applications
As the performance of the mold material is getting better and better, the tooling requirements for mold processing are also getting higher and higher. Some excellent alloy materials and improved tool designs are often used. In addition, to improve processing efficiency and reduce losses. It is also necessary to redesign and modify the tool to meet the fast-paced mold processing requirements.
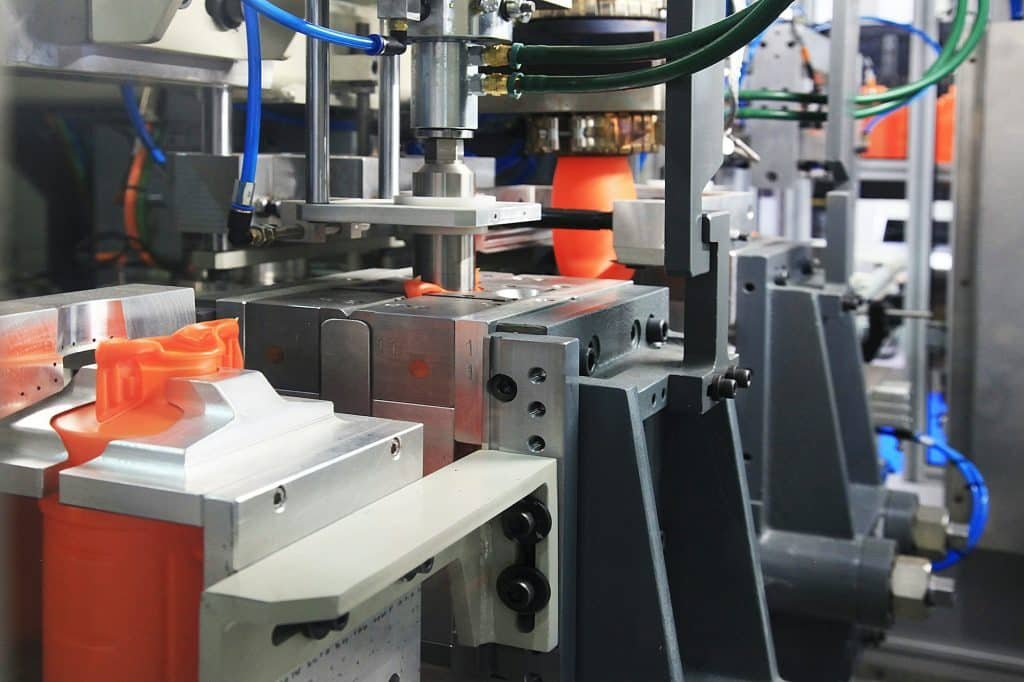
5. Efficient Process Flow for Rapid Mold Manufacturing
The forming part of the plastic mold is composed of a cavity, a core, a slider, an inclined guide column, etc.. Fixed mold and dynamic mold are by the ceiling and cavity, floor and core, and other components of the combination. To ensure the accuracy of the shape and position of the plates, the matching method is needed. Many kinds of work, many processes, and long process flow.
As the injection mold is related to product replacement and market speed, generally given the mold manufacturing time is relatively short. Therefore, mold manufacturing requires minimized manual operation, improved automation, and fast and excellent rapid molding.