Injection molding is a widely used manufacturing process for producing plastic components. One of the most commonly used plastics in this process is polycarbonate (PC), known for its strength, durability, and transparency. The successful production of high-quality pc products through injection molding largely depends on the careful control of various parameters. PC Injection molding temperature is a key factor.
Melt Temperature
Definition and Importance
The melt temperature refers to the temperature at which the polycarbonate material is melted before being injected into the mold. This temperature is crucial because it directly affects the material’s flow properties, ensuring that it fills the mold cavity completely and uniformly.
Optimal Melt Temperature for PC Products
Polycarbonate has a relatively high melt temperature, typically between 260°C and 310°C. The exact temperature within this range depends on the specific grade of PC being used and the desired characteristics of the final product. Maintaining the optimal melt temperature is essential to avoid issues such as incomplete filling, surface defects, or material degradation.

Consequences of Incorrect Melt Temperature
If the melt temperature is too low, the viscosity of the PC will be too high, leading to poor flow and incomplete mold filling. On the other hand, if the melt temperature is too high, it can cause thermal degradation, resulting in a reduction of the mechanical properties and aesthetic quality of the final product.
Mold Temperature
Role of Mold Temperature
Mold temperature is another critical parameter in the injection molding process. It influences the cooling rate of the molten polycarbonate and subsequently the quality of the molded part. Proper control of mold temperature ensures dimensional stability, surface finish, and mechanical properties.
Optimal Mold Temperature for PC Products
For polycarbonate, the mold temperature typically ranges from 80°C to 120°C. The precise temperature setting depends on the complexity of the part, wall thickness, and the desired cycle time. A higher mold temperature can improve the surface finish and reduce residual stresses, while a lower mold temperature can shorten the cycle time but may affect the quality of the part.
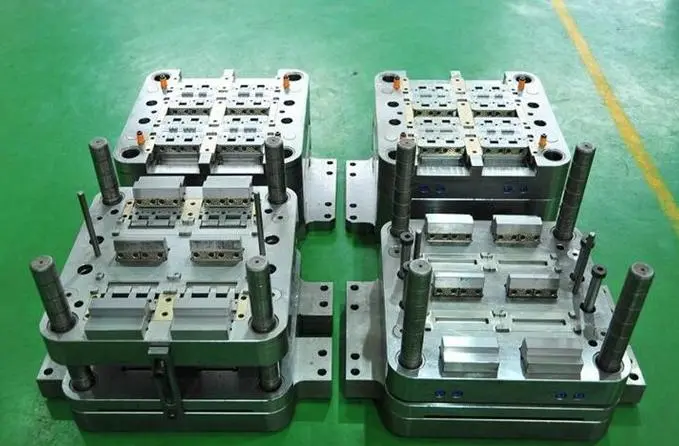
Impacts of Mold Temperature on Product Quality
Maintaining the correct mold temperature is crucial for preventing defects such as warping, sink marks, and internal stresses. An inadequately controlled mold temperature can lead to parts with poor dimensional accuracy and surface imperfections, compromising the performance and appearance of the final product.
Barrel Temperature
Barrel Temperature Zones
The barrel of the injection molding machine is divided into several heating zones, each with its specific temperature setting. These zones include the feed zone, compression zone, and metering zone. The temperature profile along the barrel is carefully controlled to ensure consistent melting and homogenization of the polycarbonate material.
Temperature Settings for PC Products
For polycarbonate, the barrel temperatures generally range from 240°C to 310°C. The feed zone is usually set at a lower temperature to facilitate the feeding of solid granules, while the compression and metering zones are set at higher temperatures to ensure thorough melting and mixing of the material.
Effect of Barrel Temperature on Processing
Properly controlling the barrel temperature is essential for achieving a uniform melt and preventing thermal degradation. Inconsistent or incorrect barrel temperatures can lead to issues such as unmelts (solid particles in the melt), poor surface finish, and reduced mechanical properties.
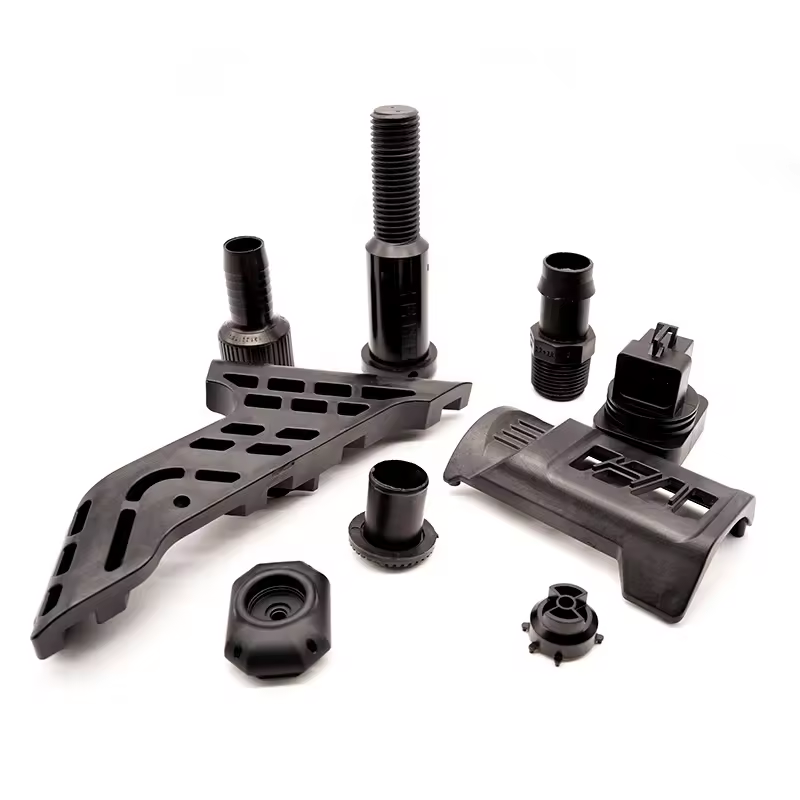
Cooling Rate and Its Impact
Cooling Rate Control
The cooling rate of the molded part is determined by the mold temperature and the cooling system design. Controlling the cooling rate is essential for achieving the desired crystallinity, shrinkage, and dimensional stability of the part.
Impact on Polycarbonate Properties
Polycarbonate is an amorphous polymer, meaning it does not crystallize during cooling. However, the cooling rate still significantly affects its properties. Rapid cooling can induce higher residual stresses, leading to warping and reduced mechanical performance. Conversely, slow cooling allows for stress relaxation and results in parts with better dimensional stability and mechanical properties.

Thermal Stability and Degradation
Thermal Degradation Risks
Polycarbonate is sensitive to thermal degradation, which can occur if the material is exposed to high temperatures for prolonged periods. Degradation can lead to discoloration, loss of mechanical properties, and reduced transparency.
Preventive Measures
To minimize thermal degradation, it is crucial to avoid excessive residence times in the barrel and to maintain the melt temperature within the recommended range. Additionally, stabilizers can be added to the polycarbonate to enhance its thermal stability.
Conclusion
In the injection molding of polycarbonate products, precise temperature control is paramount to producing high-quality parts. The melt temperature, mold temperature, barrel temperature, and cooling rate all play critical roles in determining the final properties of the molded part. By carefully managing these temperature parameters, manufacturers can ensure that their PC products exhibit the desired mechanical properties, dimensional accuracy, and surface quality. Understanding and optimizing temperature requirements is thus essential for successful injection molding of polycarbonate products.